In a world where strength meets innovation, a quiet revolution is reshaping the rope industry. Ultra-high molecular weight polyethylene (UHMWPE) fiber ropes are rapidly dethroning steel wire ropes across multiple sectors, challenging decades of industrial tradition. But what's driving this seismic shift?
Imagine a rope that's seven times lighter than steel yet just as strong. A rope that doesn't corrode, spark, or fatigue easily. Sounds like science fiction? It's not. It's the reality of UHMWPE fiber ropes, and it's transforming industries from offshore oil rigs to fishing trawlers.
As a leading rope manufacturer, iRopes is at the forefront of this transformation, offering customised UHMWPE solutions that are redefining what's possible in lifting, mooring, and rigging operations. In this post, we'll explore how sling wire rope manufacturers are adapting to these innovative materials, and why your business can't afford to be left behind in this rope revolution.
Ready to discover how UHMWPE fiber ropes could revolutionise your operations? Let's dive in.
UHMWPE Fiber Ropes: A Revolutionary Alternative to Sling Wire
In recent years, the rope industry has witnessed a remarkable transformation with the emergence of Ultra-High-Molecular-Weight Polyethylene (UHMWPE) fiber ropes. As a seasoned rope specialist, I've seen firsthand how these innovative materials are challenging the long-standing dominance of steel wire ropes across various sectors.
Advantages of UHMWPE Ropes Over Traditional Wire Ropes
The superiority of UHMWPE fiber ropes over their steel counterparts is nothing short of impressive. Let me break down the key advantages that have caught the attention of industries worldwide:
- Unparalleled strength-to-weight ratio: UHMWPE ropes boast a strength-to-weight ratio up to seven times better than steel wire. This means you can achieve the same lifting capacity with a much lighter rope, revolutionising handling and installation processes.
- Exceptional durability: These ropes exhibit remarkable resistance to abrasion, chemicals, and UV radiation. I've seen UHMWPE ropes maintain their integrity in harsh environments where steel wire ropes would have long since deteriorated.
- Ergonomic handling: The lightweight nature of UHMWPE ropes significantly reduces operator fatigue. I remember a crane operator telling me how switching to UHMWPE ropes made his 12-hour shifts feel much less gruelling.
Did You Know?
UHMWPE ropes can float on water, making them ideal for marine applications!
The rise of UHMWPE fiber ropes as a viable alternative to traditional sling wire is not just a passing trend. It's a technological leap that's reshaping industries from construction to offshore energy. As more businesses discover the benefits of this high-strength synthetic fiber, we're seeing a gradual but definitive shift away from conventional steel wire ropes.
Have you considered how UHMWPE ropes could transform your operations? Whether you're in lifting, mooring, or rigging, these innovative materials offer solutions that combine strength, durability, and ease of use in ways that were previously unimaginable.
In the next section, we'll delve deeper into specific applications where UHMWPE technology is making waves. Stay tuned to learn how various industries are benefiting from this game-changing rope solution.
Advantages of UHMWPE Fiber Ropes Over Steel Wire Rope Slings
As a rope specialist with years of experience in the industry, I've witnessed firsthand the remarkable shift towards Ultra-High Molecular Weight Polyethylene (UHMWPE) fiber ropes. These innovative materials, also known as Dyneema ropes, are rapidly gaining ground on traditional steel wire rope slings across various sectors. Let's dive into the key advantages that make UHMWPE fiber ropes a game-changer in the world of lifting and rigging.
Superior Strength-to-Weight Ratio of UHMWPE Ropes
One of the most striking features of UHMWPE fiber ropes is their incredible strength-to-weight ratio. In my experience, these synthetic ropes are about seven times lighter than steel wire ropes of equivalent strength. This means you can achieve the same lifting capacity with a fraction of the weight, revolutionising handling and installation processes.
