Did you know that a synthetic cable as thin as your finger can lift a fully loaded semi-truck? It's not science fiction—it's the remarkable reality of modern synthetic cable technology. As a leading manufacturer of high-performance ropes, we at iRopes have witnessed firsthand the revolution that synthetic cables are bringing to industries worldwide.
From the depths of the ocean to the heights of skyscrapers, synthetic cables are reshaping how we approach challenging tasks. They're not just replacing traditional steel cables; they're opening up new possibilities that were once thought impossible. But what makes these innovative ropes so special?
In this post, we'll unravel the mysteries behind synthetic cable characteristics. We'll explore their unique composition, impressive strength-to-weight ratio, and the myriad of applications that are transforming industries. Whether you're a seasoned professional or simply curious about cutting-edge technology, understanding the power of synthetic cables could revolutionise your approach to lifting, rigging, and beyond.
Join us as we delve into the world of synthetic cables—where strength meets innovation, and the possibilities are as limitless as your imagination.
Composition and Structure of Synthetic Cables
Have you ever marvelled at the strength and versatility of modern synthetic cables? As someone who's spent years in the rope manufacturing industry, I'm constantly amazed by the ingenious composition and structure of these technological marvels. Let's dive into the fascinating world of synthetic cables and unravel their secrets.
Materials Used in Synthetic Cables
Synthetic cables are a far cry from the natural fibre ropes of yesteryear. They're crafted from man-made materials that offer superior performance in various applications. The most common materials include:
- Polyethylene: Known for its excellent strength-to-weight ratio and resistance to moisture.
- Nylon: Prized for its elasticity and ability to absorb shock loads.
- Polyester: Offers high strength and low stretch, perfect for applications requiring dimensional stability.
- Polypropylene: Lightweight and water-resistant, making it ideal for marine environments.
Each of these materials brings unique properties to the table, allowing manufacturers to tailor cables to specific needs. For instance, a cable designed for heavy lifting might prioritise strength, while one meant for outdoor use might focus on UV resistance.
Hierarchical Structure of Synthetic Ropes
The true genius of synthetic cables lies in their hierarchical structure. Imagine building a massive structure from tiny Lego bricks - that's essentially how synthetic cables are constructed, but on a microscopic scale.
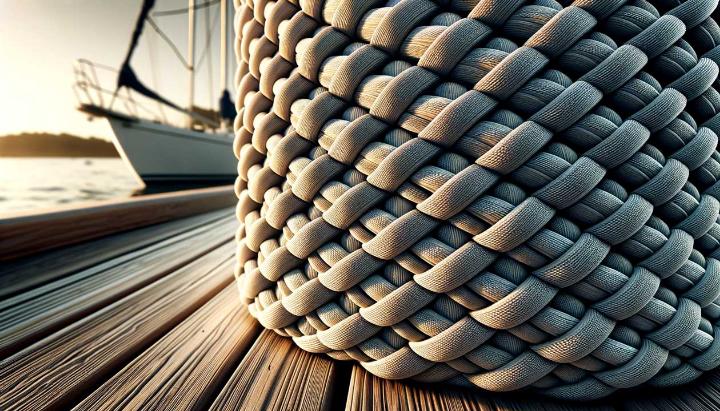
At the most basic level, we start with individual synthetic fibres, each thinner than a human hair. These fibres are twisted or braided together to form yarns. The yarns are then combined to create strands, and finally, the strands are woven or braided to form the finished rope.
This hierarchical structure is what gives synthetic cables their impressive strength. By distributing loads across multiple fibres, strands, and yarns, the rope can withstand forces far greater than the sum of its parts. It's a bit like how a bundle of twigs is much harder to break than a single twig.
But the benefits don't stop at strength. This structure also allows for incredible flexibility and durability. The multiple layers can slide slightly against each other, absorbing shocks and resisting abrasion far better than a solid piece of material ever could.
Have you ever wondered why synthetic cables feel so different from traditional steel cables? It's all down to this unique structure. Next time you handle a synthetic rope, take a moment to appreciate the complex engineering that goes into every fibre.
As we continue to push the boundaries of material science and manufacturing techniques, who knows what incredible advancements we'll see in synthetic cable technology? One thing's for sure - the future of cable manufacturing is looking stronger and more flexible than ever before.
Key Characteristics of Synthetic Cables
As someone who's been in the rope manufacturing industry for over a decade, I've witnessed firsthand the remarkable evolution of synthetic cables. Let's dive into the key characteristics that make these modern marvels stand out from their traditional counterparts.
