Have you ever witnessed a catastrophic rigging failure? It's a heart-stopping moment that no one in the industry ever wants to experience. The difference between a successful lift and a disastrous one often comes down to a seemingly small detail: wire rope sling eye dimensions. At iRopes, we've seen how crucial these measurements are, and we're here to shed light on this often-overlooked aspect of rigging safety.
In the world of heavy lifting, precision isn't just important—it's everything. Whether you're hoisting equipment on an offshore platform or manoeuvring materials on a bustling construction site, the integrity of your wire rope eye can make or break your operation. But here's the kicker: not all eyes are created equal, and that's where the game-changing potential of a hard eye wire rope sling comes into play.
Join us as we dive deep into the world of wire rope sling eye dimensions, exploring why they matter, how they're measured, and how iRopes' custom solutions are revolutionising safety and efficiency in lifting operations across the globe. Whether you're a seasoned rigger or new to the field, this guide will equip you with the knowledge to make informed decisions that could save lives and streamline your projects. Ready to see rigging through new eyes?
Understanding Wire Rope Sling Eye Dimensions
When it comes to rigging and lifting operations, understanding wire rope sling eye dimensions is crucial for ensuring safety and efficiency. As an experienced rigger, I've seen firsthand how proper eye dimensions can make or break a lift. Let's dive into the nitty-gritty of wire rope sling eyes and why they matter so much.
Measuring Wire Rope Sling Eyes
Accurate measurements are the foundation of safe lifting operations. When measuring a wire rope sling, we always focus on the bearing points - the inside of the eye where the load is actually supported. It's not just about the overall length; the distance between these bearing points is what truly matters.
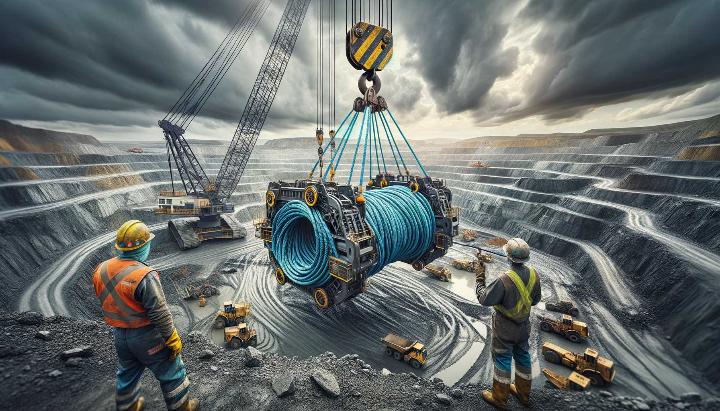
Have you ever wondered why we're so particular about these measurements? It's because even a small discrepancy can significantly impact the sling's performance and safety. For instance, an eye that's too small might not fit properly over the lifting hook, while one that's too large could cause instability during the lift.
Standard Eye Sizes and Specifications
While custom sizes are available, many industries rely on standard eye dimensions for consistency and interchangeability. Here's a quick reference table of common standard eye sizes:
Wire Rope Diameter | Standard Eye Size |
---|---|
1/4 inch | 3 x 6 inches |
3/8 inch | 4 x 8 inches |
1/2 inch | 5 x 10 inches |
When interpreting these specifications, the first number represents the eye width, while the second indicates the eye length. For example, a 3 x 6 inch eye has a width of 3 inches and a length of 6 inches.
Remember, these standard sizes are just a starting point. The specific requirements of your lifting operation might necessitate custom dimensions. That's where the expertise of companies like iRopes comes into play, offering tailored solutions to meet unique needs.
Always consult with a qualified rigging specialist when selecting wire rope slings for your specific application. The right eye dimensions can significantly enhance safety and efficiency in your lifting operations.
Understanding wire rope sling eye dimensions is more than just numbers on a spec sheet. It's about ensuring every lift is as safe and efficient as possible. By paying attention to these crucial details, we can create a safer work environment for everyone involved in rigging and lifting operations.
Understanding Wire Rope Eye Anatomy
As a rigger with years of experience, I've come to appreciate the intricate design of wire rope eyes. These seemingly simple loops at the end of a wire rope are crucial for safe and efficient lifting operations. Let's delve into the anatomy of a wire rope eye and explore why each component plays a vital role in its performance.
Types of Wire Rope Eyes
Before we dissect the components, it's essential to understand that not all wire rope eyes are created equal. In my time on job sites across Australia, I've encountered three main types:
- Flemish eye: Known for its distinctive teardrop shape, this is the most common type I see in the United States and Australia.
- Turnback eye: This type features a loop formed by turning the rope back on itself and securing it with wire rope clips.
- Hand-tucked eye: A more traditional method where the strands are manually woven back into the rope to form the eye.
Each type has its strengths and ideal applications. For instance, I often recommend Flemish eyes for heavy-duty lifting due to their superior strength and durability.
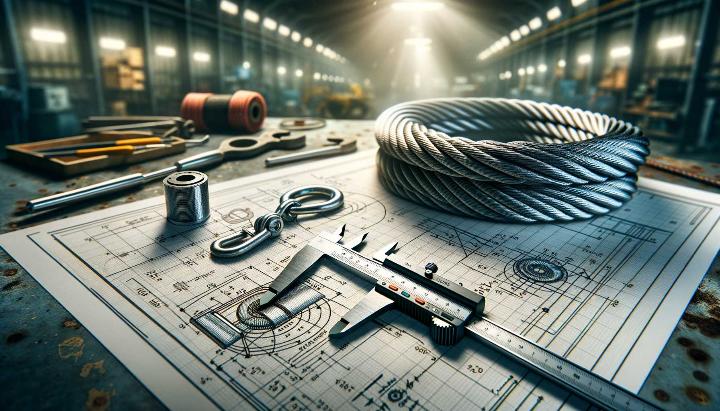
Components of a Wire Rope Eye
Now, let's break down the anatomy of a wire rope eye. Trust me, understanding these components can make a world of difference in your rigging operations:
- Wires: These are the foundation of the wire rope. They're typically made of high-carbon steel and provide the rope's strength.
- Strands: Multiple wires twisted together form strands. The number and arrangement of strands affect the rope's flexibility and strength.
- Core: At the centre of the wire rope is the core, which can be fibre (IWRC) or steel (IWRC). It provides support and helps maintain the rope's shape under load.
- Thimble: This U-shaped fitting inside the eye protects the rope from wear and maintains the eye's shape.
- Splice or Sleeve: This is how the eye is formed and secured. In a Flemish eye, a pressed metal sleeve is often used, providing higher work strength than wire rope clips.
Each of these components plays a crucial role in the wire rope eye's strength and stability. For example, the thimble prevents the eye from deforming under load, while the splice or sleeve ensures the eye can withstand the full strength of the rope.
Remember, the strength of your wire rope sling is only as good as its weakest component. Always inspect all parts of the eye before each use to ensure safety.
At iRopes, we take pride in our high-quality materials and expert craftsmanship when creating wire rope eyes. Our team understands that each component must work in harmony to create a reliable and durable wire rope sling. Whether you need a standard Flemish eye or a custom solution, we're committed to delivering wire rope eyes that meet the highest safety standards and performance requirements. Essential Rope Splicing Fid Kits for UHMWPE Lines can help ensure the integrity of your custom solutions.
Understanding the anatomy of a wire rope eye isn't just about technical knowledge - it's about ensuring the safety of every lift. So, next time you're inspecting a wire rope sling, take a moment to appreciate the engineering that goes into each component. Your keen eye could be the difference between a successful lift and a potential hazard.
Benefits of Using a Hard Eye Wire Rope Sling
As a rigger with years of experience in the field, I've seen firsthand how the right choice of sling can make all the difference in a lift. When it comes to heavy-duty rigging, hard eye wire rope slings are often my go-to choice. Let me walk you through why these robust slings are a game-changer in industrial lifting applications.
Advantages Over Other Sling Types
Hard eye wire rope slings offer a unique combination of strength, flexibility, and durability that sets them apart from other sling types. Here's why they often outperform their counterparts:
- Superior strength-to-weight ratio: Compared to chain slings, hard eye wire rope slings are significantly lighter while maintaining impressive load capacities. This makes them easier to handle and reduces operator fatigue.
- Unmatched flexibility: Unlike rigid chain slings, wire rope slings can conform to the shape of the load, providing better grip and load distribution.
- Enhanced durability: The hard eye design, typically featuring a thimble, offers superior protection against wear and abrasion compared to soft eye slings.
I remember a particularly challenging lift at a construction site where we needed to move irregularly shaped concrete blocks. The hard eye wire rope slings we used hugged the load perfectly, providing stability that a chain sling simply couldn't match.
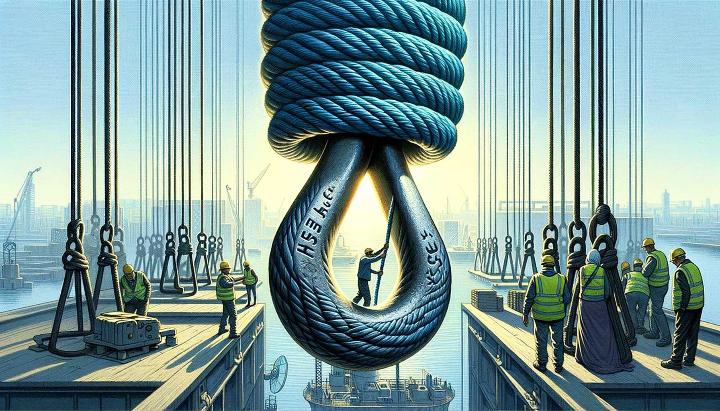
Safety Features and Durability
Safety is paramount in any lifting operation, and hard eye wire rope slings excel in this area. Here's how their design enhances safety and longevity:
- Abrasion resistance: The hard eye design, often incorporating a thimble, protects the rope from wear at its most vulnerable point - the eye.
- Load distribution: The thimble helps distribute the load evenly across the eye, reducing stress on any single point of the rope.
- Kinking prevention: The rigid eye structure prevents kinking, which can significantly weaken the sling.
To ensure the longevity of your hard eye wire rope slings, regular inspection is crucial. Check for signs of wear, broken wires, or deformation, particularly around the eye area. Proper storage away from harsh chemicals and extreme temperatures will also extend their lifespan.
Applications in Harsh Environments
One of the standout features of hard eye wire rope slings is their versatility in challenging conditions. I've used them in various industries, and they've consistently performed well:
- Construction: Ideal for lifting heavy materials like steel beams and concrete blocks in dusty, abrasive environments.
- Marine industry: The corrosion-resistant properties of certain wire rope materials make these slings suitable for saltwater environments.
- Oil and gas: Their ability to withstand extreme temperatures makes them perfect for offshore platforms and refineries.
I once worked on an offshore project where temperatures soared, and corrosive sea spray was a constant challenge. Our hard eye wire rope slings, made with galvanized wire, held up admirably where other slings might have faltered.
When selecting a hard eye wire rope sling for harsh environments, consider the specific challenges of your work site. Factors like temperature extremes, chemical exposure, and abrasive conditions should influence your choice of wire rope material and coating.
At iRopes, we understand the diverse needs of industrial lifting applications. That's why we offer a wide range of hard eye wire rope slings, customized to meet the specific requirements of your project. Whether you're working in the scorching heat of the outback or the corrosive environment of a coastal facility, we have a solution that will ensure safe and efficient lifting operations. Discover how choosing the best winch cable and 16 wire cable can further optimize your lifting solutions.
Have you used hard eye wire rope slings in your operations? What has been your experience with their performance in challenging environments? Share your thoughts and let's discuss how we can optimize your lifting solutions.
Custom Wire Rope Sling Solutions by iRopes
As a rigger with years of experience, I've seen firsthand how crucial it is to have the right wire rope sling for the job. That's where iRopes truly shines. Their custom wire rope sling solutions are a game-changer in the industry, offering tailored solutions that meet the unique needs of various sectors.
Benefits of Custom Wire Rope Slings
When it comes to lifting operations, one size doesn't fit all. Custom wire rope slings offer several advantages that can significantly improve your rigging efficiency and safety:
- Optimized performance: Tailored to your specific load requirements, ensuring maximum efficiency and safety.
- Enhanced safety: Designed to meet or exceed industry standards, reducing the risk of accidents.
- Cost-effective: While initially more expensive, custom slings can offer long-term savings by lasting longer and reducing downtime.
- Versatility: Able to handle unique load shapes and sizes that standard slings might struggle with.
I once worked on a project in the mining industry where we needed to lift oddly shaped equipment. The custom wire rope slings from iRopes made the job not only possible but also remarkably smooth and safe.
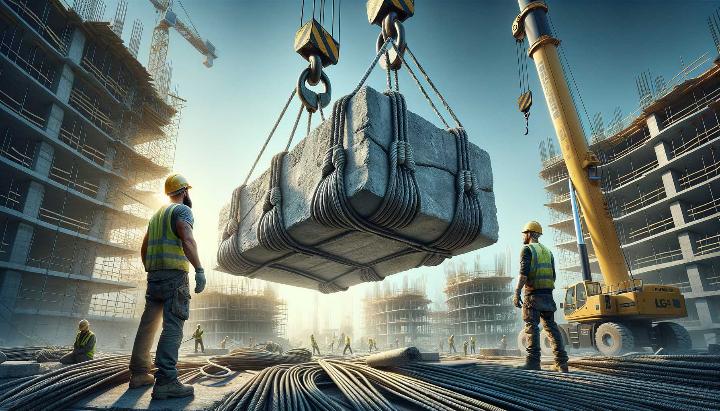
Types of Wire Rope Slings and Applications
iRopes offers a wide range of custom wire rope sling configurations to suit various applications:
- Single-leg slings: Ideal for vertical lifts and simple rigging setups.
- Multi-leg slings: Perfect for balancing uneven loads or lifting large objects.
- Endless slings: Versatile option for choker hitches and basket configurations.
- Braided slings: Offer increased flexibility and strength for specialized applications.
Each type can be customized further with different materials, coatings, and end fittings to meet specific industry requirements. For instance, we once used iRopes' custom stainless steel wire rope slings for a food processing plant, ensuring compliance with strict hygiene standards.
iRopes' Commitment to Quality and Safety
What sets iRopes apart is their unwavering commitment to quality and safety. Every custom wire rope sling undergoes rigorous testing and meets or exceeds OSHA standards. Their team of experts works closely with clients to understand their specific needs and develop solutions that prioritize both efficiency and safety.
Remember, regular inspection is crucial for maintaining the safety and longevity of your wire rope slings. Always follow manufacturer guidelines and OSHA standards for inspection and replacement criteria.
Have you considered how custom wire rope slings could improve your lifting operations? Whether you're in construction, mining, or any industry that requires reliable lifting solutions, iRopes' custom slings could be the answer to your rigging challenges. Reach out to their team of experts today to discuss your specific needs and discover how they can tailor a solution just for you. For more insights into selecting the right rope, check out our essential tips for customizing a rope to meet your specific needs.
Understanding the importance of wire rope sling eye dimensions is crucial for ensuring the safety and efficiency of your lifting operations. iRopes, a leading manufacturer in China, offers bespoke solutions for wire rope sling eyes, considering factors like material, diameter, and load capacity. Their expert craftsmanship ensures each wire rope eye is built to withstand the rigours of heavy-duty lifting, with high-quality components like thimbles and terminations enhancing their durability and performance. Specifically, hard eye wire rope slings provide added resistance to wear and better load distribution than soft eyes, making them ideal for challenging environments. With extensive OEM and ODM services, iRopes tailors each solution to meet unique customer needs, ensuring the highest standards of quality, safety, and customer satisfaction. Enhance your lifting operations with iRopes' customised wire rope slings, designed to meet the rigorous demands of various industries.
Request Custom Wire Rope Slings from iRopes
Fill out the form above to connect with iRopes and discuss your specific needs for wire rope sling eye dimensions. Their team of specialists is ready to provide personalised solutions that will elevate the safety and efficiency of your lifting operations.