Imagine a world where your industrial wire rope sheave systems are virtually immune to wear and tear, operating smoothly day in and day out without frequent replacements. Sound too good to be true? Enter Dyneema sleeves—the revolutionary material transforming the performance of wire rope sheaves, rope sheaves, and cable sheave systems across industries.
Dyneema, known for its exceptional strength and durability, offers an unparalleled solution to the common challenges faced by wire rope sheaves in industrial settings. Whether you're dealing with heavy lifting, marine operations, or mining machinery, these robust sleeves deliver enhanced performance, reduced friction, and increased lifespan. But how exactly do they achieve this, and why should you care?
In this post, we'll explore the ins and outs of wire rope sheaves, the transformative benefits of integrating Dyneema sleeves, and actionable insights on implementing and maintaining these innovative solutions in your operations. Stay with us to discover how upgrading to Dyneema-sleeved wire rope sheaves can revolutionise your industrial applications, offering enhanced efficiency, reliability, and safety.
Understanding Wire Rope Sheaves
Wire rope sheaves are essential components in many industrial applications involving heavy lifting, hoisting, and rigging. They serve as grooved wheels that guide wire ropes and allow for a change in the direction of forces applied to the ropes. Proper selection and design of sheaves play a crucial role in ensuring optimal wire rope performance and maximizing service life.
Function and Purpose of Sheaves
The primary function of sheaves is to act as grooved wheels that facilitate the smooth movement and redirection of wire ropes. They are commonly used in systems such as cranes, hoists, and rigging setups where ropes need to be guided around pulleys or changed in direction. Sheaves essentially support the wire rope, allowing it to bend and move freely while minimizing excessive wear and tear.
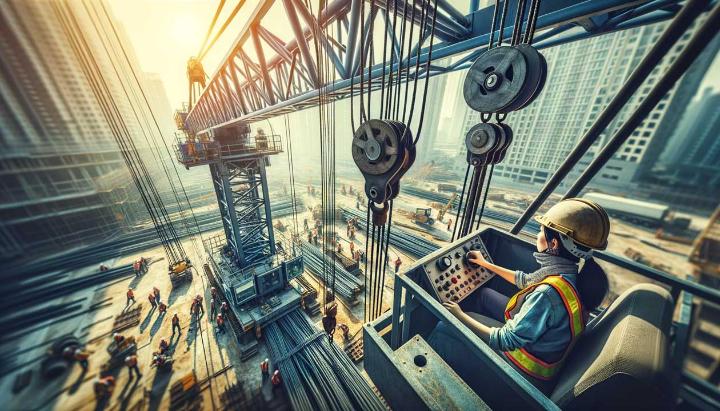
There are different types of sheaves, including fixed sheaves, traveling sheaves, and equalizer sheaves, each designed for specific applications and load requirements.
Proper Sheave Sizing and Groove Design
Selecting the correct sheave size is crucial for optimal wire rope performance and longevity. The sheave diameter should be proportional to the wire rope diameter, and industry guidelines typically recommend a sheave-to-rope diameter ratio between 18:1 and 30:1. Utilizing sheaves with smaller diameters can lead to excessive bending stress on the wire rope, resulting in deformation, pinching, or accelerated wear.
In addition to size, the design of the sheave groove plays a vital role. The groove should be slightly larger than the wire rope diameter, allowing for proper seating and avoiding pinching or crushing. Factors like groove depth, contour, and finish can significantly impact wire rope bending fatigue and overall service life.
Impact of Sheaves on Wire Rope Performance
The selection and condition of sheaves can have a profound impact on the performance and lifespan of wire ropes. Improper sheave sizing or groove design can lead to premature wire rope failure due to excessive bending stress, localized wear, or deformation.
Worn or misaligned sheaves can also contribute to wire rope degradation. Sheave wear can cause uneven grooves, resulting in increased friction and accelerated rope wear. Misaligned sheaves can create uneven loading on the wire rope, leading to uneven wear patterns and potential failure points.
Regular sheave inspection and maintenance are essential to ensure optimal wire rope performance and safety. Sheaves should be checked for wear, proper alignment, and correct groove dimensions to mitigate potential issues and maximize the service life of the wire rope system.