I remember a project where we replaced a steel wire rope with a UHMWPE alternative on an offshore platform. The crew was amazed at how much easier it was to manoeuvre and install the lighter rope, significantly reducing installation time and improving safety on the job.
Enhanced Safety and Handling Features of UHMWPE Ropes
- Increased safety due to lower recoil energy: In the unlikely event of rope failure, UHMWPE ropes store less energy, reducing the risk of dangerous whiplash effects compared to steel wire ropes.
- Reduced risk of sparking: Unlike steel wire ropes, UHMWPE fiber ropes don't produce sparks when rubbed or abraded, making them ideal for use in explosive environments like oil rigs or chemical plants.
- Improved flexibility and bend fatigue resistance: The superior flexibility of UHMWPE ropes allows for tighter bending radii and better performance around sheaves and winches, extending the rope's service life.
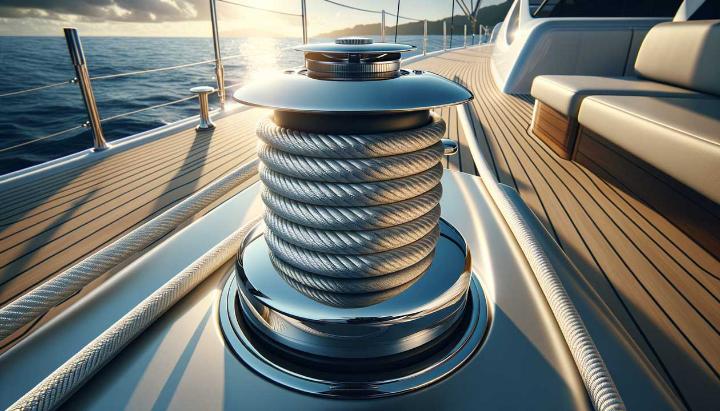
These enhanced safety features have made a significant impact in industries where worker safety is paramount. I've seen offshore oil and gas companies switch to UHMWPE ropes for their lifting operations, drastically reducing the risk of accidents and improving overall workplace safety.
Moreover, the excellent durability and resistance to environmental factors like UV radiation, chemicals, and abrasion make UHMWPE ropes a reliable choice for long-term use in harsh conditions. This translates to reduced maintenance costs and longer service intervals, a win-win for both safety and operational efficiency.
Have you considered how these advantages could benefit your operations? Whether you're in construction, marine industries, or mining, the switch to UHMWPE fiber ropes could be a game-changer for your business. As we continue to explore the benefits of these innovative materials, it's clear that the future of lifting and rigging is leaning towards lighter, safer, and more durable synthetic rope solutions.
Sling wire rope manufacturers adapting to the shift towards UHMWPE fiber ropes
As a veteran in the rope manufacturing industry, I've witnessed firsthand the seismic shift towards Ultra-High Molecular Weight Polyethylene (UHMWPE) fiber ropes. This transition is reshaping the landscape for sling wire rope manufacturers, compelling them to innovate and adapt to remain competitive in an evolving market.
Investing in research and development to create innovative UHMWPE rope solutions
Leading sling wire rope manufacturers are pouring resources into R&D to harness the full potential of UHMWPE technology. I recently toured a state-of-the-art facility where engineers were experimenting with different UHMWPE fiber combinations to enhance rope strength and durability. The buzz of innovation was palpable, with prototypes being tested for various applications, from offshore mooring to heavy-lift operations.
- Advanced fiber processing techniques: Manufacturers are developing proprietary methods to optimize UHMWPE fiber alignment and bonding, resulting in ropes with even greater strength-to-weight ratios.
- Hybrid designs: Some companies are exploring hybrid ropes that combine UHMWPE fibers with other materials to create solutions tailored for specific industry needs.
- Nanotechnology integration: Cutting-edge research is focusing on incorporating nanoparticles into UHMWPE fibers to enhance properties like abrasion resistance and UV stability.
