Imagine a construction site where a heavy load needs to be lifted, but the slightest misstep could spell disaster. The choice of sling used for this critical task is far more consequential than it might seem. While flat slings have been a go-to option for many lifting applications, their inherent limitations can put safety and efficiency at risk. Enter lifting rope slings – the unsung heroes of material handling that outperform their flat counterparts in ways that truly matter.
Lifting rope slings, with their ingenious helical design and circular cross-section, offer unparalleled advantages in strength, flexibility, and durability. These robust slings effortlessly conform to the contours of the load, evenly distributing forces and reducing the risk of damage or slippage – a game-changer for handling awkward or irregularly shaped objects. But that's just the beginning.
From harsh environments to heavy-duty applications, lifting rope slings prove their mettle time and again. Their superior resistance to abrasion, cutting, and wear ensures a prolonged service life, translating to lower replacement costs and an unbeatable overall value. It's a win-win situation for businesses seeking a cost-effective yet reliable lifting solution that prioritizes safety without compromising performance.
Limitations of Flat Sling Lifting
Flat slings, also known as webbing slings, have been a popular choice for many lifting applications due to their versatility and ease of use. However, it's essential to understand their inherent limitations to ensure safe and effective lifting operations.
Safety Factors and Load Limits
One of the critical factors to consider when using flat slings is their safety factor and working load limits. According to the Australian Standard AS1353, flat slings have a safety factor of 8:1. This means that the sling's rated capacity must be at least eight times greater than the intended load.
- Working load limits decrease with sling angle. As the angle of the sling from the horizontal decreases, the working load limit also decreases. This is an essential consideration when lifting asymmetrical loads or in situations where the sling angles change during the lift.
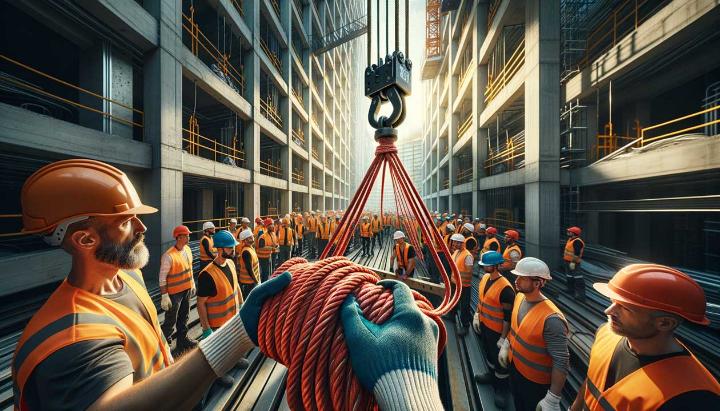
It's crucial never to exceed the rated working load limit of a flat sling, as it can lead to catastrophic failures and potential accidents.
Handling Considerations and Precautions
Flat slings are generally not recommended for dynamic or shock-loaded lifting applications without proper precautions. The flat profile and woven construction make them more susceptible to damage from sudden impacts or jerky movements.
Additionally, synthetic flat slings can be susceptible to environmental factors such as chemicals, UV rays, and abrasion. Exposure to these elements can degrade the sling material over time, reducing its strength and increasing the risk of failure.
- Regular inspections and proper handling are essential. Before each use, thoroughly inspect the sling for signs of wear, cuts, abrasions, or other damage. Follow the manufacturer's guidelines for safe handling, storage, and maintenance to prolong the sling's service life.
By understanding these limitations and adhering to safety protocols, you can ensure that flat slings are used appropriately and within their intended capabilities.
Advantages of Lifting Rope Sling Design
When it comes to heavy-duty lifting applications, wire rope slings stand out as a superior choice over traditional flat slings. Their unique design, featuring a helical pattern of steel wires and strands, offers a winning combination of strength, flexibility, and cost-effectiveness that sets them apart.
Strength and Flexibility of Wire Rope Slings
At the core of a wire rope sling lies a carefully engineered arrangement of multiple steel wires twisted into strands around a fiber or steel core. This ingenious construction creates a sling that boasts exceptional strength while maintaining remarkable flexibility.
Unlike flat slings, which can be rigid and struggle with bending, wire rope slings effortlessly conform to the shape of the load, evenly distributing the forces and reducing the risk of damage or slippage. This inherent flexibility makes them ideal for handling awkward or irregularly shaped objects, ensuring a secure grip and safe lifting operations.
