Have you ever found yourself in a tug-of-war between tradition and innovation when it comes to winch ropes? If so, you're not alone. The debate between wire rope winches and nylon wire ropes has been heating up in recent years, leaving many industry professionals wondering: which is truly better?
As a leading rope manufacturer, we at iRopes have seen firsthand how this choice can make or break operations across various sectors, from off-road adventures to industrial applications. While wire rope winches have long been the go-to for their strength and durability, nylon wire ropes are rapidly gaining ground, offering a compelling blend of flexibility, lightweight design, and surprising resilience.
In this post, we'll dive deep into the world of winch ropes, comparing the stalwart wire rope winch against its innovative counterpart, the nylon wire rope. We'll explore their unique characteristics, weigh their pros and cons, and ultimately reveal why nylon wire ropes are becoming the preferred choice for many forward-thinking professionals. Whether you're a seasoned winch operator or a curious newcomer, this comparison will equip you with the knowledge to make an informed decision for your specific needs.
So, buckle up as we unravel the strengths of these two titans of the winching world, and discover why the future might just be leaning towards the lightweight champion - the nylon wire rope.
Understanding Wire Rope Winches: Essential Components and Functions
As an avid off-road enthusiast, I've come to appreciate the power and versatility of wire rope winches. These mechanical marvels are the unsung heroes of many industries, capable of lifting or pulling heavy loads with ease. But what exactly makes a wire rope winch tick?
At its core, a wire rope winch consists of four main components: a drum, motor, gear system, and the wire rope itself. The drum is where the magic happens - it's the cylindrical heart of the winch that spools and unspools the wire rope. The motor provides the muscle, while the gear system acts as the brains, translating the motor's power into controlled, powerful movement.
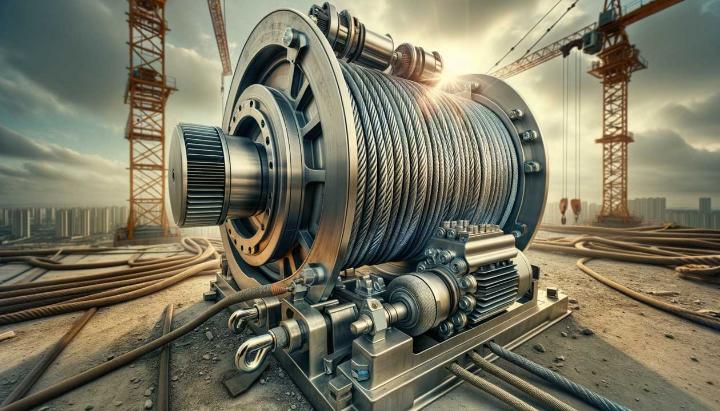
But what truly sets wire rope winches apart is their incredible mechanical advantage. By using a series of gears and pulleys, these winches can multiply the force applied, allowing them to move loads far heavier than you might expect. It's like having a team of oxen at your fingertips!
Types of Wire Rope Winches and Their Applications
Wire rope winches come in various flavours, each suited to different tasks. Let's break them down:
- Electric winches are the workhorses of many industries, offering reliable power and easy operation. You'll often spot these in warehouses or on construction sites.
- Hydraulic winches pack a serious punch, making them ideal for heavy-duty applications like oil rigs or large marine vessels.
- Manual winches might seem old-school, but they're incredibly reliable and perfect for situations where power sources are limited.
Each type has its strengths and limitations. For instance, while electric winches are versatile, they might struggle in wet environments where hydraulic winches shine. It's all about choosing the right tool for the job.
How to Operate a Wire Rope Winch Safely and Effectively
Safety should always be your top priority when operating a wire rope winch. Before you even think about powering up, conduct a thorough pre-operation check. Inspect the wire rope for any signs of wear or damage, ensure all components are properly lubricated, and check that the winch is securely mounted.
When it's time to operate, remember these key steps:
- Clear the area of bystanders
- Wear appropriate personal protective equipment
- Engage the clutch and spool out enough rope for your task
- Attach the load securely, using appropriate rigging techniques
- Double-check all connections before applying power
One common mistake I've seen (and, admittedly, made myself in my early days) is overloading the winch. Always respect the rated capacity - it's there for a reason!
