Have you ever wondered about the intricate world of single braided ropes? From the versatile 12-strand to the specialised 3-strand, and even the innovative hollow braids with 16, 24, or 32 strands used for protective sleeving, these marvels of engineering are the unsung heroes of countless industries. At iRopes, we're passionate about unlocking the full potential of single braided rope and single braid line solutions for our wholesale customers worldwide.
Imagine a rope that combines strength, flexibility, and customisation possibilities - that's the power of single braided rope. Whether you're rigging a yacht, securing heavy machinery, or seeking the perfect protective sleeve for your cables, understanding the nuances of different strand configurations can make all the difference. In this post, we'll explore the fascinating world of single braided ropes, from the robust 8-strand to the smooth 16-strand, and reveal how hollow braid ropes are revolutionising protective sleeving across industries.
Join us as we unravel the secrets of single braided rope technology and discover how iRopes' expertise in custom rope solutions can elevate your projects to new heights. Are you ready to reimagine what's possible with the right rope?
Understanding Single Braided Rope: Construction and Uses
Have you ever marvelled at the strength and versatility of a single braided rope? As someone who's spent years working with various rope types, I can tell you that single braided ropes are truly remarkable. Let's dive into the world of these ingenious cordage solutions and explore what makes them so special.
What is a Single Braided Rope?
A single braided rope is like a beautifully choreographed dance of fibres. Imagine strands of material, typically an even number, intertwining in a circular pattern. As they rotate clockwise and counter-clockwise, they create a strong, unified structure that's both flexible and durable.
Unlike their twisted or double-braided cousins, single braided ropes have a unique construction that offers several advantages. Their seamless design allows for impressive strength-to-weight ratios, making them a go-to choice for many applications.
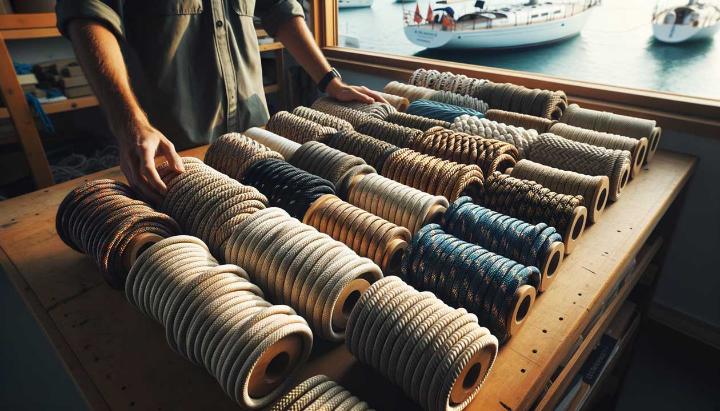
Types of Single Braided Ropes and Materials
The world of single braided ropes is diverse, with various materials offering different properties. Let's explore some common types:
- Polyester single braids: Known for their excellent UV resistance and low stretch, perfect for outdoor applications.
- Nylon single braids: Prized for their elasticity and shock-absorption, ideal for dynamic loads.
- UHMWPE single braids: Ultra-high-molecular-weight polyethylene ropes that offer incredible strength-to-weight ratios.
Each material brings its unique characteristics to the table, allowing us to tailor ropes to specific needs. For instance, I once worked on a marine project where we needed a rope that could withstand harsh saltwater conditions. A polyester single braid was the perfect solution, offering excellent resistance to UV degradation and maintaining its strength even after prolonged exposure to the elements.
Advantages and Applications of Single Braided Rope
What makes single braided ropes stand out in the crowded world of cordage? Here are some key advantages:
- Lightweight yet strong: Their efficient construction offers an excellent strength-to-weight ratio.
- Flexibility: Single braids are incredibly pliable, making them easy to handle and work with.
- Easy splicing: The braided construction allows for simple and secure splicing techniques.
- Versatility: These ropes can be used in a wide range of applications across various industries.
From my experience, I've seen single braided ropes excel in numerous fields. They're commonly used in marine environments for rigging and mooring, in the construction industry for pulling and lifting, and even in recreational activities like climbing and camping.
Did you know? Single braided ropes can be customized with different strand counts, like 8, 12, or 16 strands, each offering unique characteristics to suit specific needs.
