Have you ever wondered why some ropes snap under pressure while others hold firm? The answer lies in understanding the breaking strength of polypropylene rope - a crucial factor that can mean the difference between safety and disaster in various applications. As a leading rope manufacturer with 15 years of experience, iRopes has seen firsthand how this knowledge can save lives and ensure project success.
Polypropylene rope is a versatile synthetic cordage used in marine, racing sports, industrial, and safety applications. Its strength, durability, and cost-effectiveness have made it a popular choice for both professionals and enthusiasts. However, not all polypropylene ropes are created equal, and understanding their breaking strength is essential for making informed decisions.
In this comprehensive guide, we'll delve into the fascinating world of polypropylene rope strength, exploring the factors that influence it, testing methods, and how to choose the right rope for your specific needs. Whether you're securing cargo on a ship, rigging equipment for a construction project, or planning an outdoor adventure, this knowledge will empower you to make safer, more effective choices.
Join us as we unravel the secrets of polypropylene rope breaking strength and discover how iRopes' expertise in crafting high-quality synthetic ropes can elevate your projects to new heights of safety and performance. Are you ready to become a rope strength expert? Let's dive in!
Understanding Polypropylene Rope Strength
When it comes to selecting the right rope for your needs, understanding the strength of polypropylene rope is crucial. As an avid sailor and outdoor enthusiast, I've learned firsthand how important it is to choose the right rope for each application. Let's dive into the world of polypropylene rope strength and explore what makes this synthetic marvel so versatile.
Breaking Strength and Safe Working Load
Before we get into the nitty-gritty, it's essential to understand two key concepts: breaking strength and safe working load. Breaking strength is the maximum load a rope can handle before it fails, while the safe working load is typically a fraction of that - usually about 20% of the breaking strength. This buffer ensures safety in real-world applications where dynamic loads and environmental factors come into play.
Breaking Strength Formula
Square of rope diameter (mm) ÷ 77 tonnes
For example, an 8mm polypropylene rope has a breaking strength of about 1,040kg. But remember, you should never load a rope to its breaking point. Always work within the safe working load to ensure longevity and safety.
Factors Affecting Polypropylene Rope Strength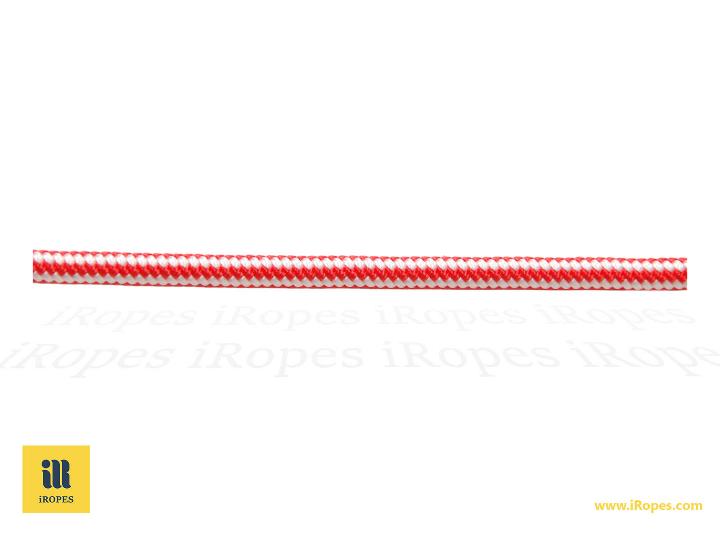
Several factors influence the strength of polypropylene rope:
- Rope diameter: Generally, the thicker the rope, the stronger it is. However, this also means increased weight and reduced flexibility.
- Construction: Three-strand and 8-strand constructions offer different strength profiles. 8-strand ropes are typically stronger but may be more expensive.
- Environmental conditions: UV exposure can degrade polypropylene over time. That's why many manufacturers add UV stabilizers to improve durability.
I once made the mistake of using an old, sun-damaged polypropylene rope for a heavy load. Needless to say, it didn't end well! Always inspect your ropes regularly and replace them if you notice any signs of wear or degradation.
Remember, knowing your rope's limits is crucial for safety. Always err on the side of caution and choose a rope with a higher breaking strength than you think you'll need.
Understanding polypropylene rope strength isn't just about numbers - it's about making informed decisions to ensure safety and efficiency in your projects. Whether you're securing a load on a truck or rigging a sailboat, choosing the right rope can make all the difference.
Have you ever had an experience where understanding rope strength was crucial? Share your story in the comments below!
Factors Influencing Polypropylene Rope Breaking Strength
As a seasoned sailor and rope enthusiast, I've learned that understanding the breaking strength of polypropylene rope is crucial for ensuring safety and efficiency in various applications. Let's dive into the key factors that influence this important characteristic.
Physical Properties Affecting Rope Strength
The breaking strength of polypropylene rope is primarily determined by its physical properties. Here are the main factors to consider:
- Rope diameter: Generally, the thicker the rope, the higher its breaking strength. However, this also means increased weight and reduced flexibility.