Lightweight and Flexible Design
One of the most striking features of synthetic cables is their incredibly light weight. I remember the first time I held a synthetic winch line; it felt almost impossibly light in my hands. Did you know that synthetic rope is up to 80% lighter than steel wire rope of the same diameter? This weight reduction has game-changing implications for various industries.
- Easier handling and transportation: The lightweight nature of synthetic cables means less strain on workers and equipment during installation and use.
- Reduced overall weight: In applications like aerospace or automotive, where every gram counts, synthetic cables can significantly contribute to weight savings and improved fuel efficiency.
- Enhanced safety: Lighter cables are less likely to cause injury if they recoil or break under tension.
But it's not just about being lightweight. Synthetic cables also boast remarkable flexibility, allowing them to bend and flex without kinking or damaging their internal structure. This flexibility translates to easier spooling on winches and reduced wear and tear during operation.
High Strength-to-Weight Ratio
Now, you might be wondering, "If these cables are so light, can they really handle heavy loads?" The answer is a resounding yes! In fact, the strength-to-weight ratio of synthetic cables often surpasses that of steel cables.
Did You Know?
Some synthetic ropes can have a breaking strength up to 15 times higher than steel cable of the same weight!
This exceptional strength-to-weight ratio opens up new possibilities in industries where high load capacity and minimal weight are crucial. For instance, in offshore operations, synthetic cables allow for deeper sea exploration and more efficient oil and gas extraction.
However, it's important to note that while synthetic cables excel in tensile strength, they may have lower abrasion resistance compared to steel cables. This is why proper handling and regular inspections are crucial for maintaining their integrity.
As we continue to explore the world of synthetic cables, I'm constantly amazed by their versatility and potential. Whether you're working in marine environments, aerospace, or even everyday applications like towing, synthetic cables offer a compelling alternative to traditional steel cables. Have you considered making the switch to synthetic in your operations? The benefits might just surprise you.
Applications and Industries Utilizing Synthetic Cables
As a seasoned rope manufacturer, I've witnessed the remarkable transformation of various industries through the adoption of synthetic cables. These versatile marvels have found their way into numerous applications, revolutionising operations across the board. Let's explore how synthetic cables are making waves in different sectors.
Benefits of Synthetic Cables in Industrial Applications
The advantages of synthetic cables in industrial settings are truly game-changing. I remember visiting a bustling shipyard where the switch to synthetic winch ropes had dramatically improved efficiency. Here are some key benefits:
- Significant weight reduction: Synthetic ropes are up to 80% lighter than steel cables, reducing strain on equipment and operators.
- Enhanced safety: The lighter weight and flexibility of synthetic ropes minimise recoil risk, creating a safer work environment.
- Improved efficiency: Easier handling and installation of synthetic cables lead to reduced downtime and increased productivity.
These benefits have led to widespread adoption in industries such as commercial fishing, mining, and marine operations. For instance, HMPE (Ultra High Molecular Weight Polyethylene) fiber ropes have become the go-to choice for deep-sea trawling, offering unparalleled strength and durability in harsh marine environments.
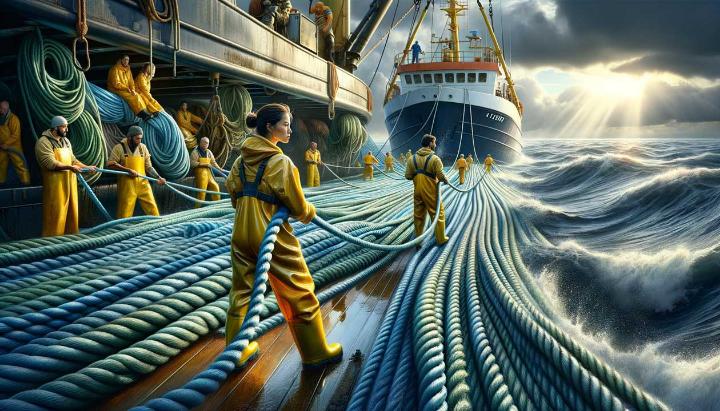
Comparing Synthetic Ropes to Steel Wire Cables
To truly appreciate the impact of synthetic cables, let's compare them to traditional steel wire cables:
Characteristic | Synthetic Ropes | Steel Wire Cables |
---|---|---|
Weight | Lightweight | Heavy |
Strength-to-Weight Ratio | High | Moderate |
Flexibility | Highly flexible | Less flexible |
Abrasion Resistance | Moderate | High |
UV Resistance | Excellent | Poor |
Corrosion Resistance | Excellent | Poor |
While synthetic ropes excel in many areas, it's important to note that they may have lower abrasion resistance compared to steel cables. This is why proper handling and regular inspections are crucial for maintaining their integrity.