As we delve deeper into the world of single braided ropes, you'll discover the incredible versatility and potential these ropes offer. Whether you're a professional in need of reliable cordage solutions or an enthusiast looking to understand more about rope construction, single braided ropes are certainly worth your attention. Have you ever used a single braided rope in your projects? I'd love to hear about your experiences!
Exploring Single Braided Rope Variations
As we dive deeper into the world of single braided ropes, it's fascinating to discover the diverse range of variations available. Each type offers unique characteristics that cater to specific needs across various industries. Let's explore some of the most common single braided rope variations and understand how they differ in construction and application.
Types of Single Braided Ropes
Single braided ropes come in various strand configurations, each offering distinct advantages. Here are some popular variations:
- 12-strand single braided rope: Known for its excellent balance between strength and flexibility, this rope is a popular choice for marine applications and general-purpose use.
- 8-strand single braided rope: Offers a good compromise between cost and performance, making it suitable for a wide range of applications where moderate strength is required.
- 16-strand single braided rope: Provides enhanced smoothness and roundness, making it ideal for applications requiring low friction and easy handling.
- 3-strand single braided rope: While less common, this variation offers unique properties and is often used in specialized applications.
In my experience working with various rope types, I've found that the 12-strand configuration often provides the best all-around performance for most applications. However, the choice ultimately depends on your specific needs and the intended use of the rope.
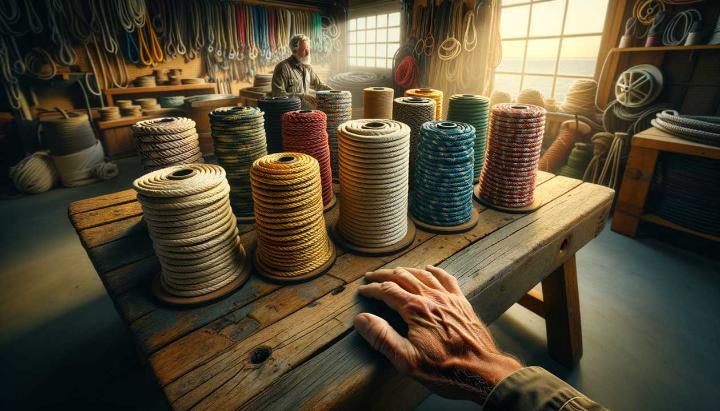
Techniques for Creating Unique Braids
The art of rope braiding goes beyond just the number of strands. Various techniques can be employed to create unique braids with specific properties:
- Solid braid: This technique creates a dense, compact rope with excellent abrasion resistance and minimal stretch.
- Diamond braid: Characterized by its distinctive diamond pattern, this braid offers a good balance of strength and flexibility.
- Hollow braid: This technique creates a rope with a hollow core, making it ideal for applications where a lightweight yet strong rope is needed.
Have you ever tried your hand at rope braiding? It's a fascinating process that requires skill and patience. I remember the first time I attempted a diamond braid - it took me several tries to get it right, but the result was a beautiful and functional rope that I still use for various projects.
Did you know? Hollow braid ropes with 16, 24, or 32 strands are often used as protective sleeving for other ropes or cables, providing an extra layer of durability and safety.
Understanding these variations and techniques is crucial when selecting the right single braided rope for your project. Whether you're working on a marine application, a construction project, or even a DIY endeavor, the type of braid you choose can significantly impact the rope's performance and longevity.
What's your experience with different single braided rope variations? Have you found a particular type that works best for your needs? Share your thoughts and let's continue exploring the fascinating world of rope construction together!
Hollow Braid Rope for Protective Sleeving: An Overview
As we delve deeper into the world of single braided ropes, we encounter a fascinating variation: hollow braid rope. This unique construction offers exceptional versatility, particularly when it comes to protective sleeving. Let's explore how this innovative rope design is revolutionising safety and efficiency across various industries.
Hollow braid rope, as the name suggests, features a tubular construction with a hollow core. This design allows for remarkable flexibility and the ability to flatten when compressed, making it ideal for protective applications. Imagine a rope that can expand to envelop and shield other ropes, cables, or hoses - that's the magic of hollow braid rope used for protective sleeving.