Regular maintenance is crucial for longevity and reliable performance. Keep your winch clean, lubricated, and stored properly when not in use. And don't forget about that all-important wire rope inspection - it could save you from a nasty surprise down the line.
Remember, a well-maintained winch is a safe winch. Never skip your routine inspections and always replace worn components promptly.
Understanding wire rope winches is more than just knowing how they work - it's about respecting their power and using them wisely. Whether you're recovering a bogged 4x4 or lifting heavy equipment on a construction site, these versatile tools are ready to lend a helping hand. Just remember to treat them with care, and they'll never let you down when you need them most.
Exploring Nylon Wire Rope: Benefits and Applications
As someone who's spent years working with various types of ropes, I've developed a soft spot for nylon wire rope. It's a fascinating blend of strength and flexibility that's revolutionised many industries. But what exactly is nylon wire rope, and why has it become such a game-changer?
At its core, nylon wire rope is a clever combination of traditional steel wire rope with a nylon coating or braiding. This marriage of materials creates a rope that offers the best of both worlds - the strength of steel and the versatility of nylon.
Advantages of Nylon-Coated Steel Wire Rope
The benefits of nylon wire rope are numerous, but let me share a few that have really stood out in my experience:
- Rust and corrosion resistance - The nylon coating acts like a shield, protecting the steel core from the elements. I've seen nylon ropes outlast their non-coated counterparts in harsh marine environments.
- Enhanced shock absorption - The nylon outer layer provides a cushioning effect, reducing the impact of sudden loads. This can be a real lifesaver when you're dealing with heavy lifting operations.
- Improved handling - The smooth nylon surface is much kinder on the hands than bare steel wire. Trust me, your palms will thank you after a long day's work!
- Reduced noise - The nylon coating significantly dampens the noise typically associated with steel wire ropes. It's a small detail, but it can make a big difference in noise-sensitive environments.
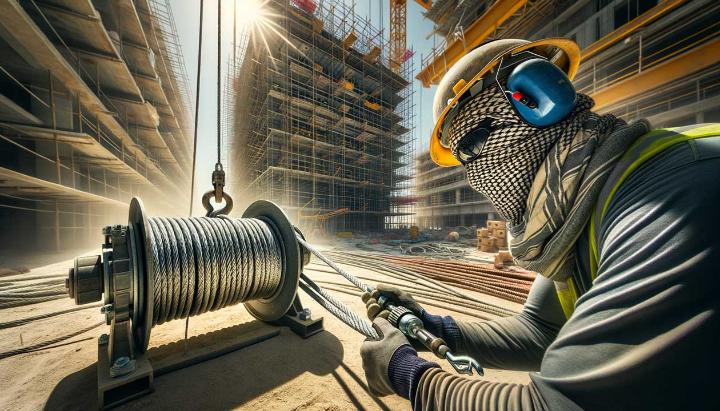
Common Uses for Nylon Wire Rope
The versatility of nylon wire rope makes it a go-to choice for a wide range of applications. Here are some areas where I've seen it truly shine:
- Marine environments - From mooring lines to fishing nets, nylon wire rope's corrosion resistance makes it ideal for use at sea.
- Construction and rigging - Its shock-absorbing properties and durability make it perfect for heavy lifting and load securing.
- Outdoor recreation - Ever been zip-lining? Chances are you were trusting your life to a nylon wire rope!
- Decorative applications - The smooth, colourful finish of nylon rope has made it popular in architectural and interior design projects.
But it's not all smooth sailing with nylon wire rope. While it's incredibly versatile, it does have its limitations. The nylon coating, while protective, can reduce the overall strength of the rope compared to a bare steel wire of the same diameter. It's also more susceptible to UV degradation over time, something to keep in mind for long-term outdoor applications.
When choosing between nylon wire rope and traditional steel wire rope, it's crucial to consider your specific needs. Are you prioritising corrosion resistance and handling comfort? Nylon might be your best bet. Need maximum strength with no compromises? Traditional steel wire could be the way to go.
