Imagine being stranded in the unforgiving Australian Outback, your 4x4 hopelessly bogged in deep sand. In that critical moment, the difference between a quick recovery and a dangerous ordeal often comes down to one crucial piece of equipment: your dynamic recovery rope.
When it comes to off-road vehicle recovery, not all ropes are created equal. The varying rope construction types and materials can mean the difference between a safe, efficient recovery and a potentially catastrophic equipment failure. That's why understanding the science behind rope engineering is crucial for anyone serious about off-road adventures or professional recovery operations.
As pioneers in advanced rope manufacturing, erin rope corp has spent years perfecting the art of creating high-performance recovery solutions. From the revolutionary elasticity of our dynamic recovery ropes to our innovative approach to rope construction, we're revolutionising the way people think about "Made in China" quality in the rope industry.
In this comprehensive guide, we'll explore the fascinating world of dynamic recovery ropes, delve into various rope construction types, and showcase how our cutting-edge manufacturing processes are setting new standards in rope performance and reliability. Whether you're an off-road enthusiast or a professional recovery operator, understanding these crucial differences could save you from a sticky situation when it matters most.
Understanding Dynamic Recovery Ropes
Have you ever found yourself stuck in challenging terrain during an off-road adventure? That's where dynamic recovery ropes come to the rescue. Unlike traditional static ropes, dynamic recovery ropes are specifically engineered to provide a safer and more effective vehicle recovery solution.
How Dynamic Recovery Ropes Work
The magic of dynamic recovery ropes lies in their unique ability to stretch between 20-30% of their original length. This remarkable elasticity acts like a giant rubber band, storing kinetic energy during the initial pull and releasing it gradually to help extract stuck vehicles with smooth, controlled force.
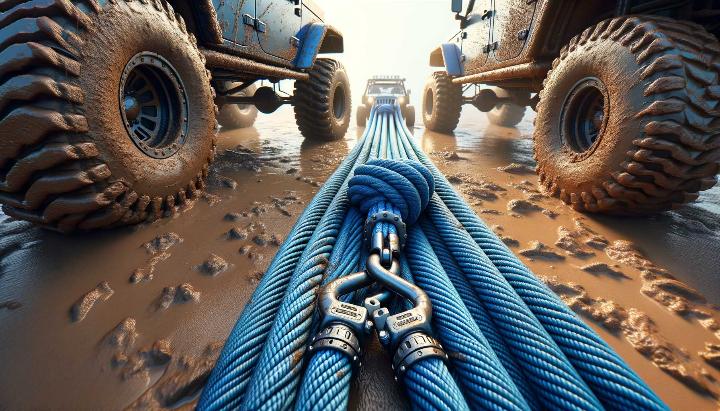
Dynamic vs Static Recovery: Key Differences
- Energy absorption - Dynamic ropes absorb shock loads gradually, reducing stress on recovery points and making the process safer
- Stretch capacity - The 20-30% stretch range provides optimal energy storage for effective vehicle extraction
- Safety features - Built-in elongation helps prevent sudden jerks that could damage vehicles or snap equipment
Choosing the Right Recovery Rope
When selecting a dynamic recovery rope, remember that your rope's minimum breaking strength should be at least three times your vehicle's gross weight. For most 4x4s, a rope length between 20-30 feet offers the perfect balance of maneuverability and effective energy transfer.
Always inspect your dynamic recovery rope before each use and replace it if you notice any signs of significant wear, such as fraying or discoloration.
Whether you're tackling mud, snow, sand, or rocky terrain, a properly rated dynamic recovery rope can mean the difference between a minor setback and a major ordeal during your off-road adventures.
Understanding Rope Construction Types
Now that we understand how dynamic recovery ropes work, let's dive into the fascinating world of rope construction types. Have you ever wondered why some ropes feel smoother while others have a more textured surface? The secret lies in their construction method.
