In the ever-evolving world of ropes and cables, two materials have long stood out as the go-to choices for a wide range of applications: synthetic rope and steel wire. From securing boats to hoisting heavy loads, these versatile materials have played a pivotal role in shaping our modern world. However, with advancements in technology and changing industry demands, the debate over which material reigns supreme has only intensified.
As you embark on this exploration of synthetic rope vs steel wire, brace yourself for an enlightening journey into the realm of wire cable clamps, cable clamps for wire rope, and the ever-versatile steel wire clamps. Whether you're a seasoned professional or a curious enthusiast, understanding the nuances of these materials is essential for making informed decisions that strike the perfect balance between performance, safety, and cost-effectiveness.
Imagine holding a synthetic rope in your hands, marveling at its lightweight yet incredibly strong composition. Now, picture the robust steel wire, a testament to unwavering strength and durability. Each material boasts its own unique advantages, from corrosion resistance to versatility in harsh environments. As you delve deeper into this comprehensive exploration, you'll uncover the key differences that set these materials apart, empowering you to choose the right solution for your specific needs.
So, buckle up and get ready to dive into the captivating world of synthetic rope and steel wire. Whether you're seeking the perfect mooring line for your yacht, the ideal rigging solution for a construction site, or the ultimate climbing rope for your next adventure, this blog post will equip you with the knowledge to make confident and informed decisions. Embrace the journey, and let the battle between synthetic rope and steel wire begin!
Comparing Material Properties: Synthetic Rope vs. Steel Wire
When it comes to choosing between synthetic rope and steel wire for your specific application, it's crucial to understand their key material properties. Let's dive into a detailed comparison of strength, weight, flexibility, and corrosion resistance to help you make an informed decision.
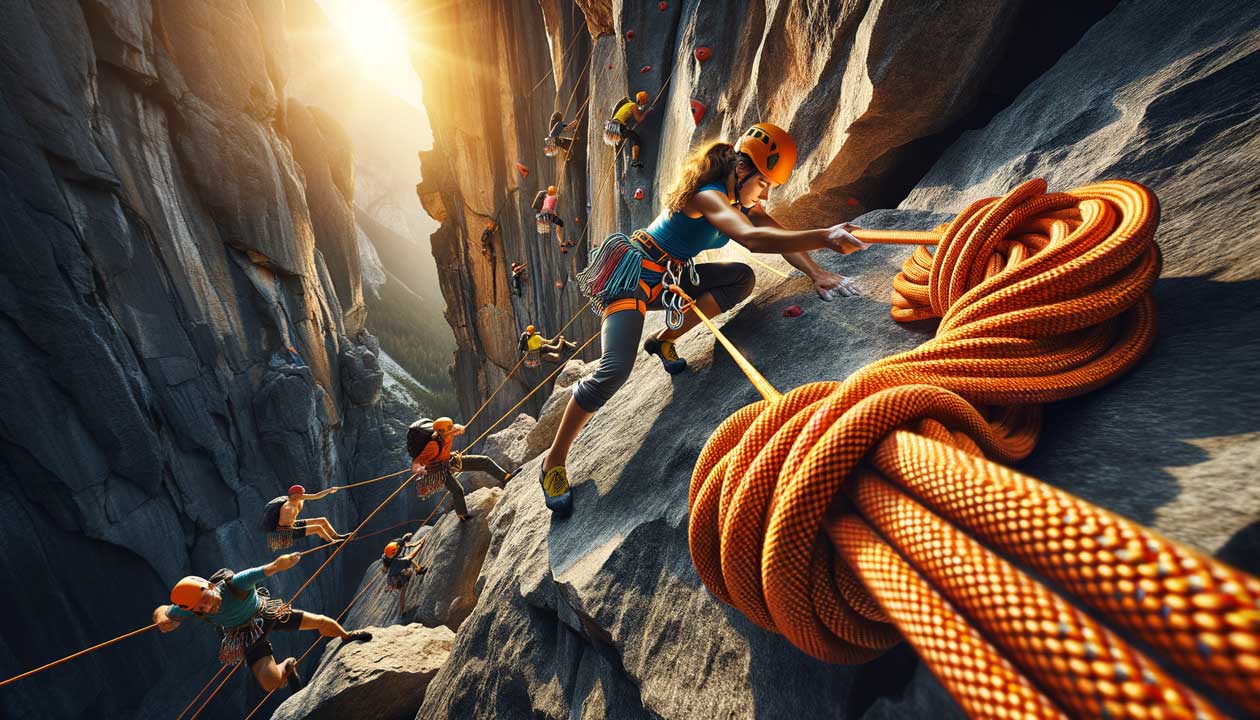
Strength and Durability: Breaking Strengths Compared
One of the most important factors to consider when selecting a rope or wire is its breaking strength. Breaking strength refers to the maximum load a rope or wire can withstand before it fails. Synthetic ropes, particularly those made from high-modulus polyethylene (HMPE) fibers, offer exceptional breaking strengths compared to steel wire ropes of the same weight.
