Did you know that the weight of a synthetic rope is only 1/7th that of a steel wire rope of the same diameter? This surprising fact is revolutionising the world of rigging and lifting operations. When it comes to carrying or installing off-road winch ropes, synthetic fibres are not only more convenient but also significantly safer. But what about the critical task of maximising efficiency in your lifting operations?
Enter the wire rope sling capacity chart – a powerful tool that's often overlooked but absolutely essential for safe and efficient lifting. Whether you're a seasoned rigger or new to the industry, understanding and utilising these charts can mean the difference between a smooth operation and a costly mistake.
In this post, we'll dive deep into the world of wire rope sling capacity charts, exploring how they can transform your lifting operations. We'll uncover the secrets to interpreting these charts, reveal the key advantages of using them, and share expert tips on maximising efficiency while prioritising safety. By the end, you'll have a new appreciation for these unassuming documents and the crucial role they play in modern rigging practices.
Are you ready to elevate your lifting game and ensure the safety of your team and equipment? Let's explore how the humble wire rope sling capacity chart can become your most valuable asset on the job site.
Understanding Wire Rope Sling Capacity Charts
As someone who's spent years in the rigging industry, I can't stress enough how crucial it is to understand wire rope sling capacity charts. These charts are the unsung heroes of safe lifting operations, providing a wealth of information that can mean the difference between a successful lift and a potentially catastrophic accident.
Components of a Wire Rope Sling Capacity Chart
Let's break down the key components you'll find in a typical wire rope sling capacity chart:
- Sling size and construction: This includes the diameter of the wire rope and how it's constructed (e.g., 6x19, 6x37).
- Rated capacity: The maximum load a sling can safely lift under ideal conditions.
- Hitch types: Vertical, choker, and basket hitches are commonly listed, each with different load capacities.
- Sling angles: Charts often show how the lifting angle affects the sling's capacity.
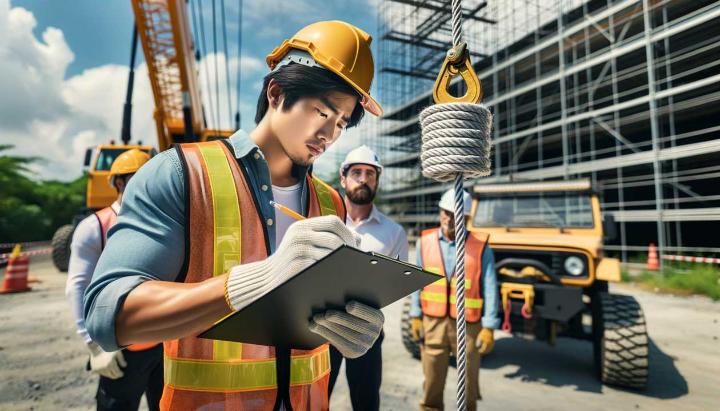
Calculating Safe Working Load for Wire Rope Slings
Determining the Safe Working Load (SWL) is critical for any lift. Here's a simplified process:
- Identify the sling's rated capacity for the specific hitch type you're using.
- Consider the sling angle and apply the appropriate reduction factor.
- Factor in any environmental conditions that might affect the sling's performance.
- Always err on the side of caution and stay well below the calculated SWL.
Remember, these calculations can be complex, and real-world conditions can vary. When in doubt, consult with a rigging specialist or engineer. Your safety and the safety of those around you depend on using these charts correctly.
Pro tip: Always check the manufacturer's guidelines for your specific wire rope sling. They may provide additional information or restrictions not covered in general capacity charts.
Understanding and correctly using wire rope sling capacity charts is an essential skill for anyone involved in lifting operations. It's not just about following rules; it's about creating a culture of safety and efficiency in your workplace. Have you encountered any challenges when using these charts? I'd love to hear about your experiences in the comments below!
Benefits of Using Wire Rope Sling Load Capacity Charts
As someone who's worked in rigging for over a decade, I can't stress enough how valuable wire rope sling load capacity charts are. These unassuming documents are the backbone of safe and efficient lifting operations. Let me walk you through why they're so crucial and how they can revolutionise your work site.
Improved Safety and Efficiency in Lifting Operations
First and foremost, these charts are your best friend when it comes to safety. I remember a close call early in my career when we nearly overloaded a sling because we didn't consult the chart. That experience taught me a valuable lesson.