Basic Rope Construction Methods
Just like a master chef's recipe, each rope construction type brings its own unique characteristics to the table. Here are the main types you'll encounter:
- Single braided (solid braid) - Features a simple yet reliable construction where strands are interwoven in a tight pattern, perfect for general-purpose applications
- Double braided - Combines an inner core with an outer braided cover, offering exceptional strength and handling characteristics
- Kernmantle - A sophisticated design featuring a load-bearing core (kern) protected by a woven outer sheath (mantle), commonly used in climbing ropes
- Twisted - The traditional three-strand construction that's been trusted for centuries, offering good grip and easy splicing
- Hollow core - Features a hollow center that allows for easy splicing and excellent shape retention
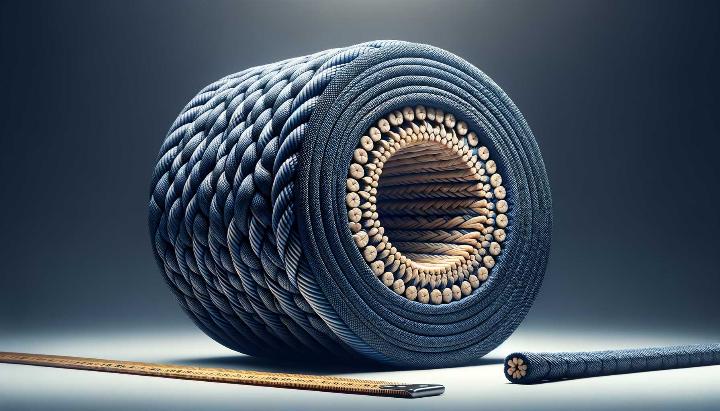
Performance Impact of Construction Types
The way a rope is constructed dramatically affects its performance characteristics. Consider these key factors when evaluating different construction types:
- Strength-to-weight ratio - Double braided and kernmantle constructions typically offer the best strength for their weight
- Flexibility and handling - Braided constructions generally provide better flexibility and smoother handling
- Abrasion resistance - Solid braid and double braid constructions often excel in rough conditions
- UV resistance - Tighter constructions like double braid provide better protection against sun damage
Choosing the Right Construction
Selecting the optimal rope construction depends heavily on your specific needs. For vehicle recovery, double braided or kernmantle constructions often provide the best balance of strength and energy absorption. Working on a boat? A twisted construction might be your best bet for its splicing capabilities and traditional handling characteristics.
When choosing a rope construction, consider not just the immediate application but also the environment where you'll be using it. Factors like exposure to UV rays, abrasive surfaces, and moisture should influence your decision.
iRopes' Manufacturing Excellence and Expertise
When it comes to manufacturing high-quality ropes, experience matters. Over the past 15 years, iRopes has been perfecting the art and science of rope making, combining traditional craftsmanship with cutting-edge technology. Have you ever wondered what makes some ropes consistently outperform others in demanding conditions?
Advanced Rope Manufacturing Process
At the heart of our manufacturing excellence lies a meticulous four-phase process that ensures every rope meets the highest standards of quality and performance. Each phase is carefully monitored and controlled by our expert technicians who understand that there's no room for compromise when it comes to rope reliability.
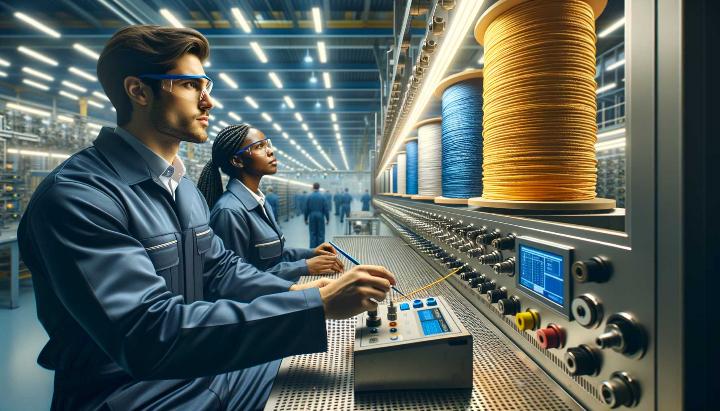
Quality Control and Material Innovation
Our commitment to excellence begins with material selection. We exclusively use premium synthetic fibers that offer superior strength-to-weight ratios and exceptional durability:
- UHMWPE (Ultra-High-Molecular-Weight Polyethylene) - Provides incredible strength while maintaining lightweight properties
- Technora™ - Offers outstanding heat resistance and dimensional stability
- Kevlar™ - Delivers unmatched tensile strength and cut resistance
- Vectran™ - Ensures excellent creep resistance and minimal stretch
- Polyamide and Polyester - Provides versatility and cost-effectiveness for various applications
Each rope undergoes rigorous testing, including break strength verification, UV resistance checks, and abrasion resistance assessments, ensuring it meets or exceeds industry standards.