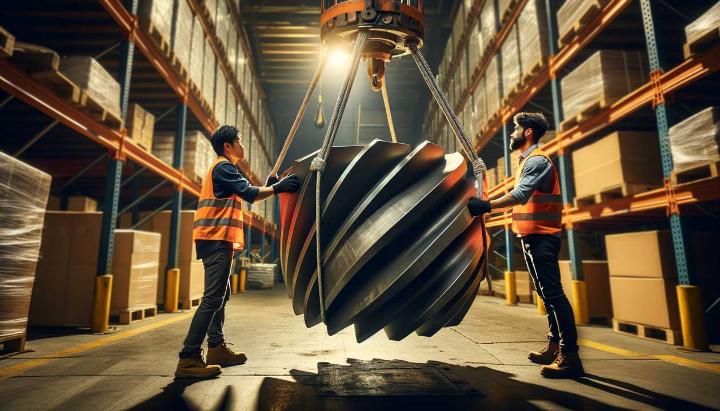
Whether you're lifting heavy machinery, construction materials, or bulky equipment, wire rope slings can handle the job with ease, adapting to the contours and bending stresses without compromising structural integrity.
Cost-Effectiveness and Versatility
Beyond their strength and flexibility, wire rope slings offer a compelling advantage in terms of cost-effectiveness. When you consider the "cost per ton" of lift, these slings often prove to be the more economical choice, especially for heavy-duty applications.
Moreover, wire rope slings are remarkably versatile, capable of handling a wide range of materials, including hot or abrasive loads that could easily damage other sling types. Their resistance to cutting and abrasion allows them to be used in harsh environments, making them a preferred choice for industries like construction, manufacturing, and mining.
Customization is another key benefit of wire rope slings. With various hardware configurations and options available, these slings can be tailored to meet the specific requirements of your lifting application, ensuring optimal performance and safety. For instance, explore our collection of durable and secure lugs for a wide range of applications.
Real-World Applications
From shipyards and steel mills to power plants and construction sites, wire rope slings are the go-to choice for their unparalleled strength, flexibility, and versatility. For more insights, read about comparing strong ropes and strong wire rope.
By leveraging the advantages of wire rope sling design, businesses across industries can streamline their lifting operations, maximize efficiency, and prioritize safety – all while enjoying the long-term cost benefits of a durable and versatile sling solution.
Durability and Longevity of Lifting Rope Slings
In the demanding world of material handling and lifting operations, safety and reliability are paramount. But beyond that, you also need equipment that can withstand the rigors of heavy use and harsh environments. That's where lifting rope slings truly shine, offering superior durability and longevity compared to their flat sling counterparts.
Factors Affecting Lifespan of Rope Slings
The lifespan of a rope sling is influenced by several factors, including the frequency of use, the weight and nature of the loads being lifted, and the storage and handling conditions. Frequent use and exposure to harsh environments can accelerate wear and tear, while proper maintenance and storage can extend the sling's service life.
- Material composition is a key factor. Rope slings can be made from various materials, each with its own unique properties and durability characteristics. For example, polyester slings are known for their strength and resistance to chemical exposure, but they can be more prone to abrasion and UV damage over time. In contrast, wire rope slings are highly resistant to cutting, abrasion, and environmental factors, making them a popular choice for heavy-duty applications.
- Proper handling and storage are crucial. Even the toughest rope sling can succumb to damage if not handled and stored correctly. Avoid dragging slings across rough surfaces, exposing them to excessive heat or moisture, or storing them in areas with potential sources of damage. Following the manufacturer's guidelines for handling, inspection, and storage can significantly prolong the sling's lifespan.
Remember
Adhering to industry standards and manufacturer recommendations is essential for maximizing the service life of your lifting rope slings. For more information on high-quality rope solutions, explore premium quality rope solutions.
Recommended Lifespan and Inspection Guidelines
While the actual lifespan of a rope sling can vary based on usage and environmental conditions, industry guidelines typically recommend a service life of 6 to 10 years for wire rope slings and 3 to 5 years for synthetic fiber slings. However, it's important to note that these are general guidelines and that regular inspections are crucial for determining the sling's actual condition and remaining lifespan.
- Regular inspections are essential. Most experts recommend inspecting rope slings at least once every 6 months or more frequently if they are used in harsh or demanding environments. During these inspections, look for signs of wear, such as broken wires, cuts, abrasions, or deformities in the sling's structure. Any sling that shows signs of significant damage or wear should be immediately removed from service and replaced.

By investing in high-quality lifting rope slings and following proper maintenance and inspection protocols, you can minimize replacement costs and enjoy the long-term benefits of a durable, reliable, and cost-effective lifting solution.
Discover Why Lifting Rope Slings Are Superior
Flat sling lifting, while versatile, falls short due to its susceptibility to damage, limited flexibility, and reduced lifting sling capacity. In contrast, lifting rope slings offer significant advantages. Their enhanced flexibility allows them to conform to loads better, while their resistance to abrasion and higher capacity make them ideal for demanding applications. Furthermore, lifting rope slings excel in durability and longevity, providing superior wear resistance and a longer service life, ultimately reducing replacement costs and improving value. Explore our solutions today and ensure optimal lifting performance. Don't forget to inquire using the form above for more details.