Did you know that a wire rope sling with the same diameter as a UHMWPE sling can be outperformed in terms of strength-to-weight ratio? It's a game-changer in the world of lifting operations, and it's reshaping how industries approach heavy-duty tasks.
Welcome to the fascinating realm of wire rope sling capacities and types. Whether you're a seasoned rigging professional or new to the field, understanding these crucial components can mean the difference between a successful lift and a costly disaster. In this comprehensive guide, we'll delve into the intricacies of wire rope sling capacities, explore the various types available, and compare them to their UHMWPE counterparts.
But why should you care? Simply put, choosing the right sling for your specific needs can dramatically improve safety, efficiency, and cost-effectiveness in your operations. We'll walk you through everything from load capacity charts to customisation options, drawing on real-world examples and expert insights.
As we navigate this complex topic, we'll also spotlight iRopes, a professional rope supplier renowned for their ability to customise slings to meet unique customer requirements. Their expertise in both wire rope and UHMWPE slings makes them an invaluable resource in our exploration.
So, buckle up and prepare to elevate your knowledge of wire rope slings. By the end of this post, you'll be equipped with the information you need to make informed decisions that could revolutionise your lifting operations. Let's dive in!
Understanding Wire Rope Sling Capacities
When it comes to lifting heavy loads, understanding wire rope sling capacities is crucial for ensuring safe and efficient operations. As someone who's spent years in the rigging industry, I can't stress enough how important it is to get this right. Let's dive into the nitty-gritty of wire rope sling capacities and explore the factors that influence them.
Factors Affecting Wire Rope Sling Load Capacity
Several key elements determine the load-bearing capacity of a wire rope sling. Picture this: you're standing on a construction site, about to lift a massive steel beam. The success of your lift depends on these critical factors:
- Wire rope strength and construction: The core material, wire grade, and layering pattern all play a role in determining the sling's overall strength.
- Sling hardware: The quality and rating of end fittings, such as hooks or shackles, can impact the sling's capacity.
- Hitch type: Different hitches (vertical, choker, basket) affect how the load is distributed and, consequently, the sling's capacity.
- Sling angle: The angle at which the sling is used can significantly alter its lifting capacity.
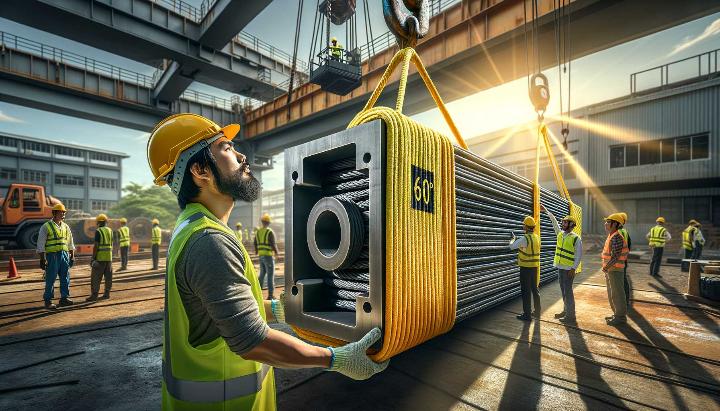
Calculating Safe Working Load for Wire Rope Slings
Now, let's talk about the all-important safe working load (SWL). This is the maximum weight a sling can safely lift under normal working conditions. Here's a simple formula to remember:
SWL = Breaking Strength ÷ Safety Factor
For example, if a wire rope sling has a breaking strength of 10,000 kg and we apply a safety factor of 5:1, the SWL would be 2,000 kg. Always err on the side of caution when calculating SWL – it's better to be safe than sorry!
Types of Wire Rope Sling Hitches and Their Impact on Capacity
The way you attach a sling to a load can make a world of difference. Let's break down the most common hitch types and their effects on capacity:
- Vertical hitch: Offers 100% of the sling's rated capacity.
- Choker hitch: Reduces capacity to about 75-80% of the vertical rating.
- Basket hitch: Can potentially double the capacity, but be cautious with the sling angle.
Remember, sling angles less than 30 degrees are a big no-no. They put excessive stress on the sling and can lead to catastrophic failures.
Always consult manufacturer-provided load capacity charts for accurate ratings. Never exceed the working load limit (WLL) specified for your wire rope sling.
Understanding wire rope sling capacities is not just about numbers – it's about safety, efficiency, and peace of mind. By considering all these factors and using the right tools for the job, you'll be well-equipped to handle even the most challenging lifting tasks. Remember, when in doubt, always consult with a rigging expert or refer to the manufacturer's guidelines. Your safety and the integrity of your load depend on it!
Types of Wire Rope Slings: An In-Depth Guide
As someone who's spent years working with various rigging equipment, I can tell you that wire rope slings are the unsung heroes of the lifting world. They're like the Swiss Army knives of rigging - versatile, reliable, and essential for a wide range of lifting applications. Let's dive into the fascinating world of wire rope sling types and configurations.
Common Wire Rope Sling Configurations
When I first started in this industry, the sheer variety of wire rope slings overwhelmed me. But over time, I've come to appreciate how each type serves a unique purpose. Here are the main configurations you'll encounter:
- Single leg slings: The simplest form, perfect for straightforward vertical lifts.