Benefits of Using Dyneema Sleeves on Wire Rope Sheaves
Dyneema sleeves, also known as chafe protection sleeves, are designed to safeguard wire rope sheaves from the damaging effects of abrasion and wear. These sleeves are made from Dyneema, a high-performance polyethylene fiber that boasts exceptional strength and durability while remaining lightweight.
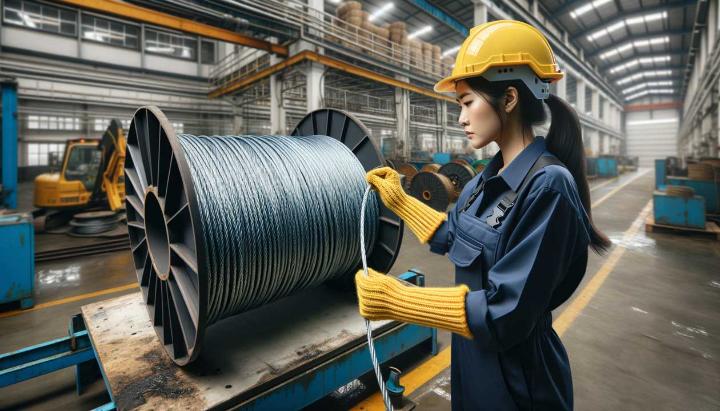
By incorporating Dyneema sleeves into your wire rope sheave systems, you can unlock a range of benefits that enhance performance, safety, and longevity.
Increased Durability and Longevity
One of the most significant advantages of using Dyneema sleeves is their ability to extend the lifespan of wire rope sheaves. These sleeves act as a protective barrier, shielding the sheaves from the abrasive forces encountered during operation. Their exceptional abrasion resistance ensures that the sheave grooves remain intact, minimizing the risk of premature wear and tear.
In industries where equipment downtime can be costly, the durability of Dyneema-sleeved wire rope sheaves can translate into substantial cost savings. By reducing the need for frequent replacements, businesses can maximize their return on investment and minimize operational disruptions.
Enhanced Safety and Reliability
Safety should be a top priority in any industrial setting, and Dyneema sleeves play a crucial role in mitigating potential risks. Wire rope failure can have severe consequences, leading to accidents, injuries, and costly damages. By safeguarding the wire rope and sheaves with Dyneema's robust protection, you can minimize the likelihood of such failures, ensuring a safer working environment for your team.
The high strength-to-weight ratio of Dyneema makes it an ideal material for demanding applications. Its durability and resistance to wear and tear contribute to the overall reliability of the wire rope sheave system, reducing the chances of unexpected breakdowns or failures.
Improved Efficiency and Productivity
In addition to enhanced safety and longevity, Dyneema sleeves can also boost the efficiency and productivity of your operations. With reduced friction between the wire rope and sheave, the system operates more smoothly, minimizing energy losses and maximizing power transmission.
Furthermore, the extended service life of Dyneema-sleeved wire rope sheaves translates into fewer maintenance requirements and longer intervals between replacements. This reduction in downtime means your operations can run more consistently, leading to increased productivity and efficiency.
Have you experienced the benefits of Dyneema sleeves firsthand? Share your story with us! We'd love to hear how these innovative sleeves have impacted your wire rope sheave systems and operations. You can also explore more benefits of Dyneema tow ropes and their applications.
Applications of Dyneema-sleeved Wire Rope Sheaves
Dyneema-sleeved wire rope sheaves are a game-changer in industries where strength, durability, and reliable performance are paramount. By combining the ruggedness of steel wire ropes with the exceptional abrasion resistance and lightweight properties of Dyneema fibers, these innovative sheaves offer a unique solution that outperforms traditional alternatives.