For example, a 12-strand braided HMPE rope with a diameter of 12mm can have a breaking strength of around 200kN, while a steel wire rope of the same diameter might have a breaking strength of only 150kN. This means that synthetic ropes can provide superior strength-to-weight ratios, allowing for lighter and more efficient designs in various applications.
Weight and Flexibility: Lightweight Advantages
Another significant advantage of synthetic ropes over steel wire ropes is their lightweight nature. Synthetic fibers like polyethylene and HMPE have much lower densities compared to steel, resulting in ropes that are significantly lighter. This weight reduction offers several benefits, including:
- Ease of handling and transportation, as lighter ropes are easier to move, deploy, and store.
- Reduced strain on equipment and structures, as lighter ropes exert less force on attachment points and winches.
- Improved flexibility and kink resistance, allowing for tighter bends and more compact coiling without damaging the rope.
The lightweight and flexible nature of synthetic ropes make them ideal for applications where weight savings and maneuverability are crucial, such as in the marine industry, construction, and recreational activities.
Corrosion and Chemical Resistance
Corrosion and chemical resistance are other areas where synthetic ropes excel compared to steel wire ropes. Steel wire ropes are susceptible to rust and corrosion, especially when exposed to moisture, salt water, or corrosive chemicals. This corrosion can weaken the wire rope over time, leading to premature failure and potential safety hazards.
In contrast, synthetic ropes made from materials like polyethylene and HMPE are inherently resistant to corrosion and chemical absorption. They do not rust or degrade when exposed to water, salt, or most chemicals, making them suitable for use in harsh environments such as marine and offshore applications. Some synthetic ropes even feature UV-resistant coatings or treatments to enhance their durability and longevity in outdoor settings.
When corrosion resistance and chemical compatibility are top priorities, synthetic ropes offer a clear advantage over steel wire ropes. They maintain their strength and integrity even in the presence of corrosive elements, ensuring reliable performance and extended service life.
Advantages of Synthetic Rope Over Steel Wire
When it comes to selecting the best material for your specific application, whether it's winching, towing, or lifting, understanding the advantages of synthetic rope over traditional steel wire is crucial. Let's explore how synthetic rope's lightweight design, flexibility, and safety features make it a superior choice in many situations.