Remember, proper maintenance is key to maximising the lifespan of any rope. Regular inspections and cleaning can significantly extend the service life of your nylon wire rope.
In my experience, nylon wire rope has proven to be a fantastic innovation, offering a balance of strength, durability, and user-friendliness that's hard to beat. Whether you're rigging a sailboat or securing a load on a construction site, it's definitely worth considering for your next project. Have you had any experiences with nylon wire rope? I'd love to hear about them in the comments below!
Comparing Wire Rope and Synthetic Rope for Winching Applications
When it comes to winching, choosing the right rope can make all the difference between a smooth operation and a potential disaster. As someone who's spent countless hours in the field, I've seen firsthand how crucial this decision can be. Let's dive into the world of wire rope and synthetic rope, and explore which might be the best fit for your winching needs.
Advantages of Synthetic Winch Rope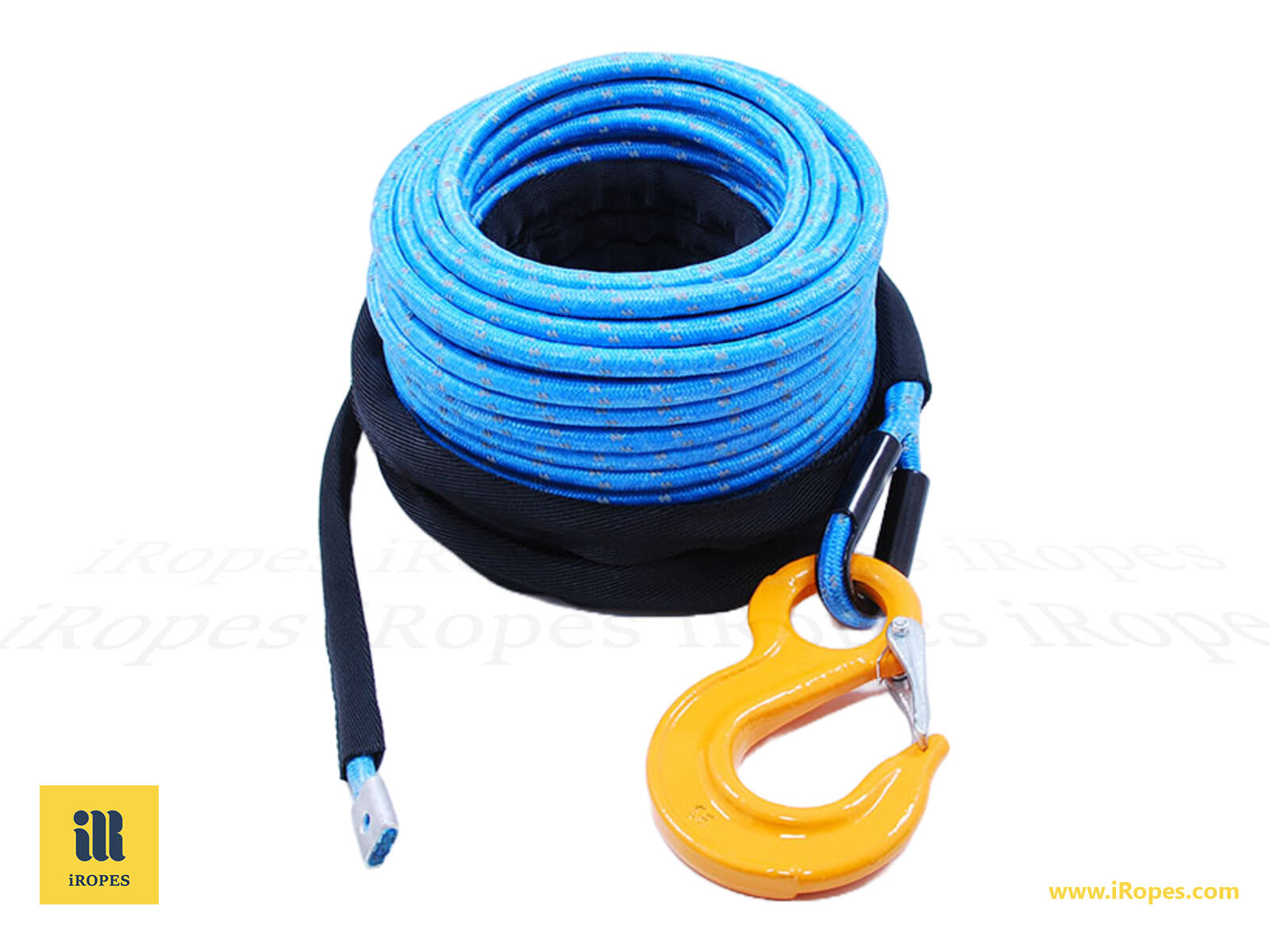
• Gusset SS black Tube thimble+G80 single ringHook+3M length black Sleeve, end
with Mounting lug+3M black Sleeve
MATERIAL: UHMWPE-UHMWPE
CONSTRUCT: 12/24strands
Synthetic winch rope has been gaining popularity in recent years, and for good reason. Here's why it's become a favourite among many winch operators:
- Lightweight champion - Synthetic rope is incredibly light, making it a breeze to handle. I remember the first time I switched from wire to synthetic - it felt like I'd taken a weight off my shoulders, literally!
- Impressive strength-to-weight ratio - Don't let its light weight fool you. Synthetic rope packs a punch, often boasting a strength that's 70% higher than steel wire of the same diameter.