- Construction method: The way a rope is constructed significantly impacts its strength. For example, braided ropes often have higher breaking strengths compared to twisted ropes.
- Fibre quality: The grade and quality of polypropylene fibres used in manufacturing play a crucial role in determining the rope's overall strength.
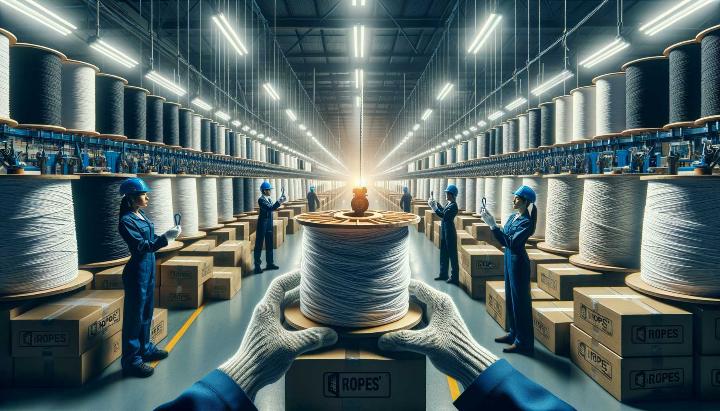
Environmental Factors Impacting Breaking Strength
Environmental conditions can significantly affect the breaking strength of polypropylene rope over time. Here's what you need to know:
- UV radiation: Prolonged exposure to sunlight can degrade polypropylene fibres, reducing the rope's strength. UV stabilisers are often added to mitigate this effect.
- Temperature fluctuations: Extreme heat or cold can alter the rope's properties. In my experience, polypropylene ropes tend to become more brittle in freezing conditions.
- Moisture and chemicals: While polypropylene is naturally water-resistant, prolonged exposure to moisture or harsh chemicals can weaken the rope over time.
I once left a polypropylene rope exposed to the harsh Australian sun for an entire summer. When I tried to use it for a heavy load, it snapped unexpectedly. This taught me a valuable lesson about proper rope care and storage.
Safe Working Load and Safety Factors
Understanding the relationship between breaking strength and safe working load is crucial for using polypropylene ropes safely:
- Safe working load: This is typically calculated as a fraction of the breaking strength, usually around 20%.
- Safety factors: Industry standards often recommend using a safety factor of 5 to 12 times the intended load, depending on the application.
Always err on the side of caution when calculating safe working loads. For critical applications, consult with a professional rope manufacturer like iRopes to ensure you're using the right rope for the job.
By considering these factors and understanding how they influence the breaking strength of polypropylene rope, you can make informed decisions about rope selection and use. Remember, proper care and regular inspections are key to maintaining your rope's strength and ensuring safety in all your rope-related activities.
Have you ever experienced a rope failure due to overlooking one of these factors? Share your story in the comments below – your experience could help others avoid similar situations!
Testing Polypropylene Rope Breaking Strength
As a rope enthusiast and safety advocate, I've always been fascinated by the science behind rope strength. Let's dive into the world of polypropylene rope testing and uncover the secrets behind those crucial breaking strength numbers.
Measuring Tensile Strength of Polypropylene Rope
When it comes to testing polypropylene rope breaking strength, it's all about the tensile strength. Imagine stretching a rope between two points until it snaps - that's essentially what happens in a controlled laboratory environment.
The setup for these tests is quite impressive. Picture massive machines with large diameter capstans, designed to apply gradually increasing force to the rope. It's like a tug-of-war between two giants, with the rope caught in the middle.
Here's a simplified breakdown of the testing process:
- Preparation: The rope is carefully measured and marked for accurate results.
- Setup: The rope is securely fastened to the testing machine's capstans.
- Tension application: Force is gradually applied until the rope breaks.
- Data collection: The maximum force applied before breaking is recorded.
The results? A precise measurement of the rope's breaking strength, typically expressed in kilograms or tonnes.
Did you know? The breaking strength of polypropylene rope can be estimated using this formula: Square of rope diameter (mm) ÷ 77 tonnes. However, always rely on official test results for critical applications.
Factors Affecting Rope Breaking Strength
Several factors influence the breaking strength of polypropylene rope:
- Rope diameter: Generally, thicker ropes have higher breaking strengths. For example, a 6mm polypropylene rope might have a breaking strength of 590kg, while a 14mm rope could withstand up to 2990kg.
- Construction method: Braided ropes often exhibit higher strength compared to twisted varieties.
- Environmental conditions: Exposure to UV radiation, extreme temperatures, and chemicals can degrade rope strength over time.
Understanding these factors is crucial for selecting the right rope for your needs. I once learned this lesson the hard way when a seemingly sturdy rope snapped during a sailing trip - always check the specs and consider the environmental conditions!