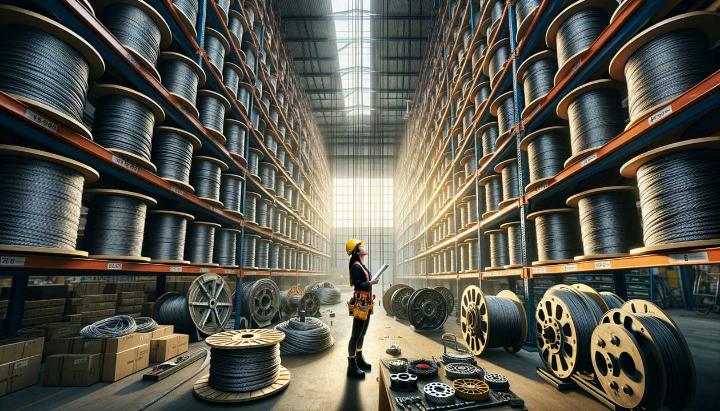
While the benefits of Dyneema-sleeved sheaves are far-reaching, some industries have embraced these innovative components with open arms, recognizing their potential to enhance safety, productivity, and bottom lines.
Benefits of Dyneema-sleeved Sheaves in Various Industries
- Crane Applications: In the construction and mining industries, where heavy loads and harsh conditions are the norm, Dyneema-sleeved sheaves offer improved lifting capacity, reduced weight, and increased reliability. Their exceptional durability ensures that critical operations can proceed without interruptions due to sheave failures or unplanned downtime.
- Maritime and Offshore: The marine environment presents unique challenges, with saltwater and corrosive conditions putting immense stress on equipment. Dyneema-sleeved sheaves are resistant to these harsh conditions, ensuring smooth and safe operations for tasks like mooring, towing, and rigging on offshore platforms and ships.
- Arborist and Heavy-Duty Lifting: In the tree care and heavy-duty lifting industries, where safety is paramount, Dyneema-sleeved sheaves provide unparalleled abrasion resistance and durability. These qualities make them ideal for rigging, load lifting, and cable support systems, reducing the risk of equipment failure and ensuring the safe completion of tasks.
Common Applications of Dyneema-sleeved Wire Rope Sheaves
The versatility of Dyneema-sleeved wire rope sheaves has led to their widespread adoption across various industries. Here are some common applications where these innovative components shine:
- Crane Operations: Dyneema-sleeved sheaves are commonly used in construction cranes, mining equipment, and offshore platform cranes, where they excel in demanding environments and heavy-duty lifting tasks.
- Maritime and Offshore: These sheaves are essential components in mooring lines, towing systems, and rigging setups on ships, offshore platforms, and marine vessels, providing reliable performance in harsh saltwater conditions.
- Arborist and Tree Care: In the arborist industry, Dyneema-sleeved sheaves are employed in rigging systems, load lifting applications, and cable support systems, ensuring safe and efficient tree care operations.
- Heavy-Duty Lifting and Material Handling: Overhead cranes, lifting slings, hoists, and other heavy-duty lifting equipment rely on Dyneema-sleeved sheaves for their exceptional strength, abrasion resistance, and long service life.
Real-world examples of Dyneema-sleeved sheave applications can be found in various industries worldwide. For instance, a leading offshore oil and gas company reported a significant reduction in sheave replacements and downtime after implementing Dyneema-sleeved sheaves on their platform cranes. Similarly, a major construction firm experienced improved efficiency and safety on their job sites by upgrading their crane sheaves to the Dyneema-sleeved variety. For more insights on rope applications, check out the essential market applications for cable sling and rope sling.
As industries continue to push the boundaries of performance and safety, Dyneema-sleeved wire rope sheaves emerge as a reliable and innovative solution, offering a powerful combination of strength, durability, and efficiency for demanding applications.
Upgrading Wire Rope Sheaves with Dyneema Sleeves
In the rugged world of industrial operations, where strength and durability are paramount, upgrading wire rope sheaves with Dyneema sleeves can be a game-changer. These innovative sleeves, crafted from the high-performance Dyneema fiber, offer a potent combination of exceptional abrasion resistance, lightweight construction, and unparalleled strength.
Can you imagine the peace of mind that comes with knowing your critical rigging systems are safeguarded against the relentless wear and tear of daily operations? With Dyneema sleeves, you can wave goodbye to premature sheave replacements and costly downtime, elevating your operational efficiency to new heights.