- Double leg slings: Offer more stability and are great for balancing uneven loads.
- Multi-leg slings: Typically with four legs, these are ideal for lifting large or awkwardly shaped objects.
- Endless loop slings: Flexible and versatile, these can be used in various hitches.
- Reverse eye slings: Feature eyes on both ends, allowing for easy attachment to hooks or shackles.
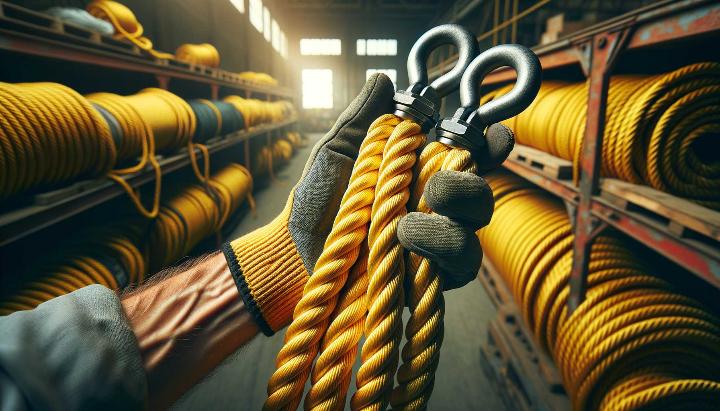
Each configuration affects the sling's lifting capacity differently. For instance, a basket hitch can potentially double a sling's capacity compared to a vertical hitch. But remember, always consult the manufacturer's load charts for precise ratings.
Choosing the Right Wire Rope Sling for Your Application
Selecting the appropriate wire rope sling isn't just about lifting capacity. It's about matching the sling to your specific needs. Here are some factors to consider:
- Load weight and shape: This will determine the number of legs and configuration needed.
- Environmental conditions: Consider factors like temperature, chemical exposure, and abrasion risks.
- Frequency of use: High-frequency applications may require more durable sling types.
- Industry-specific requirements: Some industries have unique safety standards or preferences.
For example, in my experience working with offshore oil rigs, we often opted for galvanized wire rope slings to resist corrosion from saltwater exposure. It's these small but crucial details that can make all the difference in your lifting operations.
Did you know? Specialty wire rope slings, like those with protective sleeves or high-temperature resistant materials, are available for unique applications. Always consult with a rigging expert or supplier like iRopes for customised solutions.
Understanding wire rope sling types is crucial for safe and efficient lifting operations. By matching the right sling to your specific needs, you're not just lifting loads - you're lifting them smartly and safely. Remember, when in doubt, don't hesitate to reach out to a professional supplier for guidance. Your safety and the integrity of your lift depend on it!
Choosing the Right Wire Rope Sling Suppliers
When it comes to rigging operations, the importance of selecting reliable wire rope sling suppliers cannot be overstated. As someone who's been in the industry for years, I've seen firsthand how the right supplier can make all the difference in terms of safety, efficiency, and overall project success. Let's dive into what you need to know to make an informed choice.
Factors to Consider When Selecting Wire Rope Slings
Choosing the right wire rope sling isn't just about picking the strongest option. It's about finding the perfect balance between capacity, durability, and suitability for your specific needs. Here are some crucial factors to keep in mind:
- Wire rope sling capacity: Understanding the safe working load (SWL) is crucial. Remember the rule of thumb: SWL (kg) = D² (mm) x 8, where D is the rope diameter. But always refer to manufacturer specifications for precise ratings.
- Environmental conditions: Will your slings be exposed to extreme temperatures, chemicals, or saltwater? These factors can significantly impact sling performance and lifespan.
- OSHA regulations: Ensure your supplier adheres to OSHA guidelines. For instance, did you know that OSHA prohibits shortening slings with knots or makeshift devices?
- Quality and durability: Look for slings made from high-grade materials with proper construction techniques. A well-made sling can be the difference between a successful lift and a costly accident.
Pro tip: Always ask your supplier for detailed load capacity charts and usage instructions. This information is invaluable for ensuring safe and efficient operations.
Top Wire Rope Sling Manufacturers and Suppliers
While there are many suppliers out there, not all are created equal. Here's a quick rundown of what to look for in a top-tier supplier:
- Quality certifications: Look for suppliers with ISO 9001 certification and other relevant industry standards.
- Customisation capabilities: The ability to tailor slings to your specific needs can be a game-changer. For instance, iRopes offers extensive customisation options, from material selection to specific performance characteristics.
- Technical expertise: A supplier should be more than just a vendor. They should be a partner who can provide valuable advice and support.
- Comprehensive product range: A supplier with a wide range of products, including specialty slings, can cater to all your rigging needs.
When evaluating suppliers, don't just focus on price. Consider factors like customer service, delivery times, and after-sales support. Remember, the cheapest option upfront might end up costing you more in the long run if it compromises on quality or safety.
