In the world of industrial rigging, a fierce debate rages on: braided wire rope or steel wire rope? As a leading manufacturer of high-quality ropes, we at iRopes have seen this battle play out countless times. But what if we told you that one of these contenders consistently outperforms the other in flexibility, durability, and versatility?
Picture this: You're working on an offshore oil rig, where corrosion is your worst enemy. Or perhaps you're operating a wire cable winch system on a mobile crane, where every gram of weight matters. In these scenarios and many more, the choice between braided cable wire and traditional steel rope can make or break your operation.
In this eye-opening comparison, we'll unveil the superior qualities of braided wire rope and expose the hidden weaknesses of its steel counterpart. From lightweight handling to corrosion resistance, we'll explore why more industries are making the switch to braided solutions. Whether you're in construction, marine operations, or any field requiring reliable rigging, this analysis will revolutionise the way you think about wire ropes.
Prepare to challenge your preconceptions and discover why braided wire rope is rapidly becoming the go-to choice for professionals who demand nothing but the best. Let's unravel the truth about these two titans of the rope world and see which one truly reigns supreme.
Advantages of Braided Wire Rope over Steel Wire Rope
When it comes to choosing the right rope for your project, understanding the differences between braided wire rope and steel wire rope can make all the difference. As someone who's worked with both types extensively, I can tell you that braided wire rope often comes out on top in many applications. Let's dive into why that is.
Enhanced Flexibility and Durability
Have you ever tried to bend a steel wire rope around a tight corner? It's not easy, is it? This is where braided wire rope truly shines. The intricate braided structure allows for remarkable flexibility, making it a joy to work with in confined spaces or applications requiring frequent bending.
But flexibility isn't the only advantage. Braided wire rope also boasts impressive durability. The intertwined strands distribute stress more evenly, reducing wear and tear over time. I've seen braided ropes outlast their steel counterparts in high-stress environments, saving both time and money on replacements.
- Superior flexibility: Easily bends around tight corners and obstacles
- Enhanced durability: Resists wear and tear better than steel wire rope
- Even stress distribution: Reduces the risk of sudden failure
Improved Performance in Specific Applications
Now, let's talk about where braided wire rope really excels. In my experience, it's the go-to choice for industries like electronics, automotive, and aerospace. Why? Because it offers superior resistance to both mechanical wear and electromagnetic interference.
Think about a wire cable winch system on a mobile crane. The braided rope's lightweight nature makes it easier to handle, while its flexibility allows for smooth operation. Plus, its lower electrical resistance compared to solid wire makes it ideal for applications where conductivity is a concern.
But it doesn't stop there. Braided wire rope is also a champion in marine environments. Its corrosion-resistant properties make it perfect for offshore applications where steel wire rope would quickly succumb to rust.
Did You Know?
Braided wire rope offers better grip and reduces slippage, making it safer in many applications.
In conclusion, while steel wire rope certainly has its place, braided wire rope often proves superior in terms of flexibility, durability, and performance in specific applications. When choosing between the two, consider your project's unique requirements and environment. You might find that braided wire rope is the perfect solution you've been looking for.
Disadvantages of Steel Wire Rope Compared to Braided Wire Rope
While steel wire rope has been a stalwart in many industries for decades, it's not without its drawbacks. As someone who's worked with various types of ropes for years, I've seen firsthand how these limitations can impact projects. Let's dive into the key disadvantages of steel wire rope when compared to its braided counterpart.
Lower Flexibility and Bending Resistance
One of the most noticeable differences between steel wire rope and braided wire rope is flexibility. Steel wire rope, with its rigid structure, can be stubborn when you need it to bend. I remember a particularly challenging installation where we had to route a steel wire rope through a series of tight corners. The rope's resistance to bending made the job significantly more time-consuming and physically demanding.
In contrast, braided wire rope's construction allows for much greater flexibility. This increased pliability not only makes installation easier but also reduces the risk of kinking or permanent deformation when the rope needs to navigate corners or pulleys.
Fatigue and Wear Considerations
Steel wire rope is particularly susceptible to fatigue, especially in applications involving repeated bending or flexing. Over time, this can lead to what's known as fatigue fracture - a silent killer of rope integrity.
Did you know? Fatigue fracture is responsible for up to 90% of wire rope failures in certain applications.
I've seen steel wire ropes that looked perfectly fine on the outside but were dangerously weakened internally due to fatigue. Braided wire ropes, on the other hand, distribute stress more evenly across their structure, significantly reducing the risk of fatigue-related failures.
Weight and Handling Challenges
Let's talk about weight - it's a big deal when you're working with ropes day in and day out. Steel wire rope is notoriously heavy, which can make handling and installation a real chore. I once worked on a project where we had to manually manoeuvre long lengths of steel wire rope up several flights of stairs. Trust me, it's not an experience I'm keen to repeat!
Braided wire rope, especially those made from synthetic materials like Dyneema, can be up to 80% lighter than steel wire rope of equivalent strength. This weight difference doesn't just make life easier for the installation team; it also reduces the overall load on structures and equipment.
- Easier transportation: Lighter braided ropes are more manageable to transport to job sites.
- Reduced equipment wear: Lighter ropes put less strain on pulleys, winches, and other machinery.
