Imagine a world where lifting heavy loads is as simple as tying your shoelaces. While we're not quite there yet, the right steel cable lifting sling can make all the difference between a smooth operation and a potential disaster. But with countless options available, how do you choose the perfect sling for your unique needs?
Welcome to our essential guide on choosing steel cable lifting slings. Whether you're a seasoned rigger or new to the world of heavy lifting, this comprehensive resource will equip you with the knowledge to make informed decisions that prioritise safety, efficiency, and compliance.
At iRopes, we understand that one size doesn't fit all when it comes to lifting solutions. That's why we offer customised synthetic lifting slings tailored to your specific requirements, load capacities, and lifting scenarios. From off-road adventures to industrial applications, our expert team is ready to craft the perfect sling for your unique challenges.
In this guide, we'll explore the intricacies of steel cable slings, uncover crucial selection factors, and reveal maintenance secrets that can extend the life of your equipment. So, buckle up and prepare to elevate your lifting game – your safety and success depend on it.
Understanding Steel Cable Slings: Types and Applications
When it comes to heavy lifting operations, steel cable slings are the unsung heroes of the industry. These versatile tools are essential for safely and efficiently moving loads in various sectors. Let's dive into the world of wire rope slings and explore their composition, advantages, and applications.
Anatomy of Wire Rope Slings
Steel cable slings, also known as wire rope slings, are marvels of engineering. Picture a bundle of steel wires twisted together like a metallic braid, each strand working in harmony to provide incredible strength. The core of the sling, typically made of fiber or steel, acts as the backbone, while the outer strands provide flexibility and durability.
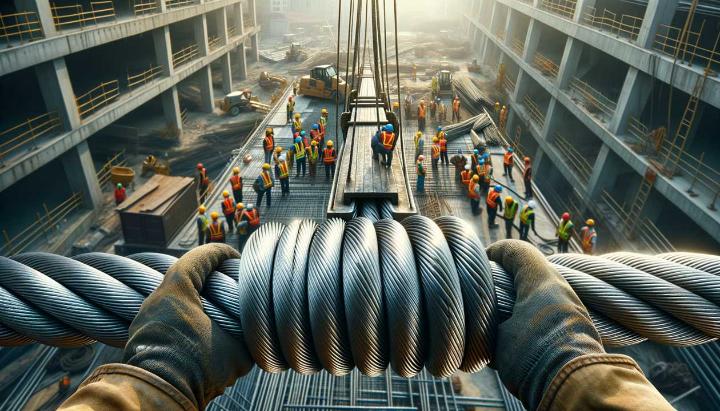
The construction of wire rope slings can vary, with different configurations offering unique properties:
- Eye-and-eye slings feature loops at both ends, perfect for versatile rigging setups.
- Endless slings form a continuous loop, ideal for choker hitches and basket configurations.
- Multi-leg slings have multiple branches, allowing for balanced load distribution in complex lifts.
Safety and Inspection Guidelines for Steel Cable Slings
Safety is paramount when working with steel cable slings. Regular inspections are crucial to identify wear, damage, or deformation. Before each use, run your hands along the sling, feeling for any broken wires or kinks. Pay special attention to the eyes and end fittings – these are critical stress points.
Remember, a well-maintained sling is a safe sling. Proper storage in a cool, dry place away from chemicals and extreme temperatures can significantly extend the life of your wire rope slings.
Calculating Lifting Capacity of Wire Rope Slings
Understanding the lifting capacity of your steel cable slings is crucial for safe operations. The rated capacity is based on the minimum breaking strength of the wire rope, with a safety factor applied. Always check the manufacturer's specifications and never exceed the working load limit (WLL).
Did you know? The angle at which a sling is used can dramatically affect its lifting capacity. A 60-degree angle can reduce the capacity by up to 13%!
Steel cable slings shine in various industries, from construction and shipping to manufacturing and mining. Their versatility, strength, and durability make them indispensable for lifting heavy machinery, structural steel, and even delicate equipment when used with proper padding.
As we wrap up this section, remember that choosing the right steel cable sling is just the beginning. Proper use, regular maintenance, and adherence to safety guidelines are all crucial for successful lifting operations. In the next section, we'll explore the factors to consider when selecting the perfect steel cable sling for your specific needs.
Essential Factors for Selecting Steel Cable Lifting Slings
Choosing the right steel cable lifting sling isn't just about picking the strongest option available. It's a delicate balance of safety, efficiency, and suitability for your specific lifting needs. Let's dive into the crucial factors you need to consider to ensure your lifting operations are both safe and effective.
Load Capacity and Weight Considerations
When I first started working with steel cable slings, I learned the hard way that underestimating load capacity can lead to disastrous consequences. The working load limit (WLL) is your golden rule here. It's typically one-fifth of the sling's minimum breaking strength, giving you a safety factor of 5:1.