Our innovative coating options further enhance rope performance, offering protection against UV damage, moisture, and abrasion. For more details, explore the ultimate guide to nylon and polyester braided rope. Whether you need a rope for marine applications, industrial use, or outdoor adventures, we have the expertise to deliver a solution that exceeds your expectations.
Setting New Standards in Rope Manufacturing
As a proud Chinese manufacturer, we're committed to challenging preconceptions about "Made in China" products. Every rope that leaves our facility represents our dedication to excellence and innovation in rope manufacturing. We invite you to discover how iRopes compares to leading US rope manufacturers. The proof is in the performance - just ask any of our satisfied customers across the globe who rely on our ropes daily in the most demanding applications.
Custom Rope Manufacturing Options at Erin Rope
Every industry has its unique rope requirements, and that's where customization becomes crucial. Have you ever struggled to find a rope that perfectly matches your specific application needs? Let's explore how our tailored solutions can address your exact requirements.
Material and Construction Customization
The foundation of any custom rope solution starts with selecting the right materials and construction method. Our engineering team works closely with clients to understand their unique challenges and recommend the optimal combination:
- Material selection - From high-performance synthetics to traditional natural fibers, each material is chosen based on your specific strength, durability, and environmental requirements
- Construction method - Whether you need the flexibility of double-braid or the durability of kernmantle, we'll match the construction to your application. For more on choosing the right construction, check our mastering rope loop splice and steel wire loop clamp tips.
- Surface treatments - Custom coatings and finishes to enhance UV resistance, water repellency, or grip characteristics
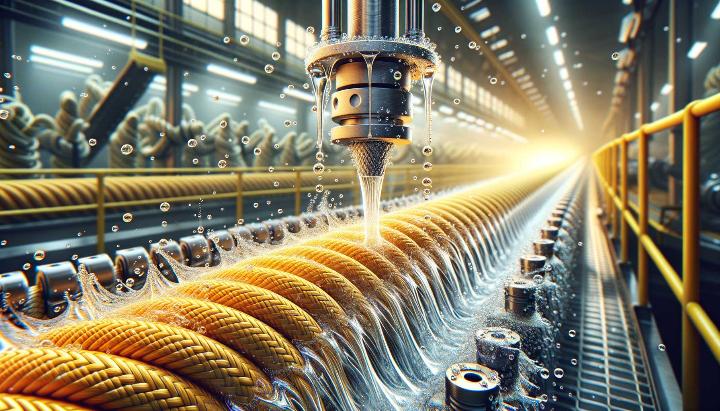
Size and Length Specifications
Every detail matters when it comes to rope performance. Our customization options include:
- Diameter precision - Available in increments as small as 0.1mm to meet exact specifications
- Custom lengths - From short assemblies to continuous lengths exceeding 1000 meters
- Color coding - Multiple color options for easy identification and brand alignment
Our technical team can help you determine the optimal specifications based on your working load requirements and safety factors.
Special Applications and Requirements
From marine rigging to industrial lifting, we've developed custom solutions across diverse industries. Here are some examples:
- Marine applications - Salt-resistant ropes with specialized coatings for harsh offshore environments
- Industrial lifting - High-visibility ropes with certified break strengths and safety factors
- Adventure sports - Lightweight, high-strength ropes with specific elongation characteristics
- Defense sector - Specialized ropes meeting strict military specifications and requirements
Whether you need a specialized rope for a unique application or a modified version of our standard products, our engineering team is ready to develop a solution that precisely matches your requirements. Contact us to discuss your specific needs and let's create the perfect rope solution together.
```htmlExploring the potential of dynamic recovery rope technology reveals its unmatched benefits for off-road recovery, harnessing unique stretch and recovery properties for safer vehicle extraction. iRopes, a leader in rope manufacturing, excels in producing top-tier, high-performance ropes using synthetic fibres like UHMWPE, Technora™, and Kevlar™, among others. Our extensive range of rope construction types, from braided to twisted, significantly impacts performance, strength, and flexibility, tailored to specific applications. With erin rope corp's capabilities in customised solutions, ropes are precisely crafted to meet diverse industry needs. Discover the supreme quality of our "Made in China" ropes, offering resilience, durability, and astonishing value. Reach out to iRopes for deeper insights into how our dynamic recovery rope can elevate your projects.
Contact Us for Tailored Rope Solutions
For more tailored rope solutions and to discuss specific applications, fill out the inquiry form above. Let iRopes guide you to the perfect rope, customised precisely for your needs.
```