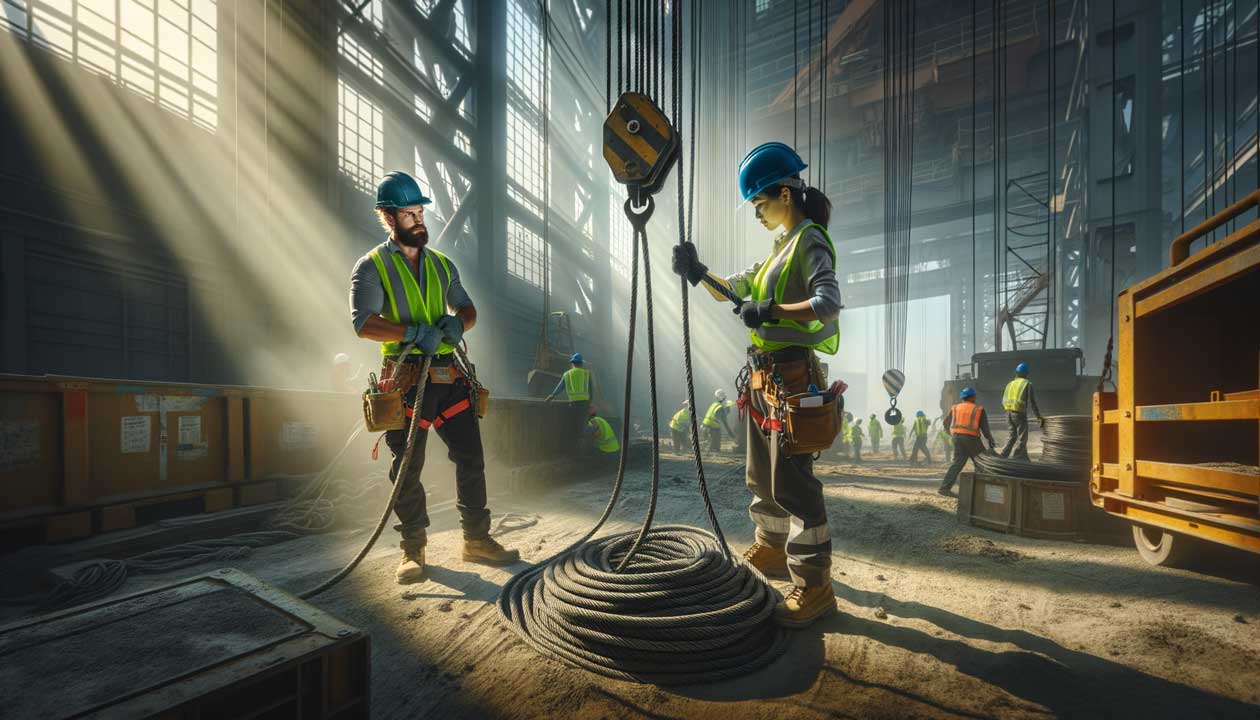
Lightweight and Flexible Design
One of the most significant advantages of synthetic rope is its lightweight construction compared to steel wire of the same diameter. Synthetic fibers like HMPE and polyethylene have a much lower density than steel, resulting in ropes that are up to seven times lighter. This lightweight design offers several benefits:
- Ease of handling and transportation: Lighter ropes are much easier to move, deploy, and store, especially in situations where weight is a concern, such as in marine or off-road applications.
- Reduced strain on equipment and structures: Lightweight ropes exert less force on attachment points, winches, and other equipment, minimizing wear and tear and extending their lifespan.
- Increased flexibility and kink resistance: Synthetic ropes are more flexible than steel wire, allowing for tighter bends and more compact coiling without the risk of kinking or damaging the rope.
The combination of lightweight and flexible design makes synthetic rope an ideal choice for applications where weight savings and maneuverability are paramount, such as in marine environments, off-road recovery, and rescue operations. Imagine being able to easily carry and deploy a rope that's strong enough to tow a vehicle or moor a boat, without the heavy, cumbersome nature of steel wire.
Safer Handling and Reduced Injury Risk
In addition to its lightweight and flexible design, synthetic rope offers significant safety advantages over steel wire. Have you ever experienced the pain of a cut or abrasion from handling steel wire with sharp burrs or rough edges? With synthetic rope, that risk is virtually eliminated. Here's how synthetic rope promotes safer handling:
- No sharp edges or burrs: Synthetic rope maintains a smooth surface throughout its lifespan, eliminating the risk of cuts or abrasions during handling.
- Rust and corrosion resistance: Unlike steel wire, synthetic rope does not rust or corrode, ensuring longer-lasting performance and reduced maintenance requirements.