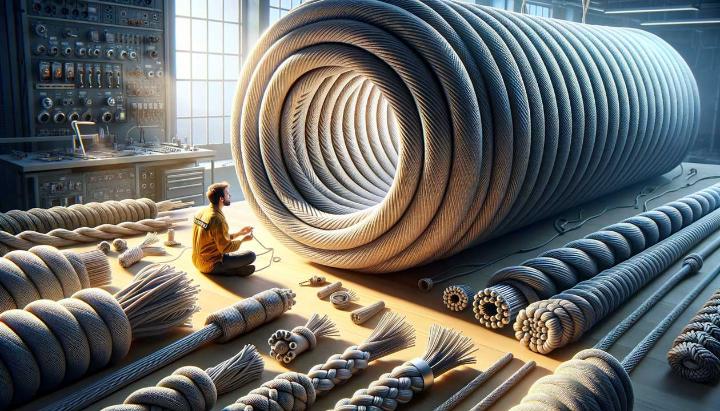
The beauty of hollow braid rope lies in its ability to provide robust protection without compromising on flexibility or ease of use. I remember a time when I was working on a marine project, and we needed to protect a bundle of hydraulic hoses from abrasion and UV damage. The hollow braid rope sleeving we used not only shielded the hoses effectively but also made the entire assembly easier to handle and route through tight spaces on the vessel.
Understanding HMPE and Polypropylene Options
When it comes to hollow braid rope for protective sleeving, two materials stand out: HMPE (High-Molecular-Weight Polyethylene) and Polypropylene. Each offers unique advantages, catering to different needs and applications.
- HMPE hollow braid rope: Renowned for its incredible strength-to-weight ratio, HMPE offers superior abrasion resistance and durability. It's the go-to choice for high-stress environments where maximum protection is crucial.
- Polypropylene hollow braid rope: Lightweight and buoyant, polypropylene excels in marine applications. It's also highly resistant to chemicals and moisture, making it ideal for industrial settings where exposure to harsh substances is a concern.
Choosing between HMPE and polypropylene often comes down to the specific demands of your project. For instance, in offshore oil rigs where safety is paramount and exposure to chemicals is common, HMPE hollow braid rope might be the preferred choice for protective sleeving. On the other hand, for recreational boating where buoyancy and UV resistance are key, polypropylene could be the better option.
Applications and Benefits of Protective Rope Sleeving
The versatility of hollow braid rope for protective sleeving extends across numerous industries and applications. Here are some common scenarios where this innovative solution shines:
- Marine industry: Protecting mooring lines, anchor ropes, and hydraulic hoses from abrasion and UV damage.
- Construction: Shielding power cables and utility lines from wear and tear on job sites.
- Forestry: Safeguarding equipment cables and hoses from branches and rough terrain.
- Offshore oil and gas: Providing an extra layer of protection for critical lines and cables in harsh marine environments.
The benefits of using hollow braid rope for protective sleeving are numerous:
- Enhanced durability: By shielding ropes and cables from abrasion, UV rays, and chemical exposure, protective sleeving significantly extends their lifespan.
- Improved safety: The added layer of protection reduces the risk of accidents caused by worn or damaged ropes and cables.
- Cost-effectiveness: While there's an initial investment, the extended lifespan of protected equipment translates to long-term cost savings.
- Versatility: Hollow braid rope sleeving can be easily installed, removed, and reused as needed, offering flexibility in various applications.
Did you know? The number of strands in a hollow braid rope (16, 24, or 32) affects its flexibility and coverage. More strands generally result in a smoother, more flexible sleeve that provides better protection against smaller particles and debris.
As we continue to push the boundaries of what's possible in various industries, the role of hollow braid rope in protective sleeving becomes increasingly crucial. Its ability to safeguard critical equipment while maintaining flexibility and ease of use makes it an invaluable tool in our arsenal.
Have you ever used hollow braid rope for protective sleeving in your projects? What challenges did it help you overcome? Share your experiences and let's discuss how this innovative solution is shaping the future of safety and efficiency across industries!
Single Braid Line and Single Wire Rope Sling Solutions
When it comes to heavy-duty lifting and rigging applications, single braid lines and wire rope slings are the unsung heroes of the industry. As someone who's spent years working with these robust solutions, I can tell you that choosing the right sling can make all the difference in your project's success and safety.