- Improved safety: Lighter ropes reduce the risk of injury during handling and installation.
In conclusion, while steel wire rope certainly has its place in certain applications, its disadvantages in flexibility, fatigue resistance, and weight make braided wire rope a superior choice in many scenarios. As always, the key is to choose the right tool for the job - and increasingly, that tool is braided wire rope.
Braided Wire Rope: Excelling in Specific Applications
As we've explored the advantages of braided wire rope over its steel counterpart, it's clear that this innovative solution shines in various industries. Let's dive deeper into the specific applications where braided wire rope truly excels, showcasing its unique properties and versatility.
Unique Properties of Braided Wire Rope
Before we delve into specific use cases, it's crucial to understand what makes braided wire rope so special. Its construction, consisting of multiple interwoven strands, provides a perfect balance of strength and flexibility. This unique structure allows for even stress distribution, significantly reducing the risk of sudden failure - a common concern with traditional steel wire ropes.
One of the most impressive features of braided wire rope is its electromagnetic interference (EMI) protection capabilities. In an age where electronic systems are ubiquitous, this property is invaluable. I once worked on a project where EMI was causing significant issues with sensitive equipment. Switching to braided wire rope solved the problem almost instantly, saving countless hours of troubleshooting and potential equipment damage.
Did you know? Braided wire rope can offer up to 95% EMI shielding effectiveness, making it ideal for use in environments with sensitive electronic equipment.
Industries and Use Cases Where Braided Wire Rope Shines
Now, let's explore some specific industries and applications where braided wire rope proves its worth:
- Automotive sector: In the automotive industry, braided wire rope is a game-changer. It's commonly used in cable harnesses, where its flexibility allows for easy routing through tight spaces. The EMI protection it offers is crucial in modern vehicles packed with electronic systems.
- Construction and heavy machinery: When it comes to wire cable winch systems on mobile cranes or excavators, braided wire rope's lightweight nature and flexibility make it an excellent choice. It's easier to handle, reduces operator fatigue, and can navigate complex pulley systems with ease.
- Marine and offshore applications: The corrosion resistance of braided wire rope makes it ideal for marine environments. I've seen braided ropes outlast traditional steel ropes by years in offshore oil rigs, where the harsh, salty conditions quickly deteriorate standard steel ropes.
One particularly memorable project I worked on involved retrofitting a large industrial crane with a braided wire rope system. The improvement in performance was remarkable - the crane operator reported smoother operation, reduced vibration, and significantly less downtime for rope maintenance.
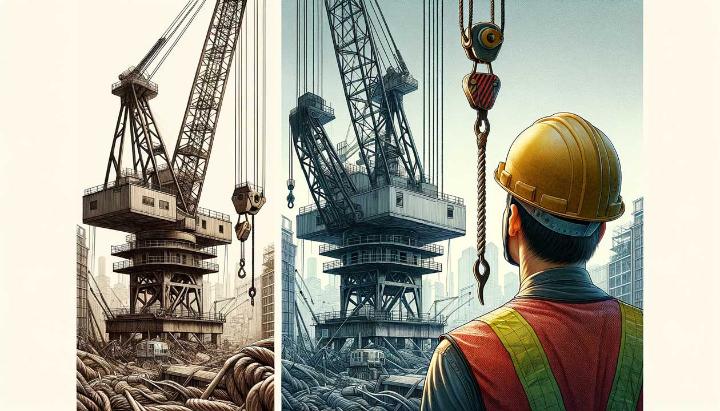
It's important to note that while braided wire rope offers numerous advantages, proper safety considerations are crucial. Always adhere to OSHA guidelines and manufacturer recommendations when using any type of wire rope. Regular inspections and maintenance are key to ensuring the longevity and safety of your braided wire rope systems.
In conclusion, braided wire rope's unique properties make it an excellent choice for a wide range of applications. Its flexibility, EMI protection, and corrosion resistance set it apart from traditional steel wire ropes. As industries continue to evolve and demand more from their equipment, braided wire rope stands ready to meet these challenges head-on. If you're interested in discovering more about such versatile rope solutions, you might want to explore the performance and applications of 2 in and 1.5 in ropes.
Likewise, insights into the unique advantages of different rope types can be crucial. Check out our guide on the best waterproof rope for your projects, which highlights the essential features for varying applications.
Moreover, understanding the key differences between rope types can greatly influence your choice. For a detailed comparison, see our article on steel wire rope vs synthetic rope to make an informed decision based on your specific needs.
When comparing braided wire rope to steel wire rope, it's clear that the braided variety excels in multiple areas, including flexibility, durability, and corrosion resistance. Braided wire rope is lightweight, straightforward to handle, and adapts to various applications, unlike its steel counterpart, which can be heavy, cumbersome, and prone to rust and kinks. This makes braided cable wire an ideal choice for environments like marine settings and applications requiring mobility, such as wire cable winch systems. With superior grip and reduced slippage, braided wire rope is often the superior option for many projects. Choose wisely based on your specific needs and conditions.
Discover the Right Rope Solution for Your Needs
If you're considering which type of rope is best for your application, fill out the form above to get in touch with our experts and receive tailored advice on selecting the perfect rope for your needs.