Have you ever wondered why some rigging operations go smoothly while others end in disaster? The secret lies in understanding choker sling capacity and wire rope sizes. As a leading rope manufacturer, we've seen firsthand how this knowledge can make or break a lift.
Imagine a scenario where a heavy load suddenly slips, endangering workers and damaging expensive equipment. This nightmare can become reality when riggers underestimate the importance of choker sling capacity and wire rope sizes. But it doesn't have to be this way.
In this comprehensive guide, we'll demystify the world of choker sling capacity, steel choker rigging, and wire rope sling size and capacity. We'll explore everything from the factors influencing sling capacity to the intricacies of rigging rope materials and construction. Did you know that rigging rope is often made of a blend of materials like polypropylene-polyester, nylon-polyester, and polyester-polyester, and can be either single braid or double braid?
Whether you're a seasoned rigger or new to the field, this blog post will equip you with the knowledge to make informed decisions, enhance safety, and optimise your rigging operations. So, let's dive in and unravel the complexities of choker slings and wire ropes – your next successful lift depends on it!
Understanding Choker Sling Capacity
When it comes to rigging operations, understanding choker sling capacity is crucial for ensuring safety and efficiency. As a rigger with over a decade of experience, I've seen firsthand how proper knowledge of choker slings can make or break a lift. Let's dive into the factors that influence choker sling capacity and how to calculate it accurately.
Factors Affecting Choker Hitch Capacity
Several key factors play a role in determining the capacity of a choker hitch:
- Choke angle: This is perhaps the most critical factor. A choke angle of 120 degrees or greater is ideal, as it maximizes the sling's capacity.
- Sling material: Different materials, such as wire rope or synthetic fibers, have varying strengths and capacities.
- Load positioning: The way the load is positioned can affect the stress on the sling and its overall capacity.
It's worth noting that a choker hitch typically has a capacity ranging from 75-80% of a single leg sling capacity. However, this can vary depending on the specific configuration and conditions.
Did you know? The choker hitch capacity can range from 40% to 80% of the single leg capacity, depending on the choke angle and other factors. Always consult manufacturer specifications for accurate information.
Calculating Choker Sling Load Limits
Calculating the load limit for a choker sling involves considering multiple factors. Here's a step-by-step guide to help you determine the working load limit (WLL) of your choker sling:
- Determine the single leg capacity of your sling from the manufacturer's specifications.
- Measure the choke angle of your setup.
- Apply the appropriate reduction factor based on the choke angle.
- Consider any additional factors such as environmental conditions or load dynamics.
For example, let's say we have a wire rope sling with a single leg capacity of 1000 kg, and we're using it in a choker hitch with a 120-degree choke angle. The capacity would be approximately 750-800 kg (75-80% of the single leg capacity).
Remember, these calculations are just guidelines. Always err on the side of caution and consult with a qualified rigger or engineer for complex lifts. Your safety and the integrity of your equipment should always be the top priority.
Safety First!
Never exceed the working load limit of your choker sling. When in doubt, always choose a higher-rated sling.
Understanding choker sling capacity is essential for safe and efficient rigging operations. By considering factors like choke angle, sling material, and load positioning, you can ensure that your lifts are performed safely and effectively. Always adhere to manufacturer specifications and industry standards, and don't hesitate to seek expert advice when needed. Your commitment to understanding these principles will contribute to a safer work environment for everyone involved in rigging operations.
Exploring Steel Choker Rigging: Applications and Benefits
As a seasoned rigger, I've come to appreciate the versatility and strength of steel choker rigging in countless industrial lifting scenarios. Steel choker rigging is a robust and reliable method that uses wire rope slings to secure and lift loads in a choking configuration. This technique is particularly useful when dealing with oddly shaped or bulky items that lack convenient attachment points.
Types of Wire Rope Slings for Choker Rigging
When it comes to wire rope slings for choker applications, there's no one-size-fits-all solution. The choice of sling depends on various factors, including the load's weight, shape, and the lifting environment. Let's explore some common types:
- Single-part wire rope slings: These are versatile and suitable for general-purpose lifting. They're my go-to choice for straightforward lifts.
- 6x19 and 6x37 wire rope constructions: These offer a balance between flexibility and strength, making them ideal for most choker applications.
- Flemish eye slings: These feature a spliced eye that provides excellent strength and durability, perfect for heavy-duty choker rigging tasks.
One game-changing innovation I've embraced in recent years is the sliding choker hook. These nifty devices allow for quick adjustments and enhanced versatility, significantly speeding up rigging operations without compromising safety.
