Imagine a world where rigging operations are not only safer but also more efficient and versatile. Welcome to the revolutionary realm of synthetic fiber ropes in rigging applications. As traditional steel wire ropes fade into the background, a new champion emerges, boasting superior strength, enhanced safety features, and unparalleled user-friendliness.
Did you know that a synthetic fiber rope can be up to 15 times stronger than steel by weight? This astounding fact is just the tip of the iceberg when it comes to the advantages of modern rigging wire rope. From construction sites to maritime operations, these innovative ropes are transforming the way we approach challenging lifting and securing tasks.
In this post, we'll delve into the game-changing benefits of rigging wire made from synthetic fibers. We'll explore how these cutting-edge materials outperform their steel counterparts in strength, safety, and versatility. Whether you're a seasoned rigging professional or simply curious about the latest advancements in industrial technology, prepare to be amazed by the potential of wire rope for rigging in the 21st century.
Join us as we unravel the future of rigging technology and discover why synthetic fiber ropes are quickly becoming the go-to choice for industry leaders worldwide. It's time to elevate your rigging game – are you ready for the revolution?
Fiber Ropes vs Steel Wire Ropes: A Strength Comparison
When it comes to rigging applications, the battle between fiber ropes and traditional steel wire ropes has been heating up. As someone who's spent years in the rigging industry, I've witnessed firsthand the remarkable evolution of rope technology. Let me take you on a journey through the world of high-strength fibers and explain why they're revolutionising the rigging game.
The Superior Strength of Dyneema Fiber Ropes
Picture this: a rope as thin as your finger, yet strong enough to lift a small car. That's the power of Dyneema, the crown jewel of synthetic fibers. Dyneema fiber ropes are not just strong; they're astonishingly strong, boasting a strength-to-weight ratio that leaves steel wire ropes in the dust.
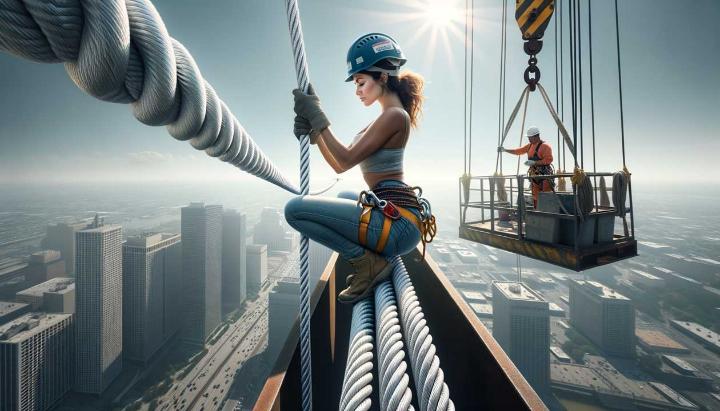
But what makes Dyneema so special? It's all in the molecular structure. These ultra-high-molecular-weight polyethylene (UHMWPE) fibers are engineered to perfection, resulting in a material that's up to 15 times stronger than steel by weight. Imagine the possibilities this opens up for rigging applications!
Advantages of Fiber Ropes Beyond Strength
Now, you might be thinking, "Strength is great, but what about other factors?" Well, fiber ropes have got you covered there too. Let's break it down:
- Lightweight wonder: Fiber ropes are incredibly light, making them a breeze to handle and transport. Your back will thank you!
- Flexibility that feels like magic: Unlike rigid steel wires, fiber ropes bend and flex with ease, adapting to your rigging needs like a dream.
- Safety first: No more worrying about sharp edges or frayed wires. Fiber ropes are smooth and splinter-free, reducing the risk of injuries.
But here's the kicker - fiber ropes, especially those made from HMPE (High-Modulus Polyethylene) like Dyneema, offer superior resistance to abrasion, chemicals, and UV radiation. This means they'll keep performing at their best, even in harsh environments. Discover more about the advantages of high-tensile strength nylon ropes in similar demanding conditions.