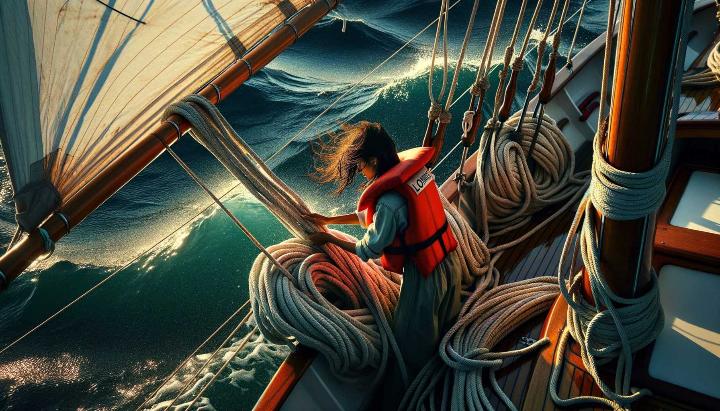
Remember, while breaking strength is important, it's the working load limit that really matters in practical applications. This is typically about 20% of the breaking strength, providing a safety margin for real-world use.
Have you ever witnessed a rope strength test or experienced a rope failure? Share your story in the comments - your experience could help others make informed decisions about rope selection and use.
Choosing the Right Polypropylene Rope Based on Breaking Strength Requirements
As a seasoned sailor and rope enthusiast, I've learned that selecting the perfect polypropylene rope for your specific needs is crucial for safety and efficiency. Let's dive into the process of choosing the right rope based on breaking strength requirements, and explore how working with professional manufacturers like iRopes can make all the difference.
Assessing Your Specific Application and Load Requirements
Before selecting a polypropylene rope, it's essential to thoroughly evaluate your intended use and load requirements. Here are some key factors to consider:
- Maximum load: Determine the heaviest weight your rope will need to support.
- Dynamic vs. static loads: Consider whether the rope will be subjected to sudden jerks or constant tension.
- Environmental conditions: Factor in exposure to UV rays, chemicals, or extreme temperatures.
- Frequency of use: Assess how often the rope will be used and the level of wear it may endure.
I once made the mistake of using a lightweight polypropylene rope for a heavy mooring application. Needless to say, it didn't end well! Always err on the side of caution when assessing your load requirements.
Considering Safety Factors and Industry Standards
When choosing a polypropylene rope based on breaking strength, it's crucial to incorporate appropriate safety factors and adhere to industry standards. Here's what you need to know:
- Safety factor: Most industries recommend a safety factor of 5:1 to 12:1, depending on the application.
- Working load limit (WLL): This is typically 15-20% of the rope's breaking strength.
- Industry-specific standards: Familiarise yourself with regulations relevant to your field, such as marine or construction standards.
Safety Factor Calculation
Working Load Limit (WLL) = Breaking Strength ÷ Safety Factor
For example, if you're working with a polypropylene rope with a breaking strength of 1,000 kg and using a safety factor of 5:1, your working load limit would be 200 kg.
The Role of Professional Rope Manufacturers
Working with experienced rope manufacturers like iRopes can significantly simplify the process of selecting the right polypropylene rope. Here's how they can help:
- Expert guidance: Manufacturers can provide valuable insights based on your specific requirements.
- Custom solutions: They can create bespoke ropes tailored to your unique needs.
- Quality assurance: Reputable manufacturers ensure their products meet or exceed industry standards.
- Comprehensive testing: Professional manufacturers conduct rigorous strength tests to verify breaking strength claims.
I've had the pleasure of working with iRopes on several projects, and their expertise has been invaluable in selecting the perfect rope for each application.
Always consult with a professional rope manufacturer when selecting ropes for critical applications. Their expertise can help ensure optimal performance and safety.
Benefits of Working with Experienced Manufacturers
Collaborating with seasoned rope manufacturers like iRopes offers numerous advantages:
- Access to cutting-edge materials: Stay ahead with the latest advancements in synthetic fibres.
- Customisation options: Tailor your rope's properties to meet specific requirements.
- Comprehensive support: Benefit from ongoing technical assistance and product education.
- Cost-effectiveness: Invest in high-quality ropes that offer longevity and reliable performance.
By leveraging the expertise of professional manufacturers, you can ensure that you're selecting the right polypropylene rope based on your specific breaking strength requirements, ultimately enhancing safety and efficiency in your operations.
Have you ever worked with a professional rope manufacturer to select the perfect rope for your needs? Share your experience in the comments below – your insights could be invaluable to others facing similar decisions!
Understanding the breaking strength of polypropylene rope is essential for safe and efficient use in various applications such as marine, racing sports, and industrial safety. Factors like rope diameter, construction method, and environmental conditions significantly influence the breaking strength of polypropylene rope. It's crucial to work within the safe working load and incorporate safety factors to ensure optimal performance. Collaborating with expert rope manufacturers like iRopes, who have over 15 years of experience, offers several benefits, including access to high-quality materials, custom solutions, and comprehensive support. For high-performance, reliable polypropylene rope solutions, trust iRopes to deliver superior products tailored to your needs.
Get Custom Polypropylene Ropes Tailored to Your Needs
Fill out the form above to get in touch with our experts at iRopes for more information and to discuss your specific requirements for polypropylene rope breaking strength. Our team is ready to help you find the perfect rope solution for your applications.