- Safety first - If a synthetic rope breaks, it doesn't store energy like steel wire. This means it's less likely to whip back dangerously, a feature that's saved many operators from nasty injuries. Learn more about synthetic winch ropes here.
- Flexibility is key - The pliable nature of synthetic rope makes it easier to work with, especially in tight spaces or when wrapping around objects.
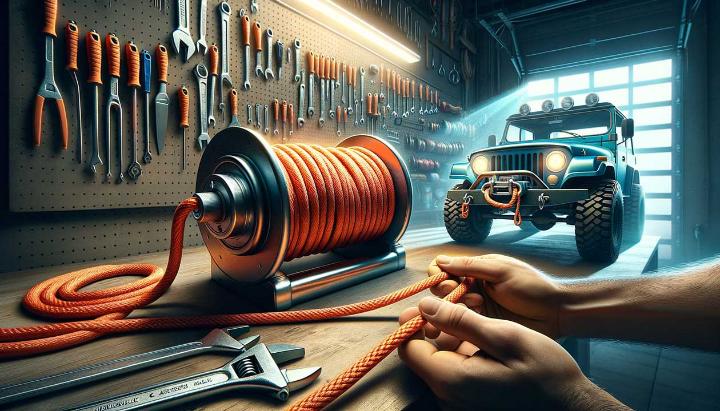
Benefits of Steel Wire Rope for Winching
Despite the rise of synthetic options, steel wire rope still holds its ground in many applications. Here's why it remains a solid choice:
- Durability is its middle name - Steel wire rope can take a beating. I've seen it withstand abrasive conditions that would shred synthetic rope in no time.
- Heat resistant - In high-temperature environments, steel wire rope maintains its integrity where synthetic might weaken or melt. Discover more about steel wire rope applications here.
- Cost-effective for frequent use - While the initial cost might be higher, steel wire rope often proves more economical in the long run for heavy, frequent use.
- UV resistant - Unlike synthetic ropes that can degrade with prolonged sun exposure, steel wire rope stands strong against UV rays.
Pro tip: Always match your rope choice to your specific winching scenario. What works best for off-road recovery might not be ideal for marine applications or industrial use.
Choosing between synthetic and steel wire rope isn't always straightforward. It depends on factors like your working environment, frequency of use, and specific application requirements. Have you had experience with both types? Which do you prefer for your winching needs? Share your thoughts in the comments below - I'd love to hear about your experiences!
Remember, whichever rope you choose, regular inspection and proper maintenance are key to ensuring safe and efficient winching operations. Read more about maintaining your ropes here. Happy winching, folks!