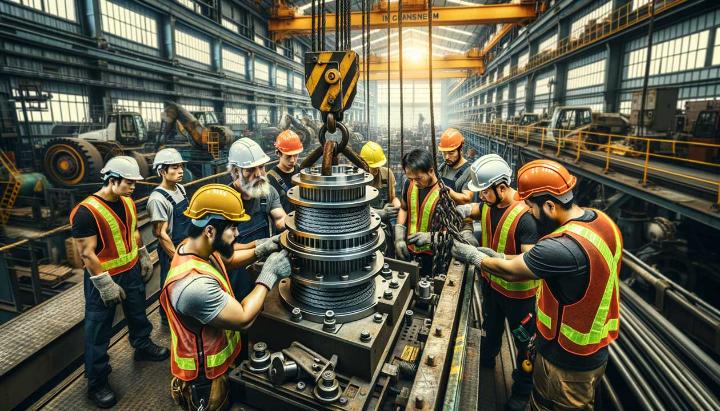
Benefits of Using Dyneema Sleeves
- Unparalleled Abrasion Resistance: Dyneema's exceptional strength and resilience make it the perfect material to shield your wire ropes from the relentless abrasion encountered in industrial settings. These sleeves act as a robust barrier, safeguarding the sheave grooves and preventing premature wear, ensuring your rigging systems continue to operate at peak performance.
- Extended Lifespan: By minimizing the friction and wear on your wire ropes, Dyneema sleeves significantly prolong the lifespan of your sheaves. Say goodbye to frequent replacements and embrace the cost savings that come with investing in components that stand the test of time.
- Improved Efficiency: The lightweight and low-stretch nature of Dyneema fibers translates into smoother operations and reduced energy losses. With Dyneema sleeves, your rigging systems can operate at optimal efficiency, maximizing power transmission and minimizing downtime.
Step-by-Step Guide to Installing Dyneema Sleeves
While the benefits of Dyneema sleeves are undeniable, proper installation is crucial to ensure you reap their full potential. Follow this step-by-step guide, and you'll be well on your way to fortifying your wire rope sheaves with unparalleled protection.
- Measure and Cut: Carefully measure the length of the sheave groove to determine the required length of the Dyneema sleeve. Cut the sleeve to size, ensuring a snug fit around the sheave.
- Prepare the Surface: Thoroughly clean the sheave groove, removing any debris or contaminants that could interfere with the sleeve's adhesion.
- Apply Adhesive: Following the manufacturer's instructions, apply a thin, even layer of the recommended adhesive to the sheave groove and the inner surface of the Dyneema sleeve.
- Install the Sleeve: Carefully position the sleeve over the sheave groove, ensuring a tight fit and maintaining proper alignment. Apply gentle pressure to ensure complete adhesion.
- Secure the Ends: Once the sleeve is in place, use the recommended method (e.g., cable ties, clamps) to securely fasten the ends, preventing the sleeve from slipping or shifting during operation.
Upgrading to Dyneema sleeves is an investment in the longevity and reliability of your operations.
By following these steps meticulously, you'll unlock the full potential of Dyneema sleeves, ensuring your wire rope sheaves are fortified against the relentless forces of abrasion and wear. Remember, proper installation is key to maximizing the benefits of these innovative sleeves, so take the time to do it right. Explore how Dyneema fibers compare to other materials in our article about Dyneema fibers vs. natural rope fibers.
Are you ready to join the ranks of industries that have embraced the power of Dyneema sleeves? Upgrade your wire rope sheaves today and experience the peace of mind that comes with knowing your critical rigging systems are safeguarded against the harshest conditions, ensuring smooth operations and minimizing costly downtime.
Unlock the Benefits of Dyneema Sleeves for Wire Rope Sheaves
Industries involved in heavy lifting and hoisting understand the critical role that wire rope sheaves play in operations. By incorporating Dyneema sleeves, these essential components experience reduced friction, enhanced durability, and increased service life, resulting in greater efficiency and safety. Whether it's a cable sheave in a construction crane or a rope sheave in maritime applications, upgrading with Dyneema sleeves ensures your systems operate smoothly and cost-effectively. Explore how Dyneema protects your wire rope sheave systems and consider making the upgrade today. Fill out the form above to learn more about how Dyneema sleeves can benefit your operations.