Collaborating with customers to understand their specific requirements
The transition to UHMWPE fiber ropes isn't just about manufacturing; it's about meeting evolving customer needs. Progressive sling wire rope manufacturers are fostering close partnerships with end-users to gain invaluable insights.
During a recent industry conference, I spoke with a product development manager who shared how their company conducts regular site visits and workshops with clients. This collaborative approach ensures that the UHMWPE rope solutions being developed address real-world challenges faced by industries like offshore energy, mining, and heavy construction.
Did you know? Some manufacturers are offering trial programs, allowing customers to test UHMWPE ropes in their operations before making a full transition from steel wire ropes.
Offering customization options to cater to diverse industry needs
The versatility of UHMWPE fiber ropes allows for unprecedented levels of customization. Forward-thinking sling wire rope manufacturers are capitalizing on this by offering bespoke solutions tailored to specific industry requirements.
I recently consulted with a company that developed a custom UHMWPE rope for a challenging underwater construction project. The rope was engineered with a unique coating to enhance its performance in saltwater and resist marine growth, addressing concerns that traditional steel wire ropes couldn't effectively mitigate:
- Specialized coatings: Manufacturers are developing proprietary coatings that enhance UHMWPE rope performance in extreme environments, from arctic conditions to corrosive industrial settings.
- Custom splicing techniques: Advanced splicing methods are being employed to create UHMWPE ropes with specialized end terminations, improving connection points and load distribution.
- Colour coding and markings: To aid in safety and efficiency, manufacturers are offering customized colour schemes and permanent markings on UHMWPE ropes, facilitating easy identification and load limit recognition.
As sling wire rope manufacturers continue to adapt and innovate with UHMWPE fiber technology, the industry is poised for a future where strength, safety, and sustainability converge. The question isn't whether UHMWPE ropes will replace traditional steel wire ropes, but how quickly and comprehensively this transition will occur across various sectors.
Have you considered how UHMWPE fiber ropes could transform your operations? As the industry evolves, staying informed about these innovations could give your business a competitive edge in an increasingly dynamic market.
Applications of UHMWPE Fiber Ropes
As a rope specialist with over two decades of experience, I've witnessed firsthand the revolutionary impact of Ultra-High Molecular Weight Polyethylene (UHMWPE) fiber ropes across various industries. These high-performance synthetic ropes are rapidly replacing traditional steel wire rope slings, offering a combination of strength, safety, and versatility that's hard to match.
Advantages Over Steel Wire Ropes
Before we dive into specific applications, let's recap why UHMWPE fiber ropes are making such waves in the industry:
- Unparalleled strength-to-weight ratio: UHMWPE ropes boast a strength-to-weight ratio 7-9 times better than steel, allowing for the same lifting capacity with significantly reduced weight.
- Enhanced safety features: The lightweight nature of these ropes reduces the risk of injuries during handling and installation, a game-changer for worker safety.
- Exceptional durability: Resistant to UV radiation, chemicals, and abrasion, UHMWPE ropes maintain their integrity in harsh environments where steel wire ropes would quickly deteriorate.
Industries Adopting UHMWPE Ropes
Now, let's explore how various sectors are benefiting from this innovative rope technology:
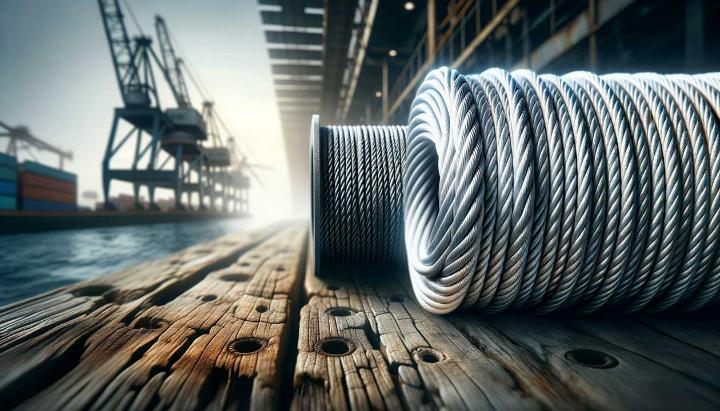
Offshore Oil and Gas Industries
In the challenging environment of offshore platforms, UHMWPE fiber ropes are revolutionising lifting and mooring operations. I recall a project where we replaced steel wire ropes with UHMWPE alternatives on an oil rig in the North Sea. The results were astounding:
- Reduced operational downtime: The lightweight nature of UHMWPE ropes allowed for quicker installation and easier handling, significantly cutting maintenance time.