But here's the kicker: it's not just about the total weight. The distribution of that weight matters too. I once saw a perfectly good sling fail because the load's center of gravity was off-center. Always consider:
- Total weight of the load: Including any additional attachments or packaging.
- Weight distribution: Uneven loads can cause unexpected stress on your sling.
- Dynamic forces: Sudden movements or stops can multiply the effective load weight.
Remember, the angle at which you use your sling can significantly reduce its lifting capacity. A 60-degree angle, for instance, can decrease capacity by up to 13%!
Sling Material and Construction
Steel cable slings are incredibly versatile, but they're not always the best choice for every situation. Let's compare them to other common materials:
- Chain slings: More durable and resistant to abrasion, but heavier and less flexible.
- Synthetic slings: Lighter and more flexible, but more susceptible to environmental damage.
- Steel cable slings: A great middle ground, offering strength, flexibility, and resistance to environmental factors.
When it comes to wire rope construction, you've got options. The number of strands and wires per strand can affect the sling's strength, flexibility, and resistance to abrasion. For instance, a 6x19 construction (6 strands, 19 wires each) offers a good balance of strength and flexibility, making it a popular choice for general lifting applications.
Choosing the right configuration is crucial too. Vertical, choker, and basket hitches each have their place:
- Vertical hitches: Simplest to use but offer the lowest load capacity.
- Choker hitches: Great for securing cylindrical loads but reduce capacity by about 25%.
- Basket hitches: Provide the highest load capacity but require careful load balancing.
Environment and Working Conditions
Your working environment can make or break your steel cable sling. I once saw a perfectly good sling corrode in a matter of weeks because it wasn't suited for a marine environment. Consider these factors:
- Temperature extremes: High heat can weaken the sling, while extreme cold can make it brittle.
- Corrosive substances: Chemicals and salt water can quickly degrade your sling.
- Abrasive conditions: Rough surfaces can wear down your sling faster than you might expect.
Don't forget about storage conditions either. Proper storage in a cool, dry place can significantly extend your sling's lifespan.
Statutory Requirements and Industry Standards
Lastly, but certainly not least, make sure your steel cable sling meets all relevant safety standards and regulations. In Australia, we follow the AS 3775 standard for steel wire rope slings. This covers everything from manufacturing requirements to periodic inspection guidelines.
Remember, compliance isn't just about avoiding fines - it's about ensuring the safety of your team and your operations. Always choose slings that come with proper certification and documentation.
Safety First, Always
No lift is worth risking lives. Choose your slings wisely and use them correctly.
Selecting the right steel cable lifting sling might seem daunting, but with these factors in mind, you're well on your way to safer, more efficient lifting operations. Remember, when in doubt, always consult with a lifting gear specialist. They can provide invaluable advice tailored to your specific needs and working conditions.
Customization Options for Cable Slings
When it comes to lifting operations, one size definitely doesn't fit all. That's where the beauty of cable sling customization comes into play. As someone who's spent years in the rigging industry, I've seen firsthand how tailored solutions can make all the difference in safety and efficiency.
Types of Custom Wire Rope Slings
Let's dive into the world of custom wire rope slings. Picture this: you're at a job site, faced with a uniquely shaped load that seems impossible to lift safely. That's when you'll appreciate the versatility of customized slings.
- Vertical slings: The simplest configuration, perfect for straightforward lifts. I remember using these to hoist massive steel beams during a skyscraper construction project.
- Basket slings: Ideal for cradling loads, these distribute weight evenly. They're my go-to for lifting oddly shaped machinery.
- Choker slings: These tighten around the load as tension increases. I've used them countless times for lifting pipes and other cylindrical objects.
Each configuration affects the sling's performance and load capacity. For instance, a basket hitch typically offers the highest load capacity, while a choker hitch reduces it by about 25%.

Selecting the Right Cable Sling Configuration
Choosing the right configuration isn't just about the load's shape. You've got to consider the entire lifting scenario. Here's what I always keep in mind:
- Load weight and shape: Is it evenly distributed? Are there any protruding parts?
- Lifting environment: Are we dealing with extreme temperatures or corrosive substances?
- Sling material: Sometimes, a steel core is necessary for added strength.
- End fittings: The right hooks or shackles can make rigging a breeze.
Remember, OSHA standards require proper identification markings on all slings. It's not just bureaucratic red tape - these markings are crucial for ensuring you're using the right sling for the job.
Did you know? The minimum design factor for wire rope slings is 5. This means the sling's breaking strength is five times its rated capacity, providing a crucial safety margin.
Custom sling fabrication goes beyond just choosing a configuration. We can tailor the length, diameter, and even add protective sleeves to prevent damage. I once worked on a project where we needed a sling with a specialized coating to resist chemical corrosion. The ability to customize saved us from potential disaster.
In my experience, working with a reputable manufacturer is key. They can guide you through the customization process, ensuring you get a sling that not only meets OSHA standards but is perfectly suited to your unique lifting challenges.
