Have you ever wondered why some ropes and cables seem to unravel at the worst possible moment? The secret lies in the often-overlooked detail of rope and cable ends. In the world of rigging and industrial applications, choosing the right end can mean the difference between a successful operation and a costly disaster.
At iRopes, we've spent 15 years perfecting the art of rope-making, offering over 2,348 cordage options for marine, racing sports, industrial, and safety uses. But our expertise doesn't stop at the rope itself. We understand that the true strength of a rope lies in its weakest point - often the ends.
In this comprehensive guide, we'll unravel the mysteries of manila rope ends, polypropylene rope ends, and wire cable ends. We'll explore why choosing the right end is crucial for your specific application, whether you're securing a yacht in choppy waters or rigging heavy machinery in a construction site.
From whipped ends to heat-sealed finishes, from melted tips to swaged terminations, we'll cover it all. And we'll reveal how iRopes' custom end solutions, crafted from cutting-edge synthetic fibres like UHMWPE and Kevlar™, are setting new standards in the industry.
So, whether you're a seasoned rigger or a DIY enthusiast, buckle up. You're about to discover how the right rope end can elevate your project from good to great, all while showcasing the excellence of "Made in China" craftsmanship.
Types of Manila Rope Ends: Understanding the Differences
When it comes to securing and finishing manila ropes, understanding the various end types is crucial for both safety and functionality. Let's dive into the world of manila rope ends and explore the different options available to you.
Natural vs. Synthetic Manila Rope Finishes
Before we delve into specific end types, it's important to distinguish between natural manila and synthetic alternatives like ProManila. Natural manila rope, crafted from Abaca fibres native to the Philippines, offers a classic look and feel. On the other hand, ProManila, made from polypropylene, provides enhanced durability and resistance to rot.
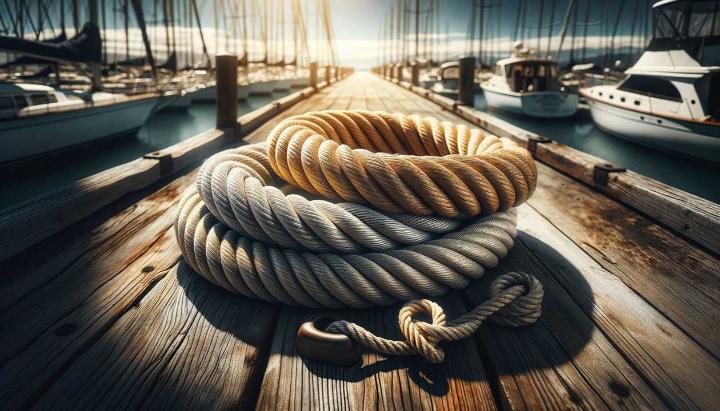
Identifying and Selecting the Right Manila Rope End
Now, let's explore the four main types of manila rope ends:
- Whipped ends: This classic method involves tightly wrapping thin twine around the rope's end to prevent fraying. It's simple, effective, and widely used in marine applications.
- Seized ends: Similar to whipping, seizing involves wrapping the rope end with its own fibres or a separate cord. This technique creates a neat, professional finish.
- Back spliced ends: A more complex but highly secure method where the rope's strands are woven back into themselves, creating a robust and attractive finish.
- Heat-sealed ends: While more common with synthetic ropes, heat-sealing can also be applied to manila ropes treated with certain coatings. This method fuses the fibres together, preventing fraying.
Choosing the right end finish depends on your specific application, the rope's environment, and personal preference. For instance, whipped ends are ideal for quick, temporary solutions, while back spliced ends offer superior strength for heavy-duty applications.
Pro tip: Use the marker tape method to quickly identify if you're working with natural manila or synthetic rope. Simply burn a small section of the rope - natural fibres will produce ash, while synthetics will melt.
Remember, proper rope end finishing not only enhances the rope's appearance but also significantly impacts its performance and longevity. Whether you're rigging a sailboat or securing a load, taking the time to understand and implement the right manila rope end will pay off in the long run.
Exploring Polypropylene Rope Ends Options
When it comes to polypropylene ropes, choosing the right end treatment is crucial for both functionality and longevity. As a sailor who's spent countless hours working with various ropes, I can attest to the importance of proper rope end management. Let's dive into the world of polypropylene rope ends and explore the options available to you.
Sealing Methods for Polypropylene Rope
Polypropylene rope's unique properties make it resistant to moisture and chemicals, but it still requires proper sealing to prevent fraying. Here are some effective methods:
- Heat sealing: My go-to method for quick and effective sealing. Simply use a lighter or heat gun to carefully melt the end, creating a solid cap.
- Tape wrapping: For a temporary fix, wrapping the end with a strong, waterproof tape can prevent fraying.
