Did you know that a seemingly simple polyamide rope can support weights of up to 28 times its own mass? In the world of industrial and marine applications, where safety and reliability are paramount, understanding polyamide rope breaking strength isn't just technical knowledge—it's a critical necessity that could mean the difference between success and catastrophic failure.
As a leading manufacturer of high-performance ropes, we've witnessed firsthand how proper comprehension of breaking strength characteristics can dramatically impact everything from maritime operations to industrial lifting. Yet surprisingly, many professionals overlook the crucial factors that influence a rope's breaking strength, potentially compromising safety and efficiency.
In this comprehensive guide, we'll delve into the fascinating world of polyamide rope breaking strength, exploring the unique properties that make these ropes indispensable across diverse applications. Whether you're a seasoned professional or new to rope selection, understanding these fundamental principles will empower you to make informed decisions that enhance safety, optimise performance, and ensure reliability in your specific application.
Join us as we unravel the science behind polyamide rope breaking strength, examining everything from material characteristics to testing methodologies, and discover why this knowledge is essential for anyone working with high-performance rope systems.
Physical Properties of Polyamide Ropes
When it comes to choosing the right rope for your application, understanding the unique characteristics of polyamide ropes can make all the difference. Having worked extensively with various rope materials, I've consistently found polyamide to be one of the most versatile options available.
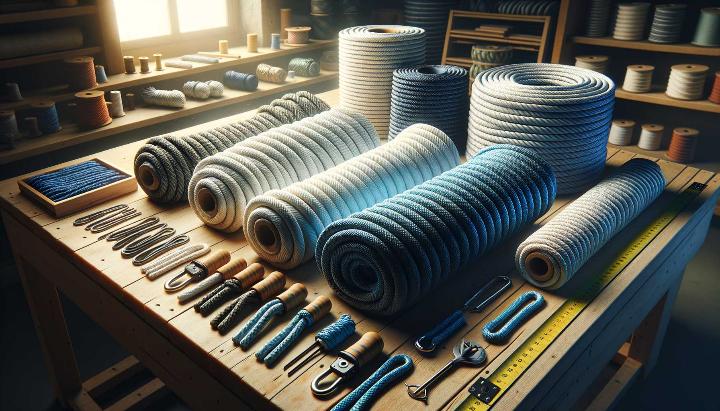
Strength and Durability Characteristics
What sets polyamide ropes apart is their remarkable combination of strength and flexibility. With a specific gravity of 1.14 kg/dm3 and a melting point of 215°C, these ropes offer exceptional durability while remaining surprisingly lightweight. Have you ever wondered why climbing enthusiasts often prefer polyamide ropes? The answer lies in their unique properties.
- Superior Abrasion Resistance: The molecular structure of polyamide fibres creates a tough outer surface that withstands repeated friction and wear, making these ropes ideal for applications involving frequent contact with rough surfaces.
- Exceptional Flexibility: Unlike stiffer alternatives, polyamide ropes maintain their suppleness even under heavy loads, allowing for easy handling and knot-tying without compromising strength.
- Outstanding Strength-to-Weight Ratio: These ropes deliver impressive breaking strength while keeping weight minimal - a crucial factor for activities where every gram counts.
- Dynamic Load Management: The natural elasticity of polyamide allows these ropes to absorb sudden shocks and impacts, reducing the risk of sudden breaks under dynamic loads.
One particularly fascinating aspect of polyamide ropes is their behaviour under different conditions. In wet environments, they can absorb up to 7% moisture, which actually increases their shock-absorption capabilities - a feature that proves invaluable in marine applications.
Did You Know?
Polyamide ropes can stretch up to 15-28% before breaking, providing crucial safety margins in high-stress applications.
Whether you're selecting ropes for industrial use, outdoor adventures, or marine applications, understanding these fundamental characteristics helps ensure you make the right choice for your specific needs. The combination of durability, flexibility, and strength makes polyamide ropes a reliable option across diverse scenarios.
Key Factors Affecting Polyamide Rope Breaking Strength
Building on our understanding of polyamide rope properties, let's dive into the crucial factors that influence their breaking strength. Throughout my years of testing various rope configurations, I've observed how these elements work together to determine a rope's ultimate performance.
Physical and Construction Factors
The foundation of a polyamide rope's breaking strength lies in its physical construction. Have you ever wondered why two ropes of the same material can have dramatically different breaking strengths? The answer lies in the details of their construction.
- Rope Diameter: Each millimeter increase in diameter significantly impacts breaking strength, typically following a geometric progression. For instance, doubling the diameter can quadruple the breaking strength.
- Strand Configuration: The number and arrangement of strands affect both strength and handling characteristics. Three-strand constructions offer excellent grip, while braided patterns provide superior strength-to-weight ratios. Explore the concept of double braid patterns for insights into strength and versatility.
- Core Design: The core's density and construction method can influence breaking strength by up to 30%, with parallel core designs typically offering the highest strength ratings.
- Raw Material Quality: Premium-grade polyamide fibers can increase breaking strength by 15-20% compared to standard materials.