Have you ever considered how these advantages could transform your rigging operations? The possibilities are endless, from improved efficiency to enhanced safety for your team.
Did you know? A 12mm Dyneema fiber rope can have the same breaking strength as a 20mm steel wire rope, while weighing only a fraction as much!
As we dive deeper into the world of fiber ropes, you'll discover how these incredible materials are reshaping the rigging industry. Stay tuned for more insights on how you can leverage the power of synthetic fiber ropes in your operations! Explore how fiber rope winch machines can revolutionize your rigging tasks by checking out our dedicated post on the advantages of fiber rope winch machines.
Enhanced Safety Features of Rigging Wire Rope
When it comes to rigging applications, safety is paramount. As someone who's been in the industry for years, I've seen firsthand how the right equipment can make all the difference. Let's dive into the enhanced safety features that make rigging wire rope a game-changer in the field.
Strength and Durability Advantages
Rigging wire rope isn't just about lifting heavy loads; it's about doing so with confidence. The unique construction of wire rope, with its multiple strands twisted together, creates a synergy of strength that's hard to beat. This intricate design allows for:
- Superior load distribution: The twisted strands work together to spread the weight evenly, reducing stress on any single point.
- Exceptional abrasion resistance: The outer wires act as a protective layer, extending the rope's lifespan even in harsh conditions.
- Impressive load conformity: Wire rope adapts to the shape of the load, providing a secure grip that minimizes the risk of slippage.
I remember a project where we were lifting delicate machinery in a corrosive environment. The wire rope's durability and resistance to chemical damage were crucial in ensuring a safe operation from start to finish.
Safety Factors and Load Capacity
Understanding safety factors is crucial when working with rigging wire rope. Have you ever wondered why we don't simply use a rope rated for the exact weight we're lifting? Here's why:
Wire rope slings typically have a 5:1 safety factor. This means they're designed to handle five times the weight they're rated for, providing a crucial safety margin.
This safety factor is not just a number—it's peace of mind. It accounts for unexpected dynamic loads, wear and tear, and other unforeseen circumstances that could compromise safety.
When determining the working load limit (WLL) and breaking strength of wire rope, we consider various factors:
- Rope diameter and construction: Thicker ropes and certain constructions offer higher strength.
- Material grade: Higher-grade steel provides increased tensile strength.
- Environmental conditions: Factors like temperature and exposure to chemicals can affect performance.
It's crucial to follow OSHA guidelines for wire rope inspection and removal. Regular checks for signs of wear, corrosion, or damage are essential. I always tell my team: "When in doubt, take it out." It's better to replace a rope than risk a catastrophic failure.
By understanding and respecting these safety features and guidelines, we can ensure that rigging wire rope continues to be a reliable and secure choice for lifting operations. Remember, in rigging, safety isn't just a priority—it's the priority.
Synthetic fiber ropes are more versatile and user-friendly
As someone who's spent years working with various rigging materials, I can confidently say that synthetic fiber ropes have revolutionised the industry. Their versatility and user-friendly nature make them a game-changer for riggers across the globe. Let me share with you why these modern marvels are quickly becoming the go-to choice for professionals and enthusiasts alike.
Lightweight champions: Easier handling and transportation
Picture this: you're on a job site, and you need to move your rigging equipment up several flights of stairs. With traditional steel wire ropes, this task would be a back-breaking ordeal. But synthetic fiber ropes? They're a breath of fresh air. I remember the first time I swapped out my steel cables for a set of high-strength polyester ropes. The difference was night and day.
- Effortless mobility: These ropes are so light, you can easily coil them up and sling them over your shoulder.
- Reduced fatigue: Less weight means less strain on your body, allowing you to work longer and more efficiently.
- Improved safety: Lighter ropes reduce the risk of accidents during transport and setup.