- Specialized rope end products: Plastic end caps or heat shrink tubing can provide a professional finish and added protection.
Remember, the key is to find a balance between effectiveness and ease of application for your specific needs.
Preventing Fraying in Polypropylene Rope
Fraying can significantly reduce the lifespan of your rope. Here are some tried-and-true prevention methods:
- Back-splicing: This technique involves weaving the rope's end back into itself, creating a secure and attractive finish.
- Whipping: Using a thin cord or thread to tightly wrap the rope's end can effectively prevent fraying.
- Chemical sealants: Specially formulated glues or epoxies can be applied to the rope end for a durable seal.
Pro tip: When choosing a fraying prevention method, consider the rope's intended use. For high-stress applications, a combination of back-splicing and heat sealing can provide superior strength and durability.
Rope End Products and Accessories
The market offers a variety of products designed specifically for polypropylene rope ends:
- Plastic clamps: These provide a clean finish and can be easily attached or removed.
- Metal crimps: For heavy-duty applications, metal crimps offer superior strength and security.
- Heat shrink tubing: This versatile option not only seals the end but can also be used to colour-code your ropes.
When selecting rope end products, consider factors such as the rope's diameter, intended use, and environmental conditions it will face. To learn more about the versatility of polypropylene rope, check out our top uses of 1.5 inch polypropylene rope and nylon rope.
As we wrap up our exploration of polypropylene rope ends, remember that proper end treatment is not just about aesthetics – it's about safety and longevity. Whether you're rigging a sailboat or securing cargo, taking the time to choose and apply the right end treatment will pay dividends in the long run. Have you tried any of these methods? What works best for your polypropylene rope applications?
Choosing the Best Wire Cable Ends for Your Needs
When it comes to electrical installations, selecting the right wire cable ends can make all the difference in safety, efficiency, and longevity. As an electrician with over a decade of experience, I've seen firsthand how proper connector choice can prevent costly failures and ensure reliable connections. Let's dive into the world of wire cable ends and explore how to choose the best options for your projects.
Types of Wire Connectors and Their Applications
Wire connectors come in various shapes and sizes, each designed for specific applications. Here are some common types you'll encounter:
- Wire nuts: These twist-on connectors are perfect for joining two or more wires in residential wiring. They're colour-coded for easy size identification.
- Crimp connectors: Ideal for automotive and marine applications, these connectors create a secure, permanent connection when crimped with the proper tool.
- Terminal blocks: These versatile connectors allow for easy wire organisation and are commonly used in industrial control panels.
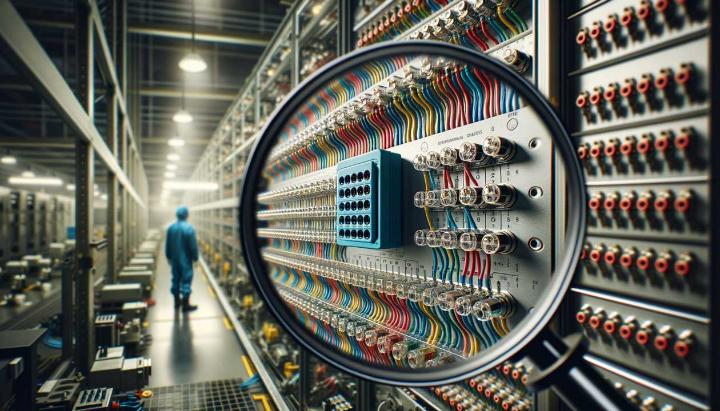
Choosing the right connector depends on factors like the environment, current load, and ease of maintenance. For instance, in a high-vibration environment like a vehicle, crimp connectors would be more suitable than wire nuts.
Factors to Consider When Selecting Cable Ends
To ensure you're using the best wire cable ends for your application, consider these key factors:
- Wire gauge: The thickness of your wire determines the appropriate connector size. Using the wrong size can lead to loose connections or overheating.
- Current rating: Ensure your chosen connector can handle the expected current flow without overheating or failure.
- Environmental conditions: Will the connection be exposed to moisture, extreme temperatures, or chemicals? Choose connectors rated for your specific environment.
- Ease of installation: Consider how often you'll need to access or modify the connection. Some connectors, like lever nuts, offer tool-free installation and removal.
Pro tip: Always use a wire gauge chart to match your wire size to the correct connector. This simple step can prevent many common wiring issues.
Remember, the goal is to create a secure, long-lasting connection that meets all safety standards. Don't hesitate to consult manufacturer specifications or seek advice from a professional if you're unsure about the best connector for your needs.