- Lower potential energy under load: Synthetic rope stores less potential energy when under load compared to steel wire, reducing the risk of whiplash or kickback in case of failure.
The safety benefits of synthetic rope extend beyond just handling. In various applications, from marine to industrial use, the reduced risk of injury and accidents can have a significant impact on overall safety and productivity. By choosing synthetic rope, you're not only investing in a high-performance material but also in the well-being of those who use it.
Whether you're a professional in the marine industry, an off-road enthusiast, or simply looking for a safer and more efficient alternative to steel wire, synthetic rope offers a range of advantages that make it a smart choice. Its lightweight and flexible design, combined with its superior safety features, make it a versatile solution for a wide range of applications. So, the next time you're considering an upgrade from steel wire, remember the many benefits that synthetic rope has to offer.
Applications and Markets of Synthetic Ropes
Discover the versatile world of synthetic ropes and their wide-ranging applications across industries.
Have you ever wondered about the countless ways synthetic ropes are used in our modern world? From the depths of the ocean to the heights of towering cranes, these incredible materials have revolutionized industries and opened up new possibilities. In this section, we'll explore the diverse applications and markets where synthetic ropes truly shine.
Marine and Coastal Applications
Picture yourself on a boat, surrounded by the vast expanse of the sea. The ropes you rely on to secure your vessel, tow water skiers, or even moor at the dock are likely made of synthetic materials. Synthetic ropes, particularly those made from high-modulus polyethylene (HMPE) fibers, have become the go-to choice for marine environments due to their unparalleled properties:
- Resistance to water, salt, and UV damage, ensuring long-lasting performance in harsh coastal conditions.
- Lightweight yet incredibly strong, making them easier to handle and less taxing on boat equipment.
- Excellent abrasion resistance, withstanding the constant friction of rubbing against surfaces or other lines.
From small sailboats to massive ships and offshore platforms, synthetic ropes have become indispensable in the marine industry. Their durability and reliability provide peace of mind to boaters, knowing their lines will hold strong against the elements.
Construction and Industrial Applications
Imagine the intricate dance of a construction site, with towering cranes lifting heavy loads and workers navigating scaffolding high above the ground. Synthetic ropes play a crucial role in ensuring safety and efficiency in these demanding environments. Here's why they've become the preferred choice:
- High strength-to-weight ratio, allowing for lifting heavier loads with smaller, more manageable ropes.
- Durability and abrasion resistance, withstanding the constant wear and tear of rugged job sites.
- Flexibility and easy handling, enabling workers to maneuver lines in tight spaces and around obstacles.
From crane rigging and material handling to scaffolding support and fall protection, synthetic ropes have become essential tools in the construction and industrial sectors. Their reliability and performance under demanding conditions help keep projects on track and workers safe.
Outdoor Recreation and Sports Applications
Step into the world of adventure sports and outdoor recreation, where synthetic ropes are the unsung heroes. Whether you're scaling a sheer rock face, sailing across a pristine lake, or exploring a remote canyon, you'll likely encounter synthetic ropes in action:
- Climbing ropes, crafted to be lightweight, low-stretch, and able to withstand intense fall forces.
- Sailing lines, designed for minimal stretch, high strength, and resistance to UV damage and saltwater.
- Canyoneering ropes, engineered to handle abrasion from rough rock surfaces and remain strong even when wet.
The advent of synthetic ropes has opened up new frontiers in outdoor recreation, enabling enthusiasts to push their limits safely. From kernmantle ropes for climbing to static lines for caving, these materials have become trusted companions on countless adventures.
As you can see, synthetic ropes have become indispensable across a wide range of industries and applications. Their unique properties, such as high strength, low weight, durability, and resistance to the elements, have made them the material of choice for tackling challenges in marine environments, construction sites, and outdoor pursuits.
The next time you see a rope in action, take a moment to appreciate the incredible science and engineering behind these synthetic marvels. They may appear simple at first glance, but the impact they've had on our world is truly remarkable. As technology continues to advance, we can only imagine the new heights synthetic ropes will help us reach in the future.• SS tube thimble+1.5M sleeve, end with lug.