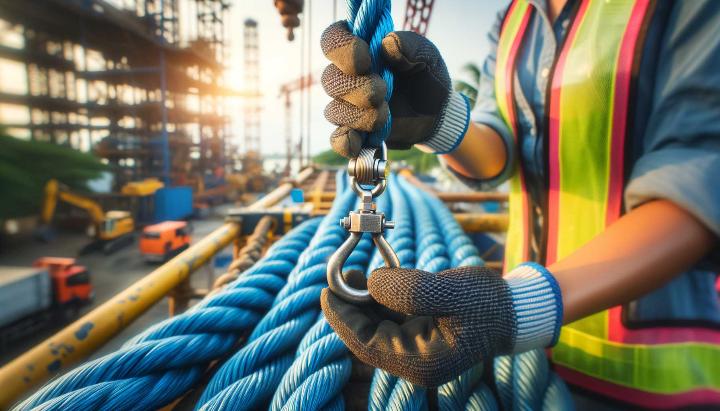
Safety Considerations for Steel Choker Rigging
Safety should always be your top priority when working with steel choker rigging. Here are some crucial points to keep in mind:
- Regular inspections are non-negotiable: Before each use, carefully examine your wire rope slings for signs of wear, kinks, or broken wires. If you spot any damage, retire the sling immediately.
- Mind the D/d ratio: This crucial factor refers to the diameter of the object being lifted (D) compared to the diameter of the wire rope (d). A larger D/d ratio reduces stress on the rope and increases the sling's capacity.
- Protect against sharp edges: Always use softeners or edge protectors when choking around sharp corners to prevent damage to the wire rope.
I once witnessed a near-miss incident where a rigger overlooked a small nick in a wire rope sling. Thankfully, a last-minute inspection caught it before the lift began. This experience hammered home the importance of thorough checks and never cutting corners when it comes to safety.
Remember: The working load limit (WLL) of a wire rope sling in a choker hitch is typically 75-80% of its straight vertical capacity. Always consult manufacturer guidelines and never exceed the rated WLL.
In conclusion, steel choker rigging is an indispensable technique in the world of industrial lifting. By understanding the different types of wire rope slings available, adhering to safety guidelines, and staying vigilant during inspections, you can harness the full potential of this versatile rigging method. Have you encountered any challenging lifts where steel choker rigging saved the day? I'd love to hear your experiences in the comments below!
Wire Rope Sling Size and Capacity Guide
As a rigging specialist with years of hands-on experience, I've come to appreciate the critical importance of understanding wire rope sling sizes and capacities. It's not just about choosing the right tool for the job; it's about ensuring the safety of every worker on site and protecting valuable cargo. Let's dive into the nitty-gritty of wire rope slings and unravel the mysteries of their specifications and capacities.
Understanding Wire Rope Sling Specifications
When I first started in this industry, the array of wire rope sling specifications seemed daunting. But trust me, once you grasp the basics, it all starts to make sense. Here are the key terms you need to know:
- Diameter: This is the thickness of the wire rope, typically ranging from a hair-thin 1/32" to a beefy 4-1/2". The diameter plays a crucial role in determining the sling's strength.
- Length: Measured from eye to eye, the length affects how the sling interacts with the load and rigging points.
- Construction: This refers to how the wire rope is made. Common types include 6x19 and 6x37, where the first number indicates the number of strands and the second, the number of wires per strand.
These specifications aren't just numbers on a label; they directly impact the sling's strength, flexibility, and suitability for different tasks. For instance, a 6x37 construction offers more flexibility than a 6x19, making it ideal for wrapping around irregularly shaped loads.
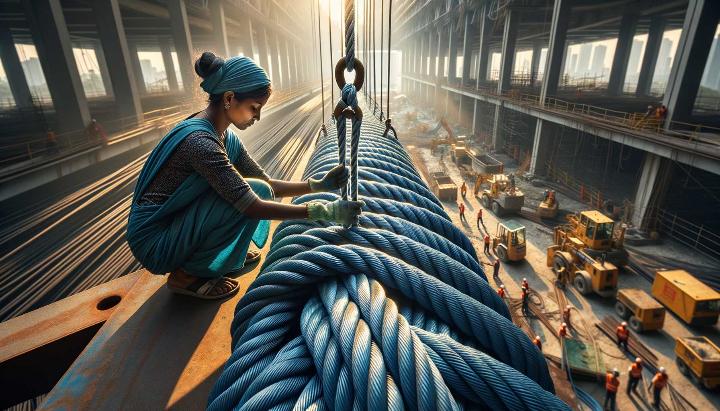
To give you a quick reference, here's a simplified table comparing common wire rope sling sizes and their general capacities:
Diameter | Vertical Capacity (tons) | Choker Capacity (tons) |
---|---|---|
3/8" | 2.8 | 2.1 |
1/2" | 4.9 | 3.7 |
5/8" | 7.6 | 5.7 |
Remember, these are general capacities. Always refer to the manufacturer's specifications for precise ratings.
Calculating Wire Rope Sling Capacity
Now, let's talk about the factors that affect sling capacity. It's not just about the wire rope itself; how you use it matters too. Here are the key considerations:
- Sling angle: The angle at which the sling is used can dramatically affect its capacity. A 60-degree angle reduces the capacity by 13%, while a 45-degree angle cuts it by 29%.
- Number of legs: Using multiple sling legs can increase capacity, but not always linearly. Two legs at a 60-degree angle provide about 1.73 times the capacity of a single vertical leg.
- Environmental factors: Extreme temperatures, chemicals, or abrasive conditions can all impact a sling's performance.