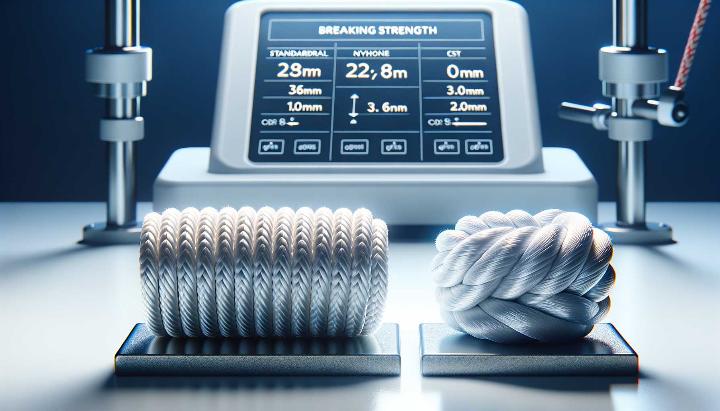
Environmental and Usage Factors
Environmental conditions play a crucial role in maintaining rope strength over time. In my experience working with marine applications, I've seen firsthand how these factors can impact performance. For more details on how different conditions affect ropes, you might want to look into elasticity and environmental adaptions of nylon pull ropes.
- Moisture Exposure: Wet polyamide ropes typically retain 80-90% of their dry breaking strength. While this reduction is temporary, repeated exposure can affect long-term durability.
- UV Radiation: Extended sun exposure can degrade breaking strength by up to 25% over time, making UV protection crucial for outdoor applications.
- Temperature Variations: Extreme temperatures affect performance - high heat can reduce strength by up to 15%, while freezing conditions can increase brittleness.
Important Safety Note
Regular inspection and proper storage can extend your rope's life and maintain its breaking strength. Always replace ropes showing signs of significant wear or exposure damage.
Understanding these factors isn't just about technical specifications - it's about ensuring safety and reliability in real-world applications. Whether you're selecting ropes for industrial use or outdoor activities, considering these factors will help you make informed decisions that match your specific needs.
Testing Methods for Polyamide Rope Breaking Strength
Having explored the factors that influence rope strength, let's dive into the critical process of testing and measuring breaking strength. Throughout my years in rope testing laboratories, I've learned that accurate measurement is as much an art as it is a science.
Standard Testing Procedures and Equipment
The cornerstone of reliable breaking strength measurement lies in standardized testing procedures. Modern testing involves sophisticated equipment and precise methodologies that have been refined over decades of industry experience. For those interested in mastering testing techniques, consider exploring the art of splicing and testing techniques for enhanced durability.
- Testing Machine Configuration: Tests utilize specialized tensile testing machines equipped with large-diameter capstans that prevent localized stress points during testing.
- Pre-Test Conditioning: Samples undergo careful preparation, including proper spooling and pre-tensioning to ensure consistent results.
- Rate of Loading: Breaking strength tests follow specific loading rates to account for polyamide's unique elongation properties.
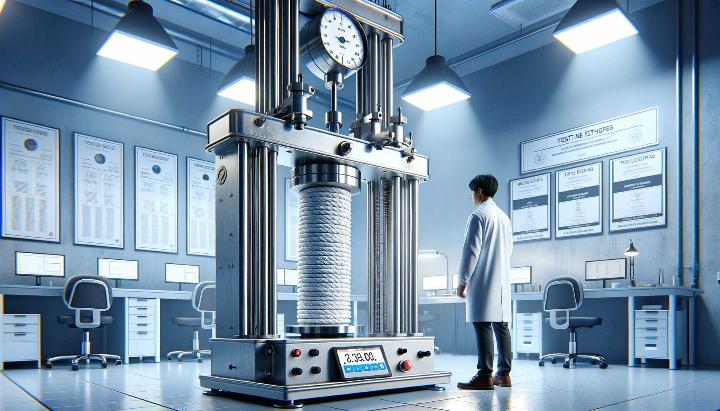
Wet vs Dry Testing Requirements
One aspect that often surprises newcomers to polyamide rope testing is the importance of wet testing. Due to polyamide's unique interaction with moisture, comprehensive testing must include both wet and dry conditions.
- Wet Testing Protocol: Ropes are soaked for a minimum of 24 hours before testing, simulating real-world marine conditions.
- Strength Variations: Wet polyamide typically shows a 10-20% reduction in breaking strength compared to dry conditions.
- Temperature Control: Testing environments maintain strict temperature controls to ensure consistent results.
Breaking Strength Calculation and Measurement
The calculation of breaking strength follows specific formulas based on rope diameter and construction. For standard polyamide ropes, the basic calculation uses the diameter squared divided by 200, though this varies with construction methods and intended use.
Industry Standard Note
All testing procedures must comply with ISO 2307 standards for rope testing, ensuring results are internationally recognized and comparable.
Remember, these tests aren't just about numbers - they're about ensuring safety and reliability in real-world applications. Whether you're manufacturing ropes for marine use or selecting them for critical operations, understanding these testing procedures helps ensure you're making informed decisions based on reliable data.
```htmlUnderstanding the unique characteristics of polyamide ropes is crucial for their application across various industries. These ropes boast impressive durability, abrasion resistance, and a superior strength-to-weight ratio, making them ideal for everything from climbing to marine applications. The polyamide rope breaking strength is influenced by factors such as the rope's diameter, construction, and environmental conditions. Accurate testing methods are essential to assess this strength, ensuring compliance with industry standards for safety and performance. By exploring these aspects, we gain invaluable insights into selecting the right rope for specific needs.
Inquire About Tailored Rope Solutions
Above, you'll find our inquiry form. Fill it in to discover how our expertise in polyamide ropes can address your unique requirements while ensuring optimal strength and durability in your applications.
```