In my experience, synthetic cables outperform steel cables in scenarios where weight reduction and ease of handling are paramount. For instance, in offshore wind farm installations, the use of synthetic mooring lines has enabled the deployment of floating turbines in deeper waters, opening up new possibilities for renewable energy generation.
Have you considered the potential benefits of synthetic cables in your industry? Whether you're in marine operations, aerospace, or transportation, the unique properties of synthetic ropes could be the key to unlocking new levels of efficiency and safety in your operations. Learn more about rope materials and their applications to make an informed decision.
Maintenance and Safety Considerations for Synthetic Cables
As someone who's spent years working with synthetic cables, I can't stress enough the importance of proper maintenance and safety practices. These high-performance ropes are incredible pieces of engineering, but they require careful attention to ensure they perform at their best and keep your operations safe. Let's dive into some essential tips that'll help you get the most out of your synthetic cables.
Essential Cleaning and Storage Practices
Keeping your synthetic cables clean and storing them correctly can significantly extend their lifespan. Here's how I approach it:
- Clean regularly with pH neutral soap: After a day's work, I always give my ropes a gentle wash with mild soap and lukewarm water. This removes dirt, salt, and other contaminants that can degrade the fibres over time.
- Rinse thoroughly: I make sure to rinse the rope completely to remove all soap residue, which can attract dirt if left on the rope.
- Air dry in a shaded area: Direct sunlight can damage synthetic fibres, so I always dry my ropes in a well-ventilated, shaded spot.
- Store in a cool, dry place: Once dry, I coil the rope loosely and store it in a clean, dry area away from direct sunlight and chemical exposure.
Remember, proper storage is just as crucial as cleaning. I've seen perfectly good ropes ruined by improper storage, so don't overlook this step!

Safety Precautions for Synthetic Rope Usage
Safety should always be your top priority when working with synthetic cables. Here are some crucial practices I've learned over the years:
- Know your rope's limits: Always adhere to the manufacturer's guidelines for working load limits. For example, OSHA recommends a safety factor of 6 for polypropylene ropes and 9 for nylon or polyester ropes.
- Inspect before every use: I make it a habit to run the rope through my hands, feeling for any cuts, frays, or abrasions. Visual inspection is important, but touch can reveal issues you might miss with your eyes alone.
- Avoid sharp edges and kinks: When setting up your rigging, ensure the rope isn't rubbing against any sharp edges. Also, avoid creating sharp bends or kinks in the rope, as these can significantly weaken its strength.
- Protect from heat and chemicals: Synthetic ropes are sensitive to extreme heat and certain chemicals. Keep them away from hot surfaces and be mindful of any chemical exposure in your work environment.
One thing I've learned the hard way: never underestimate the importance of proper training. Ensure everyone on your team knows how to handle, inspect, and care for synthetic cables correctly. It's not just about preserving your equipment; it's about keeping everyone safe.
Remember: A well-maintained synthetic cable is a safe synthetic cable. Regular inspections and proper care aren't just good practices - they're essential for preventing accidents and ensuring optimal performance.
By following these maintenance and safety guidelines, you'll not only extend the life of your synthetic cables but also create a safer working environment. Have you implemented any of these practices in your operations? If not, now's the perfect time to start. Your equipment - and your team - will thank you for it.
Synthetic cables are revolutionising various industries with their remarkable characteristics and benefits over traditional steel cables. Composed of advanced materials like polyethylene and aramid, these cables boast exceptional strength, flexibility, and durability due to innovative braiding techniques. They are lightweight, making them easier to handle and transport, and offer high tensile strength, resistance to corrosion, chemicals, and UV radiation. Their applications are diverse, spanning marine, aerospace, automotive, and defence sectors. Proper maintenance, including regular inspections and adherence to safety protocols, ensures their longevity and performance. Embrace the future of materials science with synthetic cables for enhanced efficiency and safety in your operations.
Unlock the Potential of Synthetic Cables
Ready to elevate your operations with synthetic cables? Fill in the form above to get customised solutions and expert advice tailored to your needs.