To calculate the capacity, start with the sling's rated capacity for a straight vertical lift, then apply the appropriate reduction factors for your specific configuration. Here's a simple formula to get you started:
Adjusted Capacity = Rated Vertical Capacity x Angle Factor x Number of Legs Factor
For example, let's say you're using a 1/2" wire rope sling with a vertical capacity of 4.9 tons in a choker hitch at a 60-degree angle. The calculation would look like this:
4.9 tons x 0.75 (choker factor) x 0.87 (60-degree angle factor) = 3.2 tons
Always consult the manufacturer's guidelines and OSHA standards for accurate capacity ratings and usage instructions. The safety of your team and your load depends on it!
Understanding wire rope sling sizes and capacities is crucial for safe and efficient rigging operations. By mastering these concepts, you'll be well-equipped to select the right sling for any job. Remember, when in doubt, always err on the side of caution and consult with a rigging expert. Have you encountered any challenging situations where understanding sling capacities made all the difference? Share your experiences in the comments below!
Rigging Rope Materials and Construction
As a seasoned rigger, I've learned that choosing the right rigging rope can make or break a job. The materials and construction of your rope are crucial factors that directly impact its performance, safety, and longevity. Let's dive into the world of rigging ropes and unravel the mysteries behind their composition and structure.
Types of Fibers Used in Rigging Ropes
When I first started in this industry, natural fibers like manila and hemp were the go-to materials for rigging ropes. While these traditional options still have their place, synthetic fibers have revolutionized the field. Here's a breakdown of the most common materials you'll encounter:
- Natural fibers: Manila and hemp offer good grip and are biodegradable, but they're less durable and more susceptible to rot.
- Nylon: Known for its exceptional strength and elasticity, nylon is a workhorse in wet conditions. Learn more about nylon core rope features.
- Polyester: This fiber shines in its resistance to UV damage and chemicals, maintaining its strength even when wet.
- Polypropylene: Lightweight and floatable, it's perfect for marine applications but can be slippery when wet.
In my experience, the blend of materials can significantly affect a rope's performance. For instance, I once used a polypropylene-polyester blend rope for a delicate lift in a damp environment. The rope's balanced properties of strength and water resistance made the operation smooth and safe.
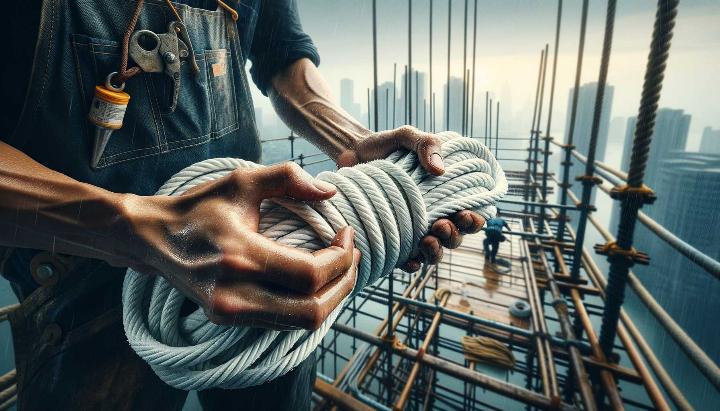
Rope Construction Techniques for Rigging
The way a rope is constructed is just as important as the materials used. Let's explore the main construction techniques:
- 3-strand twisted: This classic design offers good handling and is easy to splice, but it can untwist under load.
- 12-strand braided: Provides a balance of strength and flexibility, making it ideal for diverse rigging applications.
- Double braid: Consists of a braided core inside a braided cover, offering superior strength and reduced stretch. Discover more about double braided nylon rope for offroad and marine.
I remember a particularly challenging tree removal job where we used a 12-strand braided bull rope. Its combination of strength and flexibility allowed us to navigate tight spaces without compromising on safety. It's moments like these that highlight the importance of choosing the right rope construction for the task at hand.
Did you know? Bull ropes, specifically designed for heavy-duty rigging and tree work, often feature a 12-strand or double braid construction for maximum strength and durability. Explore more about arbortist bull ropes.
When selecting a rigging rope, consider the specific demands of your job. Are you working in a high-abrasion environment? A double braid construction might be your best bet. Need maximum flexibility for intricate rigging setups? A 12-strand braided rope could be the answer.
Remember, the right combination of materials and construction can significantly enhance your rigging operations' safety and efficiency. What's your go-to rope for challenging rigging tasks? Share your experiences in the comments below – I'd love to hear about the rope choices that have made a difference in your work!
Understanding choker sling capacity, steel choker rigging, and wire rope sling size and capacity is pivotal for safe and efficient rigging operations. Key factors like choke angle, sling material, and load positioning determine choker sling capacity, essential for accurate lifting. Steel choker rigging offers unparalleled advantages across applications, requiring diligent maintenance and inspection. Selecting the right wire rope sling size involves understanding diameter, length, and construction types, ensuring accurate working load limit (WLL) calculations. Additionally, rigging ropes, often crafted from blends such as polypropylene-polyester, nylon-polyester, and polyester-polyester, and available in single or double braid constructions, affect overall rigging efficacy. Proper selection, usage, and adherence to industry standards ensure robust and secure rigging operations.