- Instant access to safe working loads: With a quick glance, you can determine the maximum weight a sling can safely handle, eliminating guesswork and potential accidents.
- Reduced risk of sling failure: By following the chart's guidelines, you dramatically decrease the chances of overloading and damaging your equipment.
- Streamlined decision-making: Charts help you quickly select the right sling for each job, saving time and improving overall efficiency.
Pro tip: Keep laminated copies of your wire rope sling capacity charts in key locations around the work site. This ensures everyone has easy access to this vital information.
Maximizing Load Capacity and Sling Performance
Beyond safety, these charts are powerful tools for optimising your lifting operations. Here's how:
- Optimize sling angles: Charts show how different angles affect load capacity, helping you achieve maximum efficiency in your lifts.
- Understand sling construction: Learn how factors like diameter and wire rope construction influence a sling's strength and flexibility.
- Extend sling lifespan: By using slings within their rated capacities, you'll significantly increase their operational life, saving money in the long run.
Remember, these charts aren't just about compliance – they're about creating a safer, more efficient workplace. Have you found creative ways to use load capacity charts in your operations? I'd love to hear your experiences in the comments below!
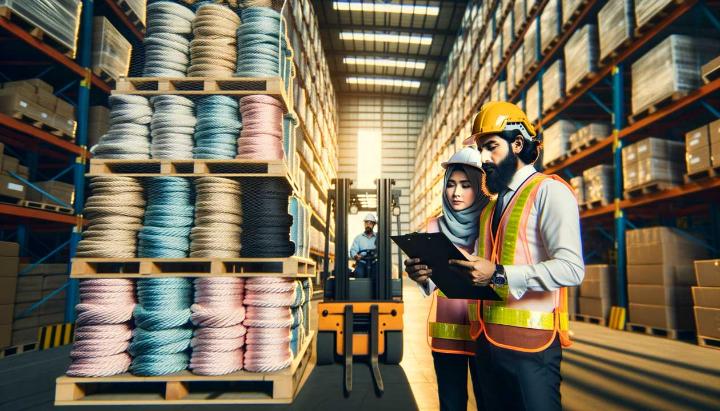
By leveraging the power of wire rope sling load capacity charts, you're not just ticking a box for compliance. You're actively creating a culture of safety, efficiency, and professionalism in your lifting operations. Isn't it time you made these charts an indispensable part of your workflow?
Key Considerations for Wire Rope Sling Capacity Charts
As someone who's spent years in the rigging industry, I can't stress enough how crucial it is to understand the nuances of wire rope sling capacity charts. These charts are more than just numbers on a page; they're your lifeline to safe and efficient lifting operations. Let's dive into the key factors you need to consider when using these invaluable tools.
Understanding Rated Capacity and Load Factors
When I first started in this field, I made the mistake of assuming all wire rope slings were created equal. Boy, was I wrong! The rated capacity of a sling is its bread and butter, but it's not as straightforward as you might think.
- Working Load Limit (WLL): This is the maximum load a sling can safely handle under ideal conditions. Always remember, the WLL is your North Star in any lifting operation.
- Load factors: These are the unsung heroes of safe lifting. They account for variables like sling angle, type of hitch, and environmental conditions.
- Safety factor: This is the buffer between the WLL and the sling's breaking strength. It's your safety net, so never ignore it!
Pro tip: Always err on the side of caution. If you're ever in doubt about a sling's capacity, consult with a rigging expert or choose a higher-rated sling.
Sling Angle Effects on Lifting Capacity
Here's where things get really interesting. The angle at which you use your sling can dramatically affect its lifting capacity. I once witnessed a near-miss incident where a team underestimated the impact of sling angle. Trust me, it's not a mistake you want to make.
- Vertical lifts: These offer the maximum load capacity, as the sling bears the full weight of the load directly.
- Angled lifts: As the angle between the sling legs increases, the load on each leg increases exponentially. It's like magic, but the dangerous kind!
- 60-degree rule: A good rule of thumb is to keep your sling angles at 60 degrees or less from horizontal. Beyond this, the stress on the sling increases rapidly.