The lightweight nature of synthetic fiber ropes doesn't just make your job easier; it opens up new possibilities for rigging in hard-to-reach places or weight-sensitive applications.
Flexibility that bends the rules
One of the most striking differences between synthetic fiber ropes and traditional wire ropes is their incredible flexibility. This characteristic isn't just about convenience; it's about expanding what's possible in rigging.
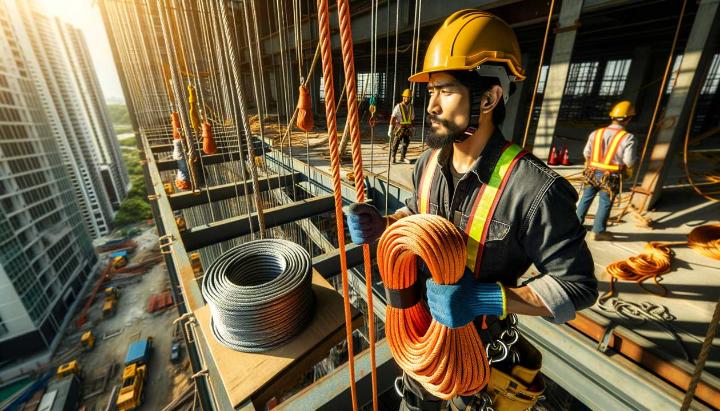
I once worked on a project where we needed to rig around a complex structure with tight corners. With steel wire, it would have been a nightmare. But our synthetic ropes bent smoothly around every obstacle, making the impossible possible. Here's why this flexibility is a game-changer:
- Versatile rigging solutions: You can create intricate setups that conform to challenging environments.
- Knot-friendly: Unlike wire ropes, synthetic fibers can be easily tied and untied without compromising strength.
- Reduced wear and tear: The ability to flex reduces stress on the rope, extending its lifespan.
Toughness that stands the test of time
Now, you might be wondering, "Sure, they're light and flexible, but can they stand up to the harsh conditions of real-world rigging?" The answer is a resounding yes. Modern synthetic fiber ropes are engineering marvels, designed to withstand the toughest challenges.
- Abrasion resistance: Many synthetic fibers outperform steel when it comes to withstanding rough surfaces and edges.
- Chemical resilience: Whether you're working in marine environments or industrial settings, these ropes resist corrosion and degradation.
- UV stability: Unlike natural fibers, high-quality synthetic ropes maintain their strength even after prolonged sun exposure.
I've seen synthetic ropes perform flawlessly in scorching desert heat and freezing arctic conditions. Their ability to maintain strength and flexibility across diverse environments is truly remarkable. For more insights, check out our detailed exploration on the advantages and applications of UHMWPE ropes.
Did you know? Some synthetic fiber ropes can retain up to 90% of their strength even after years of UV exposure, far outperforming traditional materials.
As we continue to push the boundaries of what's possible in rigging, synthetic fiber ropes are leading the charge. Their combination of strength, flexibility, and durability makes them not just a viable alternative to steel wire ropes, but in many cases, the superior choice. Whether you're working in construction, marine applications, or outdoor adventures, these versatile and user-friendly ropes are transforming the way we approach rigging challenges.
Wire rope for rigging can be customized for specific applications
In the world of rigging, one size definitely doesn't fit all. As someone who's spent years working with various rigging setups, I've come to appreciate the incredible versatility that customized wire rope brings to the table. Let's dive into how tailoring wire rope for specific applications can revolutionize your rigging operations.
Types of Wire Rope Customization for Rigging
The beauty of wire rope customization lies in its ability to meet the unique demands of different industries and applications. Here are some key ways we can tailor wire rope to fit your specific needs:
- Strand count and configuration: By adjusting the number and arrangement of strands, we can fine-tune the rope's strength, flexibility, and resistance to abrasion.
- Wire count and diameter: Altering these factors allows us to balance between strength and weight, crucial for applications where every gram counts.