MATERIAL: UHMWPE
CONSTRUCT: 12-Strands
ELONGATION: 4.80%
Situations Where Steel Wire Remains the Preferred Choice
While synthetic ropes have gained popularity in many applications, there are still situations where steel wire remains the go-to choice. Let's explore the unique properties of steel wire that make it indispensable in certain industries and environments.

Durability and Corrosion Resistance
Picture this: you're standing on an offshore oil rig, surrounded by the harsh, salty sea air. The ropes and cables supporting the massive structure must withstand not only the weight of the equipment but also the constant exposure to corrosive elements. This is where steel wire truly shines.
Steel wire, particularly stainless steel wire, offers unparalleled durability and corrosion resistance compared to other materials. The chromium content in stainless steel forms a protective oxide layer on the surface, preventing rust and deterioration even in the most challenging environments. This makes steel wire the preferred choice for applications such as:
- Marine and offshore structures, where the wire must endure constant exposure to saltwater and harsh weather conditions.
- Chemical processing plants, where the wire may come into contact with corrosive substances and hazardous materials.
- Outdoor construction projects, where the wire must withstand UV radiation, temperature fluctuations, and moisture.
The durability and corrosion resistance of steel wire translate into long-lasting performance and reduced maintenance requirements. While the initial cost may be higher compared to synthetic ropes, the extended lifespan and minimal upkeep of steel wire often make it the more cost-effective choice in the long run.
High Strength and Versatility
Have you ever marveled at the sheer size and strength of a suspension bridge or a towering construction crane? Chances are, steel wire played a crucial role in making those engineering feats possible. Steel wire's exceptional tensile strength and versatility make it the material of choice for applications that demand uncompromising performance.
The high tensile strength of steel wire allows it to support immense loads without breaking or stretching. This strength, combined with steel's ability to be woven, twisted, or formed into various configurations, makes it ideal for applications such as:
- Wire ropes and cables used in cranes, elevators, and mining operations, where the wire must lift and move heavy objects safely and reliably.
- Suspension bridges and cable-stayed structures, where the wire must bear the weight of the entire bridge deck and distribute the load evenly.
- Automotive and aerospace components, where the wire must withstand high stress and vibration while maintaining precise tolerances.
The versatility of steel wire extends beyond its strength. It can be coated with various materials, such as zinc (galvanized wire) or plastic, to enhance its durability and resistance to specific environmental factors. This adaptability makes steel wire suitable for a wide range of industries and applications.
So, the next time you find yourself in a situation that demands uncompromising strength, durability, and versatility, remember the unwavering reliability of steel wire. Whether you're designing a structure that must stand the test of time or developing a product that pushes the boundaries of engineering, steel wire remains a trusted ally in your pursuit of excellence.
While synthetic ropes have their place in the world of modern materials, steel wire's unique combination of durability, corrosion resistance, high strength, and versatility ensures that it will continue to play a vital role in shaping our world for years to come. As we look towards the future, it's clear that steel wire's legacy of strength and reliability is here to stay.
Explore Premium Quality Rope Solutions for Every Industry
Elevating Brands Through Customized, Innovative Rope Solutions
Learn MoreIn comparing synthetic rope and steel wire, it's evident that synthetic rope offers several benefits, such as a higher strength-to-weight ratio, superior flexibility, and corrosion resistance. Its lightweight and handling ease make it preferable in marine, offshore, and recreational settings. Conversely, steel wire remains superior in high-temperature environments and applications requiring extreme tensile strength, like steel wire clamps. For a detailed look at wire cable clamps and their best uses in different scenarios, the provided insights will bolster your decision-making process.
Inquire About Custom Rope Solutions
Fill out the inquiry form above to learn more about customised synthetic ropes and steel wire solutions. Whether for marine, industrial, or recreational use, our team is ready to provide expert guidance tailored to your needs.