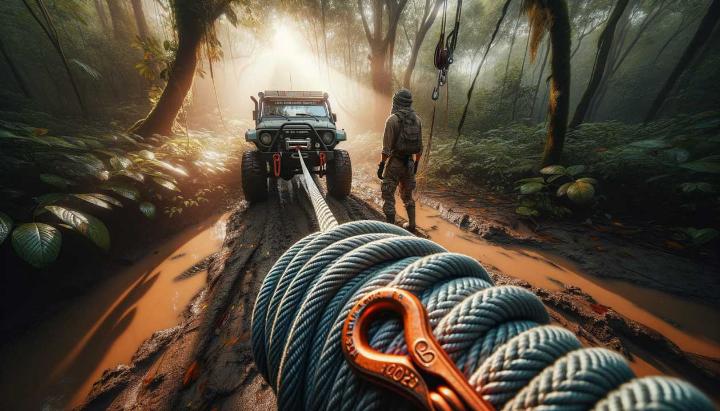
Remember, understanding these key considerations isn't just about compliance or ticking boxes. It's about creating a safer work environment and ensuring that every lift is as efficient and secure as possible. Have you ever encountered a situation where these factors made a crucial difference in your lifting operation? I'd love to hear your stories and insights in the comments below!
Maximizing Efficiency with Wire Rope Sling Capacity Charts
In my years of experience in the rigging industry, I've seen firsthand how proper use of wire rope sling capacity charts can transform lifting operations. These charts are more than just reference tools; they're the key to unlocking peak efficiency and safety in your workplace.
Understanding D/d Ratio and Load Angle Efficiency
Let's dive into two crucial factors that can make or break your lifting operation: the D/d ratio and load angle efficiency.
- D/d ratio: This is the relationship between the diameter of the object being lifted (D) and the diameter of the wire rope (d). A higher D/d ratio means less stress on the rope and greater efficiency. Learn more about Nylon Wire Rope vs Wire Rope Winch and why weight matters.
- Load angle efficiency: As the angle between the sling legs increases, the load on each leg grows exponentially. Keeping this angle at 60° or less is a good rule of thumb for maintaining efficiency and safety.
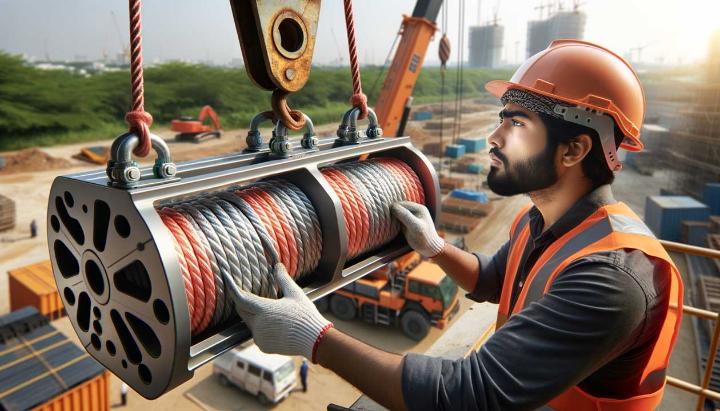
I once witnessed a near-miss incident where a team overlooked these factors. The load swung dangerously close to workers because the sling angle was too wide. It's a mistake you don't want to make twice.
Calculating Wire Rope Sling Capacity for Safe Lifting
Now, let's talk about how to put these charts to work. Here's a step-by-step guide to calculating the Safe Working Load (SWL) for your wire rope sling:
- Identify the Working Load Limit (WLL) of your sling from the manufacturer's specifications.
- Apply the SWL formula: SWL = 2.1 x WLL of single sling
- Adjust for sling angle using the efficiency factor from your chart.
- Consider environmental factors like temperature or chemical exposure that might affect capacity.
Remember: Always round down your final SWL calculation. It's better to be conservative when safety is on the line. For more information on safety and versatile ropes, take a look at Synthetic vs Nylon Coated Wire Rope.
By mastering these calculations and understanding the nuances of wire rope sling capacity charts, you're not just improving efficiency – you're creating a safer, more productive work environment. Have you found innovative ways to use these charts in your operations? I'd love to hear your experiences in the comments below!
Efficient and safe lifting operations are critical in any rigging environment, and our wire rope sling capacity chart is an indispensable tool to help ensure just that. By understanding the key components and benefits of wire rope sling capacity charts, you can optimise your lifting tasks, select the appropriate slings, and prevent potential accidents. These charts assist in maintaining compliance with industry standards and regulations while enhancing overall workplace safety and productivity. Remember, a sling's load capacity is influenced by many factors, including the sling material, construction, and environmental conditions. Fibre ropes, for instance, offer added convenience and safety, as their weight is only 1/7th that of wire ropes of the same diameter, making them easier to carry and install.