- Core material: From fiber to independent wire rope cores, the choice of core material significantly impacts the rope's performance under load and in challenging environments.
- Specialized coatings: For harsh conditions, we can apply protective coatings that enhance corrosion resistance and extend the rope's lifespan.
I recall a project where we needed a wire rope that could withstand extreme temperature fluctuations in an offshore oil rig. By customizing the strand configuration and applying a specialized coating, we created a rope that not only met but exceeded the client's expectations in terms of durability and performance.
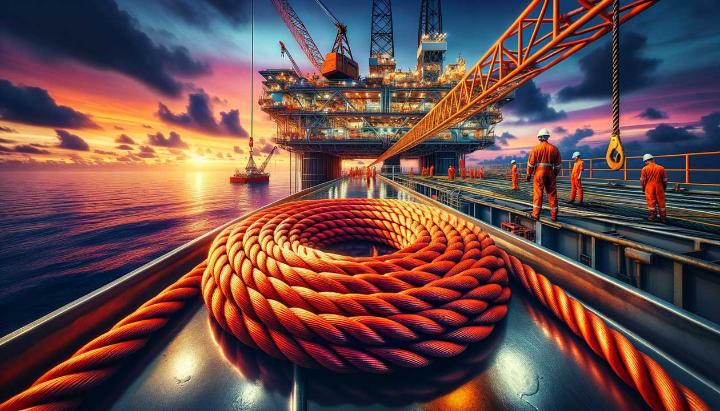
Benefits of Customized Wire Rope in Specific Industries
The advantages of tailored wire rope solutions extend across various sectors. Let's explore how customization benefits some key industries:
- Construction: In high-rise building projects, custom wire ropes with enhanced strength-to-weight ratios allow for safer and more efficient lifting operations.
- Marine: Corrosion-resistant wire ropes tailored for saltwater environments significantly reduce maintenance costs and downtime for shipping companies.
- Mining: Abrasion-resistant wire ropes customized for harsh underground conditions improve safety and extend operational lifespans in challenging mining environments.
But it's not just about industry-specific benefits. Customized wire rope assemblies also offer:
- Improved safety: Tailored solutions mean better load handling and reduced risk of failure.
- Cost-effectiveness: While custom ropes might have a higher upfront cost, their longevity and performance often result in significant long-term savings.
- Enhanced efficiency: Ropes designed for specific tasks can streamline operations and boost productivity.
Did you know? A study by the Wire Rope Technical Board found that properly customized wire ropes can increase operational efficiency by up to 25% in specialized industrial applications.
As we continue to push the boundaries of what's possible in rigging, the ability to customize wire rope for specific applications becomes increasingly crucial. Whether you're lifting massive loads in construction, navigating corrosive marine environments, or tackling the challenges of underground mining, there's a custom wire rope solution waiting to transform your operations.
Have you considered how customized wire rope could revolutionize your rigging practices? The possibilities are as diverse as the industries we serve, and the benefits are too significant to ignore. Let's explore how we can tailor the perfect wire rope solution for your unique needs.
As synthetic fiber ropes like rigging wire ropes gain traction in the industry, they present unparalleled advantages over traditional steel wire ropes. Rigging wire rope, such as those made from Dyneema, offers a remarkable strength-to-weight ratio, making them ideal for heavy loads without the bulk. The safety features of these ropes, including their lighter weight and absence of sharp edges, enhance workplace safety by minimizing injury risks. Additionally, synthetic fiber ropes demonstrate superior versatility and user-friendliness, being easier to handle, more flexible, and resistant to harsh conditions like abrasion and UV exposure. These attributes solidify their place as the preferred choice in modern rigging applications. For those seeking tailored solutions, the customization options for wire rope for rigging, including material selection and specific designs, ensure optimal performance for various unique needs.
Discover the Best Rigging Solution for Your Needs
Fill in the form above to explore how customized rigging wire ropes can enhance your operations, ensuring strength, safety, and efficiency tailored to your specific needs.