- Improved safety: The lower recoil energy of UHMWPE ropes reduced the risk of snapback injuries, a common concern with steel wire ropes.
- Extended service life: Despite the harsh marine environment, the UHMWPE ropes showed minimal wear after months of use, outlasting their steel predecessors.
Mining and Construction Sectors
In these industries, where heavy lifting is a daily occurrence, UHMWPE fiber ropes are proving their worth in hoisting and towing applications. A mining company I worked with recently made the switch, and the benefits were clear:
- Increased efficiency: The lighter weight of UHMWPE ropes allowed for longer lengths to be used without overloading winches, expanding operational capabilities.
- Reduced equipment wear: The lower weight reduced stress on pulleys and winch systems, leading to less frequent maintenance and replacements.
- Enhanced safety: The non-sparking nature of UHMWPE ropes made them ideal for use in potentially explosive environments, a crucial safety feature in many mining operations.
Marine and Fishing Industries
From commercial fishing vessels to luxury yachts, UHMWPE fiber ropes are making waves in marine applications. Their use in winches, cranes, and net hauling is transforming operations at sea:
- Improved performance: The buoyancy of UHMWPE ropes makes them ideal for marine use, reducing the load on equipment and making handling easier for crew members.
- Corrosion resistance: Unlike steel wire ropes, UHMWPE ropes don't corrode in saltwater environments, leading to longer service life and reduced maintenance costs.
- Increased catch capacity: In the fishing industry, the lighter weight of UHMWPE ropes allows for larger nets to be deployed, potentially increasing catch sizes without the need for more powerful winch systems.
Did you know? UHMWPE fiber ropes can have a breaking strength up to 15 times that of steel wire rope at the same weight, revolutionising load capacity in various applications.
As we continue to push the boundaries of what's possible in lifting and rigging operations, UHMWPE fiber ropes are at the forefront of innovation. Their unique combination of strength, safety, and versatility is not just replacing steel wire rope slings – it's redefining industry standards across the board.
Have you considered how UHMWPE fiber ropes could transform your operations? Whether you're in offshore energy, construction, or maritime industries, the switch to these high-performance synthetic ropes could be the game-changer your business needs. As we've seen, the benefits extend far beyond just weight savings – they touch every aspect of operational efficiency and safety.
In my years of experience, I've rarely seen a technological advancement with such wide-ranging positive impacts. The future of industrial rope applications is here, and it's lighter, stronger, and safer than ever before.
The shift from traditional steel wire rope sling to innovative UHMWPE fiber ropes is transforming industries with their superior strength-to-weight ratio, enhanced durability, and increased safety features. Sling wire rope manufacturers are adapting by investing heavily in R&D, collaborating with customers, and offering customised UHMWPE solutions. These fibre ropes offer remarkable advantages across various applications, from the offshore oil and gas sector to mining, construction, and marine industries, where their lightweight nature, reduced maintenance costs, and enhanced safety make them the ideal choice. Embracing UHMWPE ropes not only modernises operations but also provides a competitive edge in a demanding market.
Discover the Future of Sling Wire Rope Solutions
Have a question or need a customised rope solution? Fill out the form above to get in touch with our experts and learn how UHMWPE fibre ropes can revolutionise your operations.