Remember, the right custom cable sling isn't just about getting the job done - it's about getting it done safely and efficiently. So, next time you're faced with a tricky lift, don't settle for a one-size-fits-all solution. Explore your customization options and find the perfect fit for your needs.
Proper Use and Maintenance of Cable Lifting Slings
As a rigger with over two decades of experience, I can't stress enough how crucial proper use and maintenance of cable lifting slings are. These workhorses of the lifting world demand respect and care to ensure safe, efficient operations. Let's dive into the essential practices that'll keep your slings in top shape and your worksite safe.
Safe Usage Guidelines for Wire Rope Slings
Using wire rope slings correctly is an art as much as it is a science. I've seen far too many close calls due to improper usage. Here are some golden rules I always follow:
- Never exceed the working load limit (WLL): This isn't just a suggestion - it's a lifesaver. The WLL is typically one-fifth of the sling's breaking strength.
- Mind your angles: The wider the angle between sling legs, the lower the lifting capacity. Keep it under 60 degrees if possible.
- Protect against sharp edges: Use corner protectors or softeners to prevent damage to both the load and the sling.
- Avoid shock loading: Sudden jerks can multiply the effective load weight. Always lift smoothly and steadily.
Remember, OSHA regulations are there for a reason. Never be tempted to take shortcuts like using knots to shorten a sling - it's not just against regulations, it's downright dangerous.
Did you know? OSHA prohibits the use of knots or makeshift devices to shorten slings. Always use manufacturer-approved methods for adjusting sling length.
Essential Maintenance and Storage Practices
Proper maintenance can significantly extend the life of your cable lifting slings. Here's what I've learned over the years:
- Clean regularly: After each use, wipe down your slings to remove dirt, grime, and any corrosive substances.
- Lubricate wisely: In harsh environments, a light coating of lubricant can prevent corrosion. But be careful - too much can attract dirt.
- Store properly: Hang your slings in a cool, dry place away from direct sunlight. Avoid damp floors or areas with chemical fumes.
- Protect from damage: Use padding or racks to prevent kinks and abrasions during storage.
I once visited a worksite where slings were left out in the rain and sun. Within months, they were showing signs of UV damage and rust. Don't make the same mistake - treat your slings like the valuable tools they are.
Inspection Procedures for Cable Lifting Slings
Regular inspections are your first line of defense against sling failure. Here's my tried-and-true inspection process:
- Check for visible damage: Look for kinks, bird-caging, or broken wires.
- Feel for internal damage: Run your hands along the sling (carefully!) to detect any hidden issues.
- Examine end fittings: Ensure they're not bent, cracked, or excessively worn.
- Verify markings: Make sure the sling's ID tag is legible and matches your records.
- Test flexibility: The sling should bend easily without feeling stiff or "crunchy".
How often should you inspect? OSHA requires a thorough examination at least annually, but in my experience, a quick check before each use and a more detailed inspection monthly is a smart practice.
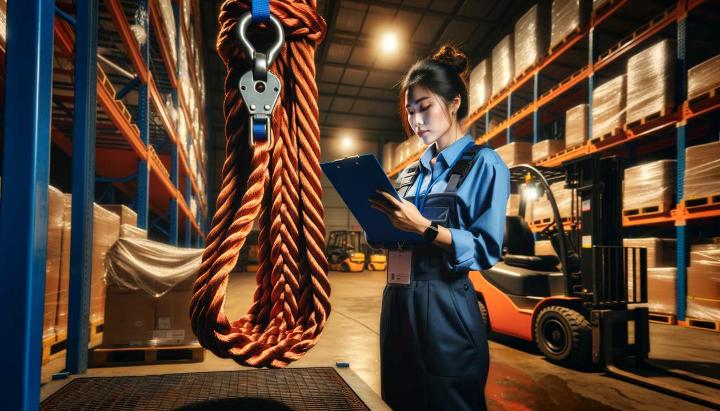
Remember, when in doubt, take it out. A sling that shows signs of significant wear or damage should be removed from service immediately. It's better to replace a sling than risk a catastrophic failure.
By following these guidelines for proper use, maintenance, and inspection of your cable lifting slings, you're not just prolonging their life - you're creating a safer work environment for everyone on site. Trust me, in this industry, safety is always worth the investment.
For more insights into specialized lifting equipment, check out our article on Synthetic Cable Characteristics Explained and learn how to incorporate innovative synthetic solutions into your lifting operations.
Get Customised Steel Cable Lifting Slings Now
Choosing the right cable lifting slings is crucial for safe and efficient operations. Steel cable slings offer superior strength and versatility, making them ideal for various industries. Key factors to consider include load capacity, sling configuration, and environmental conditions. iRopes provides custom design solutions to fit unique lifting scenarios, ensuring your slings meet all statutory and industry standards. For a tailored solution that matches your exact needs, consult with our rope specialists. Fill in the form above, and let us help you find the perfect cable slings for your application.