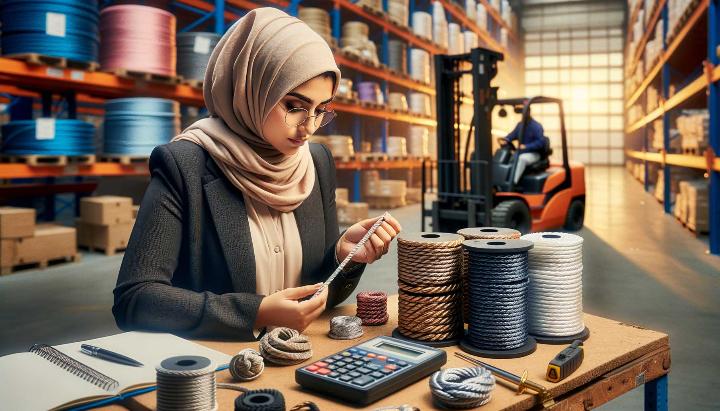
Choosing the right wire rope sling supplier is a critical decision that can impact the safety and efficiency of your operations. By considering factors like sling capacity, quality standards, and customisation options, you can ensure you're getting the best possible product for your needs. Remember, a reliable supplier isn't just selling you a product; they're providing peace of mind. So take your time, do your research, and don't hesitate to ask questions. Your safety and success depend on it!
Comparing Wire Rope Slings to UHMWPE Slings: Strength and Performance
As someone who's been in the rigging industry for years, I've seen the evolution of lifting technologies firsthand. Today, we're going to dive into a comparison that's been turning heads in our field: wire rope slings versus UHMWPE slings. Trust me, this isn't just about swapping one material for another – it's about understanding how these choices can revolutionise your lifting operations.
Key Differences Between Wire Rope and UHMWPE Slings
Let's break down the main differences between these two titans of the lifting world:
- Strength-to-weight ratio: UHMWPE slings are like the superhero version of lifting gear. They're incredibly strong yet surprisingly lightweight. In fact, UHMWPE is so strong that it can outperform steel wire rope of the same diameter.
- Flexibility and handling: If you've ever wrestled with a heavy wire rope sling, you'll appreciate the flexibility of UHMWPE. It's like comparing a rigid garden hose to a soft, pliable rope – UHMWPE slings are much easier to manoeuvre and position.
- Durability in different environments: Wire rope slings are the tough guys of the industry, holding up well against abrasion and high temperatures. UHMWPE, while strong, can be more susceptible to cuts and doesn't fare as well in extreme heat.

To put things into perspective, let's look at a quick comparison:
Property | Wire Rope Slings | UHMWPE Slings |
---|---|---|
Strength-to-weight ratio | Good | Excellent |
Flexibility | Moderate | High |
Heat resistance | High | Low |
Abrasion resistance | High | Moderate |
Advantages of UHMWPE Slings Over Traditional Materials
Now, let's talk about why UHMWPE slings are making waves in the industry:
- Incredible strength: UHMWPE fibres, like Dyneema, are pound-for-pound stronger than steel. This means you can lift heavier loads with lighter slings.
- Lightweight nature: I remember a job where we switched from wire rope to UHMWPE slings. The difference in handling was night and day – our team experienced less fatigue and could work more efficiently.
- Safety benefits: The lightweight nature of UHMWPE slings reduces the risk of back injuries during handling. Plus, they're less likely to recoil dangerously if they break under tension.
In my experience, industries like offshore oil and gas, wind energy, and aerospace have been quick to adopt UHMWPE slings. They're particularly useful in situations where weight is a critical factor or where corrosion resistance is needed.
Did you know? Plasma rope, an advanced type of synthetic rope, is pushing the boundaries of what's possible in heavy-duty lifting applications. It's worth keeping an eye on as the technology develops.
At the end of the day, choosing between wire rope and UHMWPE slings comes down to your specific needs. Are you lifting in high-temperature environments? Wire rope might be your best bet. Need to reduce weight in your rigging setup? UHMWPE could be the game-changer you're looking for.
Remember, whether you're opting for traditional wire rope slings or exploring the benefits of UHMWPE, quality matters. That's where suppliers like iRopes come in. With their ability to customise slings to your exact specifications, you can ensure you're getting the right tool for the job, every time.
Have you used both wire rope and UHMWPE slings in your operations? I'd love to hear about your experiences. Share your thoughts in the comments below!
Mastering wire rope sling capacities and types is essential for safe lifting operations across various industries. This blog delves into the factors influencing wire rope sling capacities, such as construction, hardware, hitch type, and sling angle. It outlines how to correctly calculate safe working loads and understand different wire rope sling types like single leg, double leg, and multi-leg configurations. The comparison between wire rope and UHMWPE slings highlights their respective benefits, including strength, flexibility, and environmental durability. Choosing the right wire rope sling suppliers is crucial, and iRopes, a leading manufacturer, offers customised solutions tailored to specific needs. Whether you require wire rope or UHMWPE slings, ensure they meet quality standards and your operational requirements.
Get Expert Customisation for Your Lifting Needs
To find the perfect wire rope sling for your operations, fill out the form above. Our experts at iRopes are ready to assist with custom solutions that ensure safety and efficiency in your lifting tasks.