Importance of Regular Wire Rope Inspection
As someone who's spent years in the rigging industry, I can't stress enough how crucial regular wire rope inspections are. It's not just about ticking boxes on a safety checklist; it's about protecting lives and ensuring the longevity of your equipment.
Key Guidelines for Wire Rope Inspection
Let me walk you through the inspection process I've honed over the years:
- Visual check - Start with a thorough visual inspection of the entire rope length. Look for obvious signs of wear, corrosion, or damage.
- Feel the rope - Run your hands along the rope (with proper PPE, of course). You'd be surprised how much you can detect through touch alone.
- Measure the diameter - Use callipers to check for any reduction in rope diameter, which could indicate internal wear.
- Check for broken wires - Count any visible broken wires. OSHA has specific guidelines on the maximum number allowed.
- Inspect end attachments - Don't forget to examine the rope terminations and connections for any signs of weakness or damage. Learn more about securing your rope ends here.
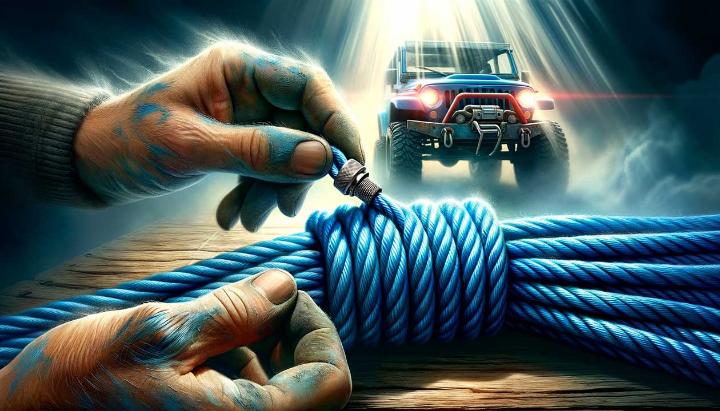
Remember, these inspections aren't just a one-off event. OSHA recommends daily visual checks and more thorough inspections at least annually. In my experience, it's better to err on the side of caution and inspect more frequently, especially in harsh environments or high-use scenarios.
OSHA Requirements for Wire Rope Safety
OSHA doesn't mess around when it comes to wire rope safety, and for good reason. Here's a quick rundown of their key requirements:
- Daily visual inspections are mandatory for all wire ropes in use.
- Thorough examinations must be conducted at least annually, or more frequently based on usage and conditions.
- Detailed records of all inspections must be maintained, including dates, findings, and any actions taken.
- Immediate removal from service is required if certain defects are found, such as kinking, crushing, or excessive broken wires.
I've seen firsthand the consequences of neglecting these inspections. Trust me, it's not pretty. A few years back, I witnessed a catastrophic failure on a construction site due to an overlooked wire rope defect. Thankfully, no one was hurt, but it was a stark reminder of why we take these inspections so seriously.
Never compromise on wire rope inspections. The few minutes you spend could save lives and prevent costly equipment failures.
Regular wire rope inspections aren't just about compliance; they're about creating a culture of safety and reliability in your operations. By following these guidelines and staying vigilant, you're not only protecting your team but also ensuring the efficiency and longevity of your equipment. Remember, when it comes to wire rope safety, there's no such thing as being too careful.
Have you encountered any challenges with wire rope inspections in your work? I'd love to hear about your experiences and any tips you might have for our readers. Drop a comment below and let's keep the conversation going!
Choosing between a wire rope winch and a nylon wire rope boils down to application-specific needs. A wire rope winch, known for its strength and durability, is ideal for heavy-duty lifting but can be weighty and prone to corrosion. Alternatively, nylon wire rope offers a lightweight and flexible design, making it perfect for marine and off-road uses, though it's typically less robust than its steel counterpart. Routine wire rope inspection is critical to maintain safety and equipment functionality. Consider your priorities carefully to select the best winch rope for your needs.
Request for Customised Rope Solutions
For further insights into wire rope winch options or customisation details, please fill in the inquiry form above. Our specialists at iRopes are ready to assist you with tailored solutions that meet your specific requirements.