Types of Wire Rope Slings
Wire rope slings come in various configurations, each designed for specific lifting challenges. Let's explore the two main categories:
- Single-part wire rope slings: These workhorses consist of a single length of wire rope with end fittings. They're ideal for straightforward lifts and offer excellent strength-to-weight ratios.
- Multi-part wire rope slings: When you need extra lifting power or flexibility, these slings use multiple legs of wire rope. They're perfect for handling oddly shaped or heavy loads.
But the real game-changer in recent years has been the introduction of braided wire rope slings. These innovative solutions combine the best of both worlds, offering unique advantages that have revolutionised the lifting industry.
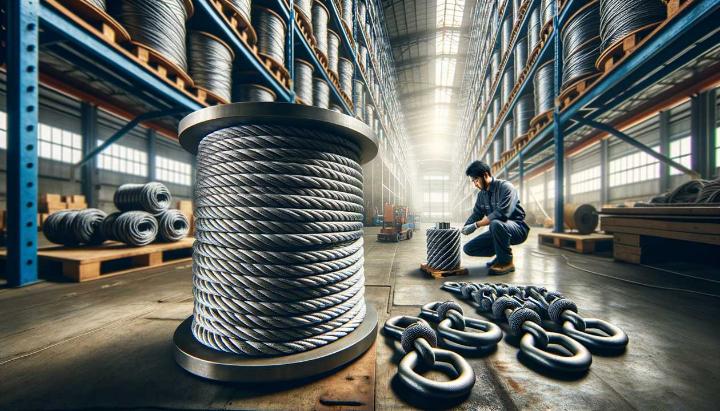
Advantages of Braided Wire Rope Slings
Braided wire rope slings have quickly become a favourite among riggers and lifting professionals. Here's why:
- Unmatched flexibility: The braided construction allows these slings to bend and flex more easily than traditional wire ropes, making them ideal for complex lifts.
- Superior load distribution: The braided design spreads the load more evenly across the sling, reducing stress on individual wires and extending the sling's lifespan.
- Enhanced grip: The textured surface of braided slings provides a better grip on loads, reducing the risk of slippage during lifts.
I remember a particularly challenging project where we needed to lift an irregularly shaped piece of machinery. The braided wire rope sling we used conformed perfectly to the load's contours, providing a secure lift that would have been much riskier with a traditional sling.
Choosing the Right Wire Rope Sling
Selecting the perfect wire rope sling for your job isn't just about picking the strongest option. Here are some crucial factors to consider:
- Load capacity: Always choose a sling rated well above your maximum expected load weight. Safety should never be compromised.
- Environmental conditions: Consider factors like temperature extremes, chemical exposure, or abrasive environments that could affect the sling's performance.
- D/d ratio: This crucial measurement refers to the diameter of the bend in relation to the rope's diameter. A higher D/d ratio means less stress on the rope during use.
One of the most important lessons I've learned over the years is the significance of regular inspections. Always adhere to ASME standards for wire rope sling inspection and rejection criteria. A well-maintained sling is a safe sling.
Did you know? The D/d ratio is critical in determining a sling's working load limit. A larger D/d ratio allows for a higher working load limit, as it reduces the stress on the rope fibres during bending.
Whether you're dealing with single braid lines or complex wire rope sling solutions, understanding these key concepts will help you make informed decisions for your lifting projects. Remember, the right sling not only ensures efficiency but also prioritises safety in your operations.
Have you had experience with different types of wire rope slings? What challenges have you faced in selecting the right sling for your projects? Share your thoughts and let's continue this fascinating discussion on lifting and rigging solutions!
Dive into the fascinating world of single braided rope and discover the various configurations like the 12-strand, 8-strand, 16-strand, and 3-strand single braided rope, each delivering unique strength and flexibility. Explore the protective benefits of hollow braided rope with 16, 24, and 32 strands, ideal for safeguarding cables and hoses. Learn about the advantages of single braid line and the specific uses of single wire rope sling in lifting and rigging applications, highlighting how iRopes' customized solutions can meet your specific needs. Whether for marine, construction, or industrial use, selecting the right single braid solution can significantly enhance performance and safety.
Looking for Custom Single Braided Rope Solutions?
Please fill out the form above to get in touch with our experts and explore how iRopes can provide the perfect rope solutions tailored to your specific applications. Your journey to superior rope performance starts here!