By carefully considering these factors and choosing high-quality connectors, you'll ensure your electrical installations are safe, efficient, and built to last. Have you encountered any challenges with wire cable ends in your projects? Share your experiences in the comments below!
iRopes' Custom End Solutions for Ropes and Cables
As a rope enthusiast who's been in the industry for over two decades, I've seen firsthand how crucial custom end solutions are for maximizing the performance and safety of ropes and cables. iRopes, with its 15 years of expertise in rope manufacturing, has truly mastered the art of creating tailored end solutions that cater to diverse industry needs.
Tailored Wire Rope Assemblies for Every Industry
One of the most impressive aspects of iRopes' custom end solutions is their ability to create wire rope assemblies that perfectly fit the unique requirements of various industries. From marine applications to heavy construction, each sector demands specific features from their ropes and cables. Let me share a few examples I've encountered:
- Marine industry: Requires corrosion-resistant end fittings that can withstand harsh saltwater environments.
- Construction: Needs high-strength terminations capable of supporting immense loads safely.
- Aerospace: Demands lightweight yet durable end solutions that meet stringent safety standards.
iRopes' custom wire rope assemblies address these diverse needs with precision, ensuring optimal performance and safety across all applications.
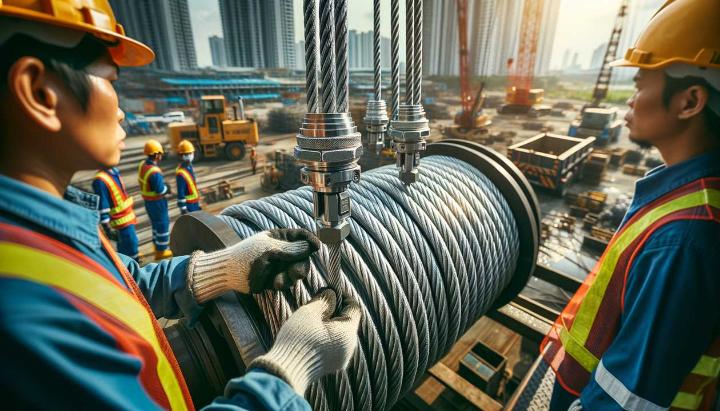
Innovative End Fitting Options for Optimal Performance
What sets iRopes apart is their extensive range of innovative end fitting options. Having worked with various manufacturers, I can confidently say that iRopes offers some of the most versatile and reliable solutions I've seen. Here's a breakdown of some popular end fittings and their unique benefits:
- Cylindrical nipples: Ideal for applications requiring a smooth, low-profile termination. They offer excellent load distribution and are often used in pulley systems.
- Shank end stops: Perfect for preventing cable slippage in tensioning systems. Their robust design ensures a secure grip even under high loads.
- Eyelets: Versatile and widely used, eyelets provide a simple yet effective connection point for various applications, from rigging to industrial machinery.
The beauty of iRopes' custom end solutions lies in their ability to combine these fittings with their expertise in synthetic fibers like UHMWPE, Technora™, and Kevlar™. This combination results in rope assemblies that are not just strong and durable, but also tailored to meet specific industry standards and performance requirements. For insight into the benefits of 3 Strand Nylon Line, check out our benefits of 3 Strand Nylon Line.
Pro tip: When choosing end fittings, consider not just the immediate application but also future maintenance needs. Some fittings, like swage terminals, offer excellent strength but may require specialized tools for replacement.
iRopes' commitment to quality assurance is evident in every custom end solution they produce. Their rigorous testing procedures ensure that each rope assembly not only meets but often exceeds industry standards. This dedication to excellence, combined with their innovative approach to customization, truly exemplifies the "Made in China" quality that iRopes stands for. Visit our page on customization to learn more about our offerings.
Have you ever encountered a situation where a standard rope or cable just didn't cut it? Share your experiences in the comments below – I'd love to hear how custom end solutions have made a difference in your projects!
When looking to choose the right ends for manila, polypropylene, and wire cables, understanding the benefits of each type is crucial for enhancing performance and safety. For manila ropes, options such as whipped, seized, back spliced, and heat-sealed ends offer different levels of security and functionality. Polypropylene rope ends can be melted, taped, spliced, or knotted, each suited for specific applications and environments. Wire cable ends, including swaged, Flemish eye spliced, and compressed ends, must be matched to the cable's use case for optimal efficiency. iRopes, with 15 years of excellence in Chinese manufacturing, offers tailor-made solutions for all these types backed by quality synthetic fibres like UHMWPE, Technora™, and Kevlar™.
Find the Perfect Ends for Your Ropes and Cables
Fill in the form above to discover how iRopes can customise manila rope ends, polypropylene rope ends, and wire cable ends based on your specific requirements, ensuring top-notch performance and durability.