Did you know that choosing the wrong sling for your lifting operation could be the difference between a successful project and a costly disaster? In the high-stakes world of industrial rigging, the age-old debate between synthetic rope slings and steel slings continues to challenge even the most seasoned professionals.
At iRopes, we've seen firsthand how this choice can make or break a project. Picture this: a critical offshore operation where every kilogram matters, or a delicate lifting task where flexibility is paramount. In these scenarios, the right sling isn't just a tool—it's your lifeline.
Today, we're diving deep into the synthetic rope sling vs steel sling showdown. We'll explore the unique advantages of synthetic materials like UHMWPE, POLYESTER, NYLON, KEVLAR, TECHNORA, and VECTRAN, and how they stack up against traditional steel in various applications. From marine environments to custom sling solutions, we'll uncover why the choice between synthetic and steel could be the most important decision you make for your next project.
Join us as we unravel the complexities of modern rigging materials and discover which sling reigns supreme in today's demanding industrial landscape. Your next successful lift might just depend on it.
Synthetic Rope Slings: A Versatile and Lightweight Option
When it comes to lifting and rigging applications, synthetic rope slings have revolutionised the industry with their remarkable versatility and lightweight nature. As someone who's spent years working with various sling types, I can confidently say that synthetic slings offer a range of benefits that make them an increasingly popular choice among professionals.
Advantages of Synthetic Slings for Lifting and Rigging
One of the most striking features of synthetic slings is their incredibly light weight. I remember the first time I switched from a steel sling to a synthetic one – the difference was like night and day. The ease of handling and reduced fatigue for workers are game-changers, especially on long projects or in challenging environments.
But it's not just about weight. The flexibility of synthetic slings allows for some truly impressive rigging configurations. I've seen these slings wrap around awkwardly shaped loads with ease, providing a secure grip where steel slings would struggle. This adaptability can be a real lifesaver when you're dealing with unique or delicate items.

Another significant advantage is their resistance to corrosion and chemicals. In marine environments or industrial settings where exposure to harsh substances is common, synthetic slings maintain their integrity far better than their metal counterparts. This durability translates to a longer lifespan and reduced replacement costs – something any project manager can appreciate.
Types of Synthetic Rope Materials for Slings
The world of synthetic slings is diverse, with materials like nylon, polyester, and HMPE (High Molecular Weight Polyethylene) leading the pack. Each material has its unique properties, suited for different applications. Let's break it down:
- Nylon: Excellent for its elasticity and shock-absorbing qualities. I've found it particularly useful in dynamic lifting scenarios.
- Polyester: Known for its dimensional stability and resistance to UV degradation. It's my go-to for outdoor applications where sunlight exposure is a concern.
- HMPE: Offers an impressive strength-to-weight ratio. In situations where maximum strength with minimal weight is crucial, HMPE is hard to beat.
Have you ever wondered how these materials compare in real-world applications? Here's a quick comparison table to give you an idea:
Material | Strength | UV Resistance | Chemical Resistance |
---|---|---|---|
Nylon | High | Moderate | Good |
Polyester | High | Excellent | Excellent |
HMPE | Very High | Good | Excellent |
For those interested in exploring more about these versatile materials and how they can positively impact your operations, consider reading our article on the advantages of synthetic ropes over traditional wire or why synthetic ropes outperform steel lifting cables.
In my experience, the choice between these materials often comes down to the specific requirements of the job at hand. It's not just about picking the strongest option – factors like the lifting environment, load characteristics, and frequency of use all play a role in selecting the ideal synthetic sling.
As we delve deeper into the world of synthetic rope slings, it's clear that their versatility and lightweight nature make them an invaluable tool in modern lifting and rigging operations. Whether you're working in construction, shipping, or any industry that requires safe and efficient material handling, synthetic slings offer a compelling alternative to traditional steel options. Have you considered making the switch to synthetic slings in your operations? The benefits might surprise you.
Steel Slings: The Traditional Choice for Heavy-Duty Lifting
When it comes to heavy-duty lifting applications, steel slings have long been the go-to choice for industry professionals. As someone who's spent decades in the rigging business, I've seen firsthand how these robust workhorses continue to dominate in environments where strength and durability are non-negotiable.
Advantages of Steel Wire Rope Slings
Steel wire rope slings offer a unique combination of strength, versatility, and reliability that's hard to beat. Let me break down why they're still a favourite among riggers:
- Unmatched strength-to-diameter ratio: Steel wire ropes pack an incredible amount of lifting power into a relatively small package, allowing for heavy lifts in tight spaces.
- Heat resistance: Unlike their synthetic counterparts, steel slings can withstand high temperatures without losing integrity – a crucial factor in many industrial settings.
- Abrasion resistance: The tough exterior of steel wire ropes stands up to rough surfaces and sharp edges that would quickly damage softer materials.
- Longevity: With proper care and inspection, a high-quality steel sling can last for years, even in demanding environments.
I remember a project where we were lifting massive steel beams in a foundry. The heat was intense, and there were abrasive surfaces everywhere. Our trusty steel wire rope slings performed flawlessly, handling the job with ease where synthetic slings would have faltered.
Applications and Use Cases for Steel Slings
Steel slings shine in a variety of industries and applications. Here are some common scenarios where you'll find them in action:
- Construction: Lifting heavy machinery and materials
- Shipyards: Handling large vessel components
- Mining: Moving oversized equipment and ore
It's worth noting that while steel slings excel in many areas, they do have limitations. Their weight can be a drawback in some situations, and they can potentially damage delicate surfaces. That's why it's crucial to assess each lifting scenario carefully.
Speaking of safety, it's essential to follow OSHA regulations when using steel wire rope slings. Always ensure proper identification markings are present and conduct regular inspections. Remember, a well-maintained sling is a safe sling. For more insights on choosing the right sling, you might find our guide to choosing the best mooring rope material helpful.
Have you considered the specific requirements of your lifting applications? Whether you're dealing with extreme temperatures, abrasive environments, or simply need the reassurance of time-tested strength, steel slings might be the perfect solution. Don't hesitate to consult with a rigging expert to find the ideal fit for your heavy-duty lifting needs.
Key Factors in Choosing Between Synthetic Rope Slings and Steel Slings
As someone who's spent years in the rigging industry, I can't stress enough how crucial it is to choose the right sling for your lifting needs. The decision between synthetic rope slings and steel slings isn't always straightforward, but understanding the key factors can make all the difference in safety, efficiency, and cost-effectiveness.
Load Characteristics and Sling Performance
When it comes to lifting capacity, steel slings generally have the upper hand. I've seen steel wire rope slings effortlessly handle loads that would make synthetic slings struggle. However, it's not just about raw strength. The flexibility of synthetic slings can be a game-changer for oddly shaped loads.
- Weight capacity: Steel slings typically offer higher load limits, making them ideal for heavy industrial applications.
- Flexibility: Synthetic rope slings excel in wrapping around irregular shapes, providing better load distribution.
- Load shape influence: Consider how the sling will interact with your load. Sharp edges might favour steel, while delicate surfaces could benefit from synthetic options.
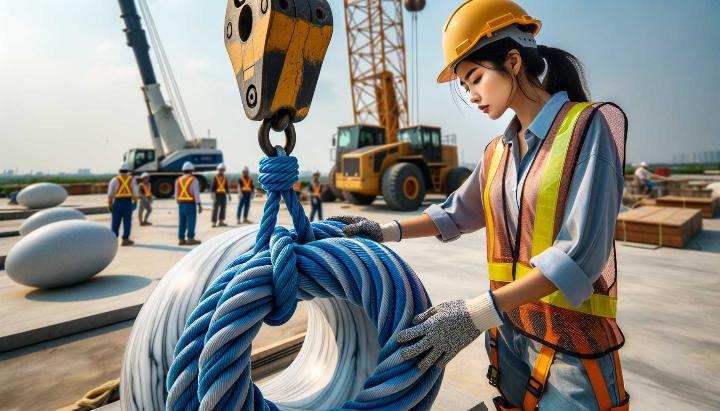
Environmental Considerations for Sling Selection
The environment in which you're operating can significantly impact your sling choice. I once worked on a project in a chemical plant where the corrosive atmosphere ruled out steel slings entirely.
- Temperature limitations: Steel slings can withstand higher temperatures, often up to 400°F (204°C), while most synthetic slings are limited to around 180°F (82°C).
- Chemical resistance: Synthetic slings, especially those made from materials like polyester or nylon, often have superior chemical resistance compared to steel.
- UV exposure: For outdoor applications, consider that some synthetic materials can degrade with prolonged UV exposure, while steel remains largely unaffected.
Remember, it's not just about choosing between synthetic and steel – it's about selecting the right material for your specific environment. Have you considered how your work environment might affect your sling's performance and lifespan?
Safety Factors and Inspection Requirements
Safety should always be your top priority when selecting a sling. Both synthetic and steel slings have specific safety factors and inspection requirements that you must adhere to.
- Safety factors: Synthetic slings typically have a higher safety factor (usually 5:1 to 9:1) compared to wire rope slings (usually 5:1).
- Inspection frequency: Both types require regular inspections, but synthetic slings may need more frequent checks due to potential hidden damage.
- Visible wear indicators: Some synthetic slings come with built-in wear indicators, making it easier to spot when replacement is necessary.
In my experience, a robust inspection routine is crucial regardless of the sling type you choose. It's not just about compliance – it's about ensuring the safety of your team and your loads.
Always consult the manufacturer's guidelines and relevant industry standards (such as ASME B30.9) for specific inspection and usage requirements for your slings.
Choosing between synthetic rope slings and steel slings isn't always black and white. It requires careful consideration of your specific lifting needs, environmental conditions, and safety requirements. By weighing these factors, you'll be well-equipped to make an informed decision that ensures both efficiency and safety in your lifting operations.
Applications and Industries Where Synthetic Marine Rope Excels
As a seasoned maritime engineer, I've witnessed firsthand the remarkable evolution of synthetic marine rope over the years. The versatility and cutting-edge technology behind these ropes have revolutionised numerous industries, particularly in marine environments where traditional materials often fall short.
Marine and Fishing Applications of Synthetic Rope
In the world of sailing and commercial fishing, synthetic marine rope has become an indispensable tool. I remember the first time I stepped onto a modern fishing trawler equipped with high-strength synthetic fiber ropes. The difference in handling and performance compared to traditional steel cables was night and day.
- Mooring lines: Synthetic ropes offer superior elasticity, absorbing shock loads and reducing strain on vessels during docking.
- Tow lines: The lightweight nature of synthetic ropes makes handling easier and safer for crew members during towing operations.
- Anchoring systems: High-strength synthetic fibers provide excellent holding power while being easier to deploy and retrieve.
One particular incident stands out in my mind. During a challenging rescue operation in rough seas, the lightweight and flexible nature of our synthetic tow lines allowed us to maneuver with precision that would have been impossible with heavier steel cables. It's moments like these that truly showcase the safety advantages of synthetic marine rope.
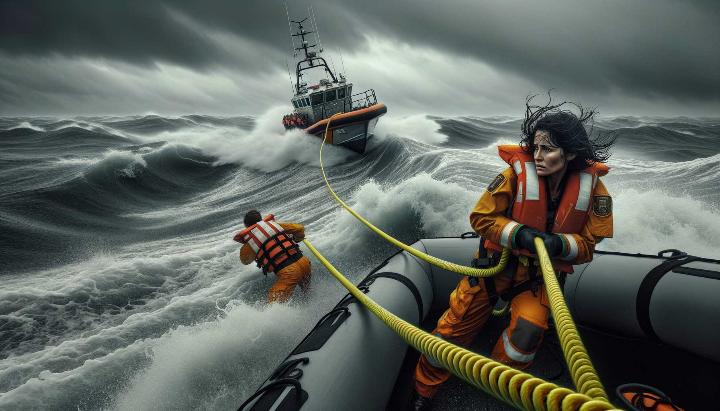
Industrial and Construction Uses for Synthetic Rope
Beyond the maritime world, synthetic rope has found its way into various industrial applications, offering unparalleled performance in challenging environments.
- Offshore oil and gas: HMPE ropes provide exceptional strength-to-weight ratios for deep-sea operations, reducing the overall weight on platforms.
- Mining: Synthetic ropes resist abrasion and chemicals, making them ideal for use in harsh mining conditions.
- Construction: The flexibility and ease of handling of synthetic ropes make them perfect for intricate lifting operations in construction sites.
I once consulted on a high-rise construction project where we replaced traditional steel cables with high-strength synthetic ropes for the tower cranes. The reduction in overall weight allowed for more efficient operations and increased the crane's effective range. It's innovations like these that continue to push the boundaries of what's possible in industrial applications. To learn more, check out our detailed guide on high-quality rope and cords for every industry.
Did you know? Advanced synthetic fibers like UHMWPE can have a strength-to-weight ratio up to 15 times that of steel, while being 7 to 8 times lighter.
The durability and weather resistance of synthetic marine rope also translate to significant cost savings over time. In my experience, properly maintained synthetic ropes can outlast their steel counterparts by a considerable margin, especially in corrosive environments like saltwater.
As we continue to push the boundaries of engineering and explore new frontiers, the role of synthetic marine rope in various industries is only set to grow. Whether you're involved in maritime operations, construction, or any field that requires reliable and high-performance rigging solutions, it's worth considering the advantages that synthetic rope can bring to your projects. Have you had any experience with synthetic marine rope in your work? I'd be curious to hear about your observations and how it compared to traditional materials.
In the world of lifting and rigging, choosing between a synthetic rope sling and a steel sling hinges on several factors, including the specific demands of the application and environmental conditions. Synthetic rope slings, crafted from materials like UHMWPE, polyester, and nylon, offer lightweight flexibility and chemical resistance, making them ideal for projects where versatility and easy handling are paramount. They also excel in sectors such as marine, where their durability against UV and chemicals is valuable. Conversely, steel slings, with their unmatched strength and high load capacities, are suited to heavy-duty tasks in rugged environments, though their weight and rigidity can pose challenges. For those involved in maritime or offshore applications, synthetic marine rope stands out for its lightweight and safety benefits over traditional steel wire ropes. Ultimately, the decision between these options should factor in load capacity, environmental exposure, and cost-effectiveness.
Explore the Ideal Sling Solution for Your Needs
Above, you'll find the inquiry form where you can reach out for tailored advice on choosing between synthetic rope slings and steel slings. Our experts are ready to assist in finding the most suitable and safe option